Michael Carano: A Focus on Process Control, Part 2
September 28, 2022 | I-Connect007 Editorial TeamEstimated reading time: 10 minutes
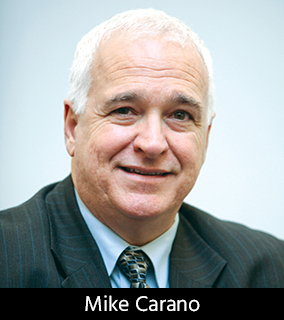
In this second half of our conversation, Michael Carano discusses some of the metrics that fabricators need to consider before investing in new processes, especially process control technologies, and some of the challenges board shops face updating brownfield sites.
To read Part 1, click here.
Barry Matties: So, part of the investment that fabricators need to make has to come from thinking about process—process control engineers, process engineers, etc. But when you start talking about shops with 50 employees, you can walk into a facility and tune it up for $50,000. Do they not have the knowledge? Because $50,000 isn’t resource limitation.
Mike Carano: Right. It’s not that they don’t have the knowledge. The problem is the company has one engineer that does everything. That’s it. Everyone else is in administration. You need a place with more engineering talent, ones who can understand the process and what happens in the process. But you have a young person who comes in and has to work on imaging one day, solder mask the next day, and then plating the next because a “fire” breaks out. It all cascades down. Something is out of control. What do I fix right now? With more automation on the controls, the instrumentation will give you online analysis.
Don’t just depend on your supply base to do all this for you; you need it onsite and with much tighter controls. If you’re building eight- or four-layer boards, maybe you don’t need to do all that, but you need process control no matter what. Only a few processes are truly automated in terms of control. Maybe the alternate etcher has the feed and bleed. But even with that, you want to make sure the equipment is maintained so it gives you an accurate reading and keeps the chemistry within a tight operating window. The other one is much more extensive, and that’s where engineering comes in. There’s a lot to do with imaging. All the processes must come together. It’s not just plating, the materials, or the materials handling. It’s the etching, imaging, surface preparation, the workflow, and how people manage it. In this industry, there’s so much going on at one time and it’s all interrelated.
The Special Brownfield Challenges
Nolan Johnson: In the Thought Leaders paper, mechanization and automation is strongly implied. Such as, if you were to go through that $10 million upgrade, you’ll have a lot more mechanization and automation available to you on the manufacturing floor. Can you do this in a brownfield site?
Carano: That’s a good question. You walk in, you say, “Here’s what I would do right here.” You’ve got an etcher in this corner, and you’ve got imaging over here and you carry the panels from imaging to etching or developing. Early in my career, I was working with direct metallization horizontal processing. You start with bare copper, go through horizontal desmear and then drilling. So, it’s horizontal desmear, down through the direct metallization line. You shorten the process because direct metallization really squeezed a lot of time and increased productivity as well as quality. From there, it goes into a slit in the wall, into a cut sheet laminator, the photoresist gets laminated, and the panel imaged. Then it goes into another room and gets developed, etched, and stripped, all automated, all horizontal.
You can do a lot with that. You don’t have to say, “I must make this workable. I must make 10,000 panels a day.” No, you don’t. You can size the equipment properly, you replace the equipment with the latest in etching technology. It’s probably a shorter footprint, and you just do it horizontally. In Asia, almost every- thing is horizontal processing in some way, shape, or form, except maybe for the electroplating. But I’ve seen people do electroplating horizontally, in a continuous fashion, and yet they have a lot of engineers. Those engineers are freed up to solve any technical issues because they’re constantly watching that.
There’s a grocery store by my house that has automated most of the cashiers, but they didn’t eliminate the jobs. Instead, they put the people out in the aisles to help you find what you’re looking for. They guide you to find what you need and if they can’t find it, they go to the stockroom and get it for you.
That’s where you get that personal touch. If you have engineers on the floor, instead of worrying about running the horizontal line, they’re solving problems and keeping everything in tight control. Audit those processes on a regular basis. Is it getting out of control? Are the temperatures rising or is it out of control? It’s all about variation. Some people, like Happy Holden, are firm believers in process audits and how to control things. As I’ve talked to Happy, I’ve learned it could be done in a reasonable fashion with less money. Most people think it’s going to cost millions and millions. It’s not.
Johnson: If it’s a brownfield site that has a very difficult workflow, they’ve got a problem. They have to start at step zero and develop a workflow before they can take advantage of the automation.
Carano: That’s exactly right.
Matties: It sounds like one of the first audits a shop should do is determine what the process engineer is working on. What’s a typical day? How do we free them up from the things that are, as you’re saying, not taking care of the customer, if you will?
Carano: Exactly. Remember that you have the line workers that are feeding the etchers and moving the panels on the floor. You want to invest in their training so when there’s an issue, they will notice it, stop the line, and call the engineers. This is “customer facing,” problem solving, and making improvements.
From an engineer, I always look at their total chemical costs and they tell me, “Oh, my costs might be too high.” Well, how do you know? How are you analyzing it? How are you con- trolling it? If they’re into a situation when the bath gets contaminated, we just send it to waste treatment. Well, that adds cost. At that point, it’s contaminated and why? Maybe that’s the first thing you do. That’s the engineer’s job. I’ve worked with some great engineers over the years who really understand how to con- trol things and optimize processes. They spend their time doing that and educating folks on the line. I’ve seen these engineers improve how the chemistry is managed and added, how it’s controlled. Not only does it improve yields, but it reduces waste and cost.
People always look at cost per liter, cost per gallon. It’s not the price, it’s the cost of owner- ship. What does it cost you to make this circuit board? That includes a lot of things, including the quality of the handling, the yields. You’re looking for an efficient use of the processes and that can be done with people paying good attention.
