-
-
News
News Highlights
- Books
Featured Books
- pcb007 Magazine
Latest Issues
Current IssueSales: From Pitch to PO
From the first cold call to finally receiving that first purchase order, the July PCB007 Magazine breaks down some critical parts of the sales stack. To up your sales game, read on!
The Hole Truth: Via Integrity in an HDI World
From the drilled hole to registration across multiple sequential lamination cycles, to the quality of your copper plating, via reliability in an HDI world is becoming an ever-greater challenge. This month we look at “The Hole Truth,” from creating the “perfect” via to how you can assure via quality and reliability, the first time, every time.
In Pursuit of Perfection: Defect Reduction
For bare PCB board fabrication, defect reduction is a critical aspect of a company's bottom line profitability. In this issue, we examine how imaging, etching, and plating processes can provide information and insight into reducing defects and increasing yields.
- Articles
- Columns
- Links
- Media kit
||| MENU - pcb007 Magazine
Book Excerpt: The Electronics Industry’s Guide to… The Evolving PCB NPI Process, Chapter 1
September 28, 2022 | I-Connect007 Editorial TeamEstimated reading time: 2 minutes
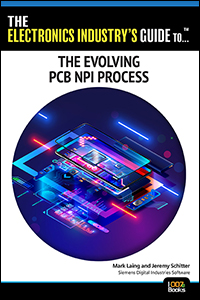
Chapter 1
How the NPI Process Has Changed and Where We're Going
When forging into unknown territory or exploring new ground, it can help to look at where we’ve been so we can orient ourselves.
Just a few decades ago, electronics manufacturing companies were producing high volumes of few products. The efficiency of electronics manufacturing lines is measured by overall equipment effectiveness (OEE) and total effective equipment performance (TEEP). Back then, this meant optimizing the time it took to build a single board. If the time it took to build one board could be reduced by a few seconds, the savings would be multiplied by the number of boards being built. This could be in the hundreds of thousands or millions of boards, with no changes in the line configuration. If it took a day to change over from one product to another, it didn’t matter because the TEEP/OEE was driven by the time it took to build a board.
For example, consider that it takes 35 seconds to place components on a single board, and I need to make 250 boards. My handling time (the time it takes to load a board into the machine and get it out after) is 10 seconds, then the total time to build the 250 boards will be (35 + 10) • 250 = 11,250 seconds. This equates to about 188 minutes, or approximately three hours. If it takes four hours to changeover—namely reconfigure the line before starting a different PCB—to a new product, my OEE will be less than 50%, considering no other external factors. As the batch size goes down, the changeover time dominates the OEE figure.
In today’s high-mix, low-volume production environments, performance is further enhanced with line efficiency. Line efficiency is the ratio of the number of hours during which a high-volume, pick-and-place machine places parts on the PCB, divided by the number of hours during which the SMT assembly lines are staffed (placement time/staffed time x 100). It is a solid number, simple to obtain, and has great value as a key performance indicator.
With higher product mixes, the number of NPIs being processed increases. Changeovers on the shop-floor line can happen daily or many times a day. This also means the time it takes to process the source design data has increased. This data-processing time is becoming a more important consideration compared to when NPI processing was not a daily task in the lower mix environment. As product mix has gone up, there has been a move from mixed vendor lines focused on ultimate through-put to single vendor lines focused on flexibility and shorter changeovers. There may be more than one pick-and-place vendor brand in the factory, but each line commonly has only one brand now.
Download your free copy today! You can also view other titles in our full library.
We hope you enjoy The Electronics Industry’s Guide to… The Evolving PCB NPI Process.
Testimonial
"The I-Connect007 team is outstanding—kind, responsive, and a true marketing partner. Their design team created fresh, eye-catching ads, and their editorial support polished our content to let our brand shine. Thank you all! "
Sweeney Ng - CEE PCBSuggested Items
Statement from the Global Electronics Association on the July 2025 Tariff on Copper Foil and Electronics-Grade Copper Inputs
07/31/2025 | Global Electronics AssociationWe are disappointed by today’s decision to impose a 50% tariff on imported copper foil and other essential materials critical to electronics manufacturing in the United States.
Mouser Electronics Receives Top Global Distributor, Growth Awards from HARTING
08/01/2025 | Mouser ElectronicsMouser Electronics, Inc., the authorized global distributor with the newest electronic components and industrial automation products, has been honored with HARTING's prestigious Global High Service Distributor of the Year Award. Mouser also received the Distinguished Award for New Product Sales Growth. The awards were presented at HARTING's recent 2025 Distribution Summit in Louisville, Kentucky.
FlashPCB Enhances SMT Production Line with Heller 1809 Reflow Oven and KIC ProBot
07/31/2025 | FlashPCBFlashPCB, a leading provider of quick-turn PCB assembly, has expanded its surface mount production capabilities with the installation of a Heller 1809 MKII reflow oven paired with the KIC ProBot automatic profiling system. This addition supports FlashPCB’s goal of achieving faster throughput, higher quality assurance, and consistent process control across a wide range of PCB builds.
DigiKey Expands Inventory with Over 32,000 Stocking NPIs in Q2 2025
07/31/2025 | Digi-KeyDigiKey, the leading global electronic components and automation products distributor, extensively expanded its in-stock products available for same-day shipment by adding more than 32,000 innovative new product introductions (NPIs) in the second quarter of 2025.
Insulectro Facilitates Fabricator Access to EMC Mass Lam Capabilities
07/30/2025 | InsulectroInsulectro, the largest distributor of materials used in the manufacturing of printed circuit boards and printed electronics, announces a new service - a system to help our customers to access EMC's well established mass lam offerings. Long a leader in mass lam manufacturing, EMC is the exclusive supplier in Insulectro's laminate and pre preg portfolio.