-
- News
- Books
Featured Books
- pcb007 Magazine
Latest Issues
Current IssueInventing the Future with SEL
Two years after launching its state-of-the-art PCB facility, SEL shares lessons in vision, execution, and innovation, plus insights from industry icons and technology leaders shaping the future of PCB fabrication.
Sales: From Pitch to PO
From the first cold call to finally receiving that first purchase order, the July PCB007 Magazine breaks down some critical parts of the sales stack. To up your sales game, read on!
The Hole Truth: Via Integrity in an HDI World
From the drilled hole to registration across multiple sequential lamination cycles, to the quality of your copper plating, via reliability in an HDI world is becoming an ever-greater challenge. This month we look at “The Hole Truth,” from creating the “perfect” via to how you can assure via quality and reliability, the first time, every time.
- Articles
- Columns
- Links
- Media kit
||| MENU - pcb007 Magazine
Estimated reading time: 2 minutes
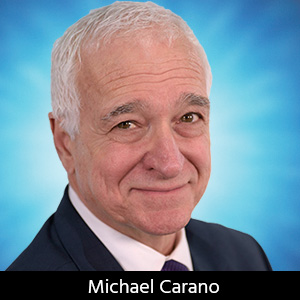
Contact Columnist Form
Trouble in Your Tank: Electrodeposition of Copper, Part 3—Plating Distribution and Throwing Power
Introduction
Success in the plating room rests largely on the understanding and the application of those critical principles that govern the process of electrodeposition (often referred to as electroplating). This month, I look at the fundamentals of plating distribution and throwing power, and what that means for the circuit board fabricator.
Current Distribution
There are many factors that influence the flow of current in the electroplating cell and, ultimately, the distribution of the metal across the part, along with the concept of throwing power.
These are:
- Overall composition of the electrolyte
- Polarization influence
- Conductivity of the electrolyte
- Cathode efficiency/current density curves
- Geometry of plating system/plating cell design
- Other factors such as use of organic addition agents
- Substrate composition and structure
- Surface preparation and pre-treatment
When studying electrodeposition, one needs to understand that current distribution has two components:
- Primary current distribution
- Secondary current distribution
One can easily apply these two entities to develop a model for the electroplating process. Primary current distribution is determined by voltage drop inside the cell and electrode shape and position. Basically, this is governed by the electrical field within the cell itself.
Fortunately for the electrodeposition process, other factors come into play. If only primary current distribution were present, relatively uniform plating distribution and good throwing power in high aspect ratio through-holes would be challenging if not nearly unattainable. Now, secondary current distribution is influenced by ohmic resistance in the plating cell along with the kinetics of the electrodes.
More specifically, organic addition agents and other additives act as high current density inhibitors—suppressing plating in the high current density areas of the board. This allows for improved micro throwing power in the lower current density areas, i.e., areas of higher ohmic resistance. This can be better explained below in Figure 1.
Again, if the cell resistance is low, then primary current distribution would dominate. In other words, portions of the part or PC board closest to the anode would receive the most current. Thus there would be overall poor distribution of plating thickness across the part and in the through-holes (Figure 2).
Fortunately for the process engineer, other factors come into play in the form of secondary current distribution. The difference between primary and secondary current distribution lies in understanding electrode kinetics in addition to solution resistance. Secondary current distribution allows for a more uniform current distribution across the cathode surface. This is primarily because of electrode kinetics by means of an activation overpotential. This overpotential tends to make the current distribution more uniform.
Compared to the primary current distribution, the secondary current distribution is smoother, with a smaller difference between the minimum and maximum values. When the activation overpotential is included, a high local current density would introduce a high local activation overpotential at the electrode surface, which causes the current to naturally take a different path—essentially finding its way to the lower current density areas. Therefore, one can improve through-hole plating distribution.
The engineer can improve plating distribution and throwing power by manipulating the following:
- Reduce cathode current density
- Increase conductivity of the electrolyte—higher acid concentration
- Ensure uniform solution agitation across the panels, but not excessive
- Monitor contamination and organic build-up in the plating electrolyte
- Increase anode-to-cathode distance—10 inches improve throwing power vs. 6 to 8 inches
Remember this is a process and needs to be controlled.
This column originally appeared in the September 2022 issue of PCB007 Magazine.
More Columns from Trouble in Your Tank
Trouble in Your Tank: Minimizing Small-via Defects for High-reliability PCBsTrouble in Your Tank: Metallizing Flexible Circuit Materials—Mitigating Deposit Stress
Trouble in Your Tank: Can You Drill the Perfect Hole?
Trouble in Your Tank: Yield Improvement and Reliability
Trouble in Your Tank: Causes of Plating Voids, Pre-electroless Copper
Trouble in Your Tank: Organic Addition Agents in Electrolytic Copper Plating
Trouble in Your Tank: Interconnect Defect—The Three Degrees of Separation
Trouble in Your Tank: Things You Can Do for Better Wet Process Control