I’ve had people tell me their electroless copper is $2 a square foot. I look at it and I can see why. They’re wasting chemistry. The vats are not shutting down properly at night, so the chemistry is plating out. You could be doing some simple things that don’t cost you anything: Turn down the temperature and turn on the air pump to keep the baths stable overnight or clean out the tank on the weekend to prevent any doubt. That’s waste, so don’t get mad because your costs are high. When you get it back to running properly, then the cost per square foot goes down by 50% or more and the reliability is also there. Some very simple things can be done, but it’s about education, training, certification, and getting everyone on board— including the ownership and management.
Matties: Right. If management doesn’t buy in, it’s not going to happen.
Carano: No, it won’t and that’s the same story. If an OEM doesn’t come to them with the design and says, “I need you to build this. I want you to build the 20-micron lines and spaces,” they won’t make the investment into that next technology. It’s a shame because there are some great opportunities to do this process-, chemistry-, and material-wise. It could be done.
Matties: In a brownfield site, what’s the priority in terms of transforming the facility?
Carano: I would start with a top-down audit of all processes, including imaging materials, handling storage, and humidity chambers. How are you controlling the plating processes? Where are the matching processes. From there you make the recommendations. You need better controls and better lab equipment. You can’t just have burettes and titrations; you need some other methods of controlling your processes.
To build high-end items, you must figure out reliability. How reliable are your processes? That’s important. There are opportunities to do D-coupon testing, CITC, as well as IST. You can use outside sources to qualify that. I would look at the latest in registration and imaging. How could I automate more of the etching? Can I connect the etching and imaging processes together? At the very least can I improve the etcher? Can I get a better etcher that’s not 20 years old? Can I enhance my electroplating knowledge and tank set-up with new via fill technology?
There is good electrolytic copper technology today and it’s getting better. All the suppliers are pushing via fill technology with new equipment and chemistries. To upgrade, you must take a leap of faith.
The mil/aero space is clamoring for some help by the North American fabricator, otherwise they will go offshore. They will argue to the DoD that if they can’t get it built here, then what? You’re going to shut down an entire fighter program? That would be devastating for this industry. To me, it would be the death of it.
Johnson: In general, does the ownership in the U.S. fabrication industry have the motivation to do this?
Carano: I’ve talked to several, particularly some who bought a new company or addi- tional companies over the last couple of years, and they’re committed, smart, and motivated. Their work is full, upgrading where needed, looking to hire, moving up to the level they need to, investing in some equipment, maybe plating equipment and flying probe technology.
The next step is with ultra-high density. It will be much finer lines and spaces, which translates into not just various layers, like signal layers, but into the IC substrates. That requires another level of investment. The current lasers are great, they’re at 1 mil, but you will get below that, down to 0.5 or 0.8 mil. That will require an investment, which will typically cost more. Then you maybe add a new laser CO2 YAG drill. That’s another cost.
I’m sure the military aerospace group will get some help. There’s money to be spread around and it’s not going to cost a billion dol- lars per fabricator. With $10 or $20 million, it can be done. Then, get people excited; instead of working in a foundry, which is not rad, come to our circuit board business, our electronics business, our interconnect business. We can give it something that says, “This is really cool.”
Johnson: With an automated factory, now you’re starting to talk about more of an engineering function than just an operator function.
Carano: Exactly. Folks can come in from a technical school or a two-year program and say, “Hey, this is fun. I want to do more. I want to learn more.” They might want to take night classes or other training so they can do more on the job. It’s life-changing, knowing the products they make are helping somebody. If it’s for the medical industry, for example, making stents more reliable for the human body, making heart monitors more reliable. While it’s not the end product, those stents go in someone’s body and they need to function. They can’t corrode or cause problems. That can make your work more enjoyable.
Matties: Thank you so much. We greatly appreciate your time.
Carano: Thank you.
This conversation originally appeared in the September 2022 issue of PCB007 Magazine.
Suggested Items
BEST Inc. Introduces StikNPeel Rework Stencil for Fast, Simple and Reliable Solder Paste Printing
06/02/2025 | BEST Inc.BEST Inc., a leader in electronic component rework services, training, and products is pleased to introduce StikNPeel™ rework stencils. This innovative product is designed for printing solder paste for placement of gull wing devices such as quad flat packs (QFPs) or bottom terminated components.
See TopLine’s Next Gen Braided Solder Column Technology at SPACE TECH EXPO 2025
05/28/2025 | TopLineAerospace and Defense applications in demanding environments have a solution now in TopLine’s Braided Solder Columns, which can withstand the rigors of deep space cold and cryogenic environments.
INEMI Interim Report: Interconnection Modeling and Simulation Results for Low-Temp Materials in First-Level Interconnect
05/30/2025 | iNEMIOne of the greatest challenges of integrating different types of silicon, memory, and other extended processing units (XPUs) in a single package is in attaching these various types of chips in a reliable way.
E-tronix Announces Upcoming Webinar with ELMOTEC: Optimizing Soldering Quality and Efficiency with Robotic Automation
05/30/2025 | E-tronixE-tronix, a Stromberg Company, is excited to host an informative webinar presented by Raphael Luchs, CEO of ELMOTEC, titled "Optimize Soldering Quality and Efficiency with Robotic Automation," taking place on Wednesday, June 4, 2025 at 12:00 PM CDT.
CE3S Launches EcoClaim Solutions to Simplify Recycling and Promote Sustainable Manufacturing
05/29/2025 | CE3SCumberland Electronics Strategic Supply Solutions (CE3S), your strategic sourcing, professional solutions and distribution partner, is proud to announce the official launch of EcoClaim™ Solutions, a comprehensive recycling program designed to make responsible disposal of materials easier, more efficient, and more accessible for manufacturers.