-
- News
- Books
Featured Books
- pcb007 Magazine
Latest Issues
Current IssueInventing the Future with SEL
Two years after launching its state-of-the-art PCB facility, SEL shares lessons in vision, execution, and innovation, plus insights from industry icons and technology leaders shaping the future of PCB fabrication.
Sales: From Pitch to PO
From the first cold call to finally receiving that first purchase order, the July PCB007 Magazine breaks down some critical parts of the sales stack. To up your sales game, read on!
The Hole Truth: Via Integrity in an HDI World
From the drilled hole to registration across multiple sequential lamination cycles, to the quality of your copper plating, via reliability in an HDI world is becoming an ever-greater challenge. This month we look at “The Hole Truth,” from creating the “perfect” via to how you can assure via quality and reliability, the first time, every time.
- Articles
- Columns
- Links
- Media kit
||| MENU - pcb007 Magazine
Estimated reading time: 4 minutes
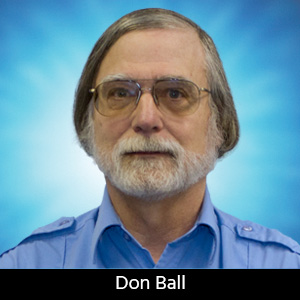
The Chemical Connection: How to Automate Your Wet Processes
Considering automating your PCB fabrication line? If you are, then you may have concerns about what it takes to implement new automation technology. The good news is that setting up your processing lines for automation is simpler than you may think. Whether you are obtaining new equipment, or you want to automate a machine that you’ve been working with for years, automating it can be as simple as tightening a few bolts and wiring a couple connections.
Automating your process lines is now easier than ever thanks to low-cost, user-configurable robot arms. Since most of the processes from the beginning to the end of PCB manufacturing are already automated (at least in wet processing), the only areas left open for automation are the loading and unloading sections. In most cases, people are employed to stand at the ends of the machines loading and unloading material throughout production. As you can imagine, this is not very cost effective because often these people could be performing more important, specialized tasks. By using low-cost, user-configurable robots at the loading and unloading ends of a process (loader bots), you open opportunities for your PCB production to improve. First and foremost, you will reduce the cost per panel thus increasing your profit margins (Table 1 and Figure 1).
On top of the cost decrease, you can shift your employees’ focus to maintaining the equipment, thus improving machine longevity and efficiency. If this is the direction you wish to take your PCB fabrication line, here are a few considerations you will need to get started.
How Many Loaders Are Necessary?
Before you consider automating your process with a loader bot, you will first want to think about the minimum number of loader bots you’ll need to successfully automate your process. This number will depend on your answer to the following questions:
- How many panels do you need to produce per day?
- What is your conveyor speed?
- How large are your panels?
- How many processing lanes are you running (number of panels parallel on the same conveyor)?
- Are there slipsheets that need to be taken off before loading or placed in between panels when coming off the conveyor?
In most cases, you will just need two loader bots to automate your wet process: one for loading and one for unloading. Although this is the case for most, there are bound to be some exceptions. If you have small panels, high conveyor speeds, multiple processing lanes, or slipsheets involved in your production, you may need more than two loader bots to maintain the maximum production capacity without any errors. This is because to maintain a production level of full efficiency, every movement of the loader bot needs to be purposeful. The loader bot can only move so fast and with each additional task you require the bot to take, the less time it will have to make sure your conveyor space is fully utilized. Even in cases where there are high conveyor speeds and slipsheets, the standard two-loader bots can still get the job done. However, if you find yourself with multiples of these special cases, you should tell your bot provider/representative about the conditions you are trying to obtain. From there, they can run tests and work with you to determine the minimum number of bots to run your desired process. Once you know how many loader bots you will need, then you will know how many resources you will need to spare for them.
Base Necessities for Loader Bots
One of the great things about the loader bots is that they do not require many resources to function. The main resources they need are power, air, and space.
Some loader bots can simply run off a 9V wall outlet. Although they can run off simple outlets, it is wise to plan and provide a source of power that would be close to where the bot will be functioning. For safety reasons, it is best to arrange permanent wiring and avoid extension cords.
Air supply should be a relatively simple resource to provide for the loader bot as well. Since wet processing equipment typically uses compressed air somewhere on the machine, you can feed a line from that source to a regulator valve that would feed into your bot’s head-frame for suction.
Space is another resource that needs to be allocated to the loader bots. Thankfully, the loader bots themselves can be easily mounted on the side of a machine. Since they will be on the side of a machine, they will likely take up space that will already be available and therefore will not need much planning. However, additional space is required to provide trays to hold the panels. This would mean each robot would need a tray within reach. Figure 2 shows an example.
These trays will need to be slightly larger than the panels you are processing, but if you are also working with slipsheets you may need trays for those too. If you plan to reuse the slipsheets or to restack the process boards with slipsheets separating them, you will need extra trays to hold the sheets.
Once you have all these resources prepared, all that’s left to do is to install the bot and create the routine that the bot will run through.
Conclusion
Setting up your wet process for automation is quite simple and the most it requires is just a little planning. Once you have all the necessities planned out, it is just plug-and-play from there on. You will get time to work with the program and develop routines for the bot to go through. After that, you have an automated wet processing line that can run for hours without human intervention.
This column originally appeared in the September 2022 issue of PCB007 Magazine.
More Columns from The Chemical Connection
The Chemical Connection: Sales Organization from a Capital Equipment PerspectiveThe Chemical Connection: Through-glass Vias in Glass Substrates
The Chemical Connection: Reducing Defects in Circuit Board Production
The Chemical Connection: Common Misconceptions in Wet Processing
The Chemical Connection: Surface Finishes for PCBs
The Chemical Connection: Earthquakes, Astronauts, and Aquatics—A Lighter Look at the Past
The Chemical Connection: Better Fabs Attract a Better Workforce
The Chemical Connection: Can Changing Spray Nozzles Improve My Etch Quality?