-
- News
- Books
Featured Books
- pcb007 Magazine
Latest Issues
Current IssueThe Hole Truth: Via Integrity in an HDI World
From the drilled hole to registration across multiple sequential lamination cycles, to the quality of your copper plating, via reliability in an HDI world is becoming an ever-greater challenge. This month we look at “The Hole Truth,” from creating the “perfect” via to how you can assure via quality and reliability, the first time, every time.
In Pursuit of Perfection: Defect Reduction
For bare PCB board fabrication, defect reduction is a critical aspect of a company's bottom line profitability. In this issue, we examine how imaging, etching, and plating processes can provide information and insight into reducing defects and increasing yields.
Voices of the Industry
We take the pulse of the PCB industry by sharing insights from leading fabricators and suppliers in this month's issue. We've gathered their thoughts on the new U.S. administration, spending, the war in Ukraine, and their most pressing needs. It’s an eye-opening and enlightening look behind the curtain.
- Articles
- Columns
- Links
- Media kit
||| MENU - pcb007 Magazine
The Brave New World of the CTO
September 21, 2022 | I-Connect007 Editorial TeamEstimated reading time: 4 minutes
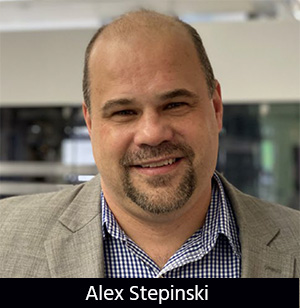
In this conversation with the I-Connect007 Editorial Team, Alex Stepinski shares his insight on how to automate the PCB fab. Spoiler alert: It doesn’t start with new equipment and panel handlers; it’s much more strategic than that. Alex details the new role of a chief technology officer in the 21st century and cautions that we don’t have nearly enough of them in the industry.
Nolan Johnson: Alex, the pressures are increasing on PCB fabs to mechanize, and it’s coming from several directions, whether it’s capabilities, labor, or staffing abilities. How does someone in charge of a PCB facility move this forward without breaking the bank, or having to hire a coder or software engineer?
Alex Stepinski: This is an interesting topic. It is the intersection of investment management: what a CFO does, and technology delivery: what a CTO does. You could say that an advanced CTO with a strong finance background is likely the key person to drive something like this in a company. You don’t even necessarily need engineers on site; you just need one person who can architect the whole thing. It’s all about intrapreneurship with the Lean startup approach. The question is: “How do I move my business plan forward to improve my efficiencies—labor, capital utilization efficiencies, return on invested capital, commodity strategy?” You need a plan for a particular process area: If we upgrade to X, what do I get out of it? What products and emergent capabilities will I be able to get, and how can I monetize them? That’s how you must look at it to get it done in a time-efficient manner.
For example, it’s hard to watch people in an old factory with insufficient capital invest at a time when returns are high. They’re working on a machine that’s 30 years old, and it’s great heroism to get the product through the machine because it’s poorly designed and not capable of doing the product you currently build. Typically, you don’t automate a 30-year-old machine. Instead, you get a modern machine that’s capable of building the products that you’re booking (or want to book) in your factory. The process must also be stable to be automated. It’s that simple. That’s the first step to overcome, especially for older shops where they rely on the operators to manipulate things to get the product through. Is the process stable and capable for the products that you want to build under automation? If the answer is no, then you must upgrade the process first.
Barry Matties: You must remove all the operator band-aids before you can automate it. Otherwise, even if you automate the process, it isn’t going to work.
Stepinski: That’s right. Honestly, in a lot of the older shops, this is predominantly the case. At the same time, you hear “there’s not enough space for the automation,” which stems from never having had an automation strategy when whoever started the business so many years ago. When you look at these two things—the band-aids and no space—(plus the process is not stable), usually the best thing to do is get a new piece of equipment. But how much of this equipment in your factory portfolio needs to be replaced? If it’s a few percent, go do it. I’m sure you can find the financing/ROI. If a lot needs to be replaced, that’s a different story. You really have to think about what you’re doing. It might even be time to sell because valuation multiples are high now and you may find someone gullible enough to buy.
But if you think you have a way forward—maybe starting to build a certain type of board—and you can estimate your return on that investment, then you can finance a bigger project. Today’s machines are typically smaller than the ones designed for the production days of the 1990s and earlier in the United States, so you need less space.
When you look at investing in mechanization, it’s really about the process plus the automation. You don’t just put loaders and unloaders on some machine that you deemed capable, or some machine that you upgraded. How much more sophisticated do you want to get with new products? What kind of product mix do you have? How many panel sizes do you have? In the North American market, we have huge numbers of panel sizes. In overseas locations, you don’t see that. In places that are more highly automated, there are fewer panel sizes.
The material cost is typically a lot less than the processing cost, and panel size optimization is a big trade space. You can often reduce the number of panel sizes, which leads to supply chain economies and drop-charge reduction while not increasing TCOQ. It increases the mechanization cost to have excessive panel sizes because you put additional axes on the loader zone and make conveyor width optimization to improve quality via perimeter contact untenable. Loaders can have adjustable panel sizes that adjust on demand—or you manually do it, which then offsets the purpose of the automation.
To read this entire article, which appeared in the September 2022 issue of PCB007 Magazine, click here.
Suggested Items
Smarter Machines Use AOI to Transform PCB Inspections
06/30/2025 | Marcy LaRont, PCB007 MagazineAs automated optical inspection (AOI) evolves from traditional end-of-process inspections to proactive, in-line solutions, the integration of AI and machine learning is revolutionizing defect reduction and enhancing yields, marking a pivotal shift in how quality is managed in manufacturing.
Magnalytix and Foresite to Host Technical Webinar on SIR Testing and Functional Reliability
06/26/2025 | MAGNALYTIXMagnalytix, in collaboration with Foresite Inc., is pleased to announce an upcoming one-hour Webinar Workshop titled “Comparing SIR IPC B-52 to Umpire 41 Functional & SIR Test Method.” This session will be held on July 24, 2025, and is open to professionals in electronics manufacturing, reliability engineering, and process development seeking insights into new testing standards for climatic reliability.
The Death of the Microsection
06/26/2025 | Bob Neves, Reliability Assessment Solutions, Inc.I got my start out of college grinding and polishing PCB microsections. My thumbs are a bit arthritic today because of the experience (microsection grinders know what I mean). Back then, via structures were rather large, and getting to the center in six steps of grinding and polishing was easy compared to what my team has been doing recently at the lab.
Specially Developed for Laser Plastic Welding from LPKF
06/25/2025 | LPKFLPKF introduces TherMoPro, a thermographic analysis system specifically developed for laser plastic welding that transforms thermal data into concrete actionable insights. Through automated capture, evaluation, and interpretation of surface temperature patterns immediately after welding, the system provides unprecedented process transparency that correlates with product joining quality and long-term product stability.
Knocking Down the Bone Pile: Tin Whisker Mitigation in Aerospace Applications, Part 3
06/25/2025 | Nash Bell -- Column: Knocking Down the Bone PileTin whiskers are slender, hair-like metallic growths that can develop on the surface of tin-plated electronic components. Typically measuring a few micrometers in diameter and growing several millimeters in length, they form through an electrochemical process influenced by environmental factors such as temperature variations, mechanical or compressive stress, and the aging of solder alloys.