-
- News
- Books
Featured Books
- pcb007 Magazine
Latest Issues
Current IssueVoices of the Industry
We take the pulse of the PCB industry by sharing insights from leading fabricators and suppliers in this month's issue. We've gathered their thoughts on the new U.S. administration, spending, the war in Ukraine, and their most pressing needs. It’s an eye-opening and enlightening look behind the curtain.
The Essential Guide to Surface Finishes
We go back to basics this month with a recount of a little history, and look forward to addressing the many challenges that high density, high frequency, adhesion, SI, and corrosion concerns for harsh environments bring to the fore. We compare and contrast surface finishes by type and application, take a hard look at the many iterations of gold plating, and address palladium as a surface finish.
It's Show Time!
In this month’s issue of PCB007 Magazine we reimagine the possibilities featuring stories all about IPC APEX EXPO 2025—covering what to look forward to, and what you don’t want to miss.
- Articles
- Columns
Search Console
- Links
- Media kit
||| MENU - pcb007 Magazine
Korf and Strubbe: Material Witnesses
October 3, 2022 | I-Connect007 Editorial TeamEstimated reading time: 3 minutes
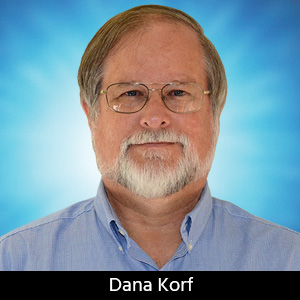
Recently, columnist Dana Korf has been working with Taiwan Union Technology Corporation (TUC), one of the largest providers of copper-clad laminate and mass lamination services in the world. We spoke with Dana about the trends he sees in materials at TUC and around the globe, why copper is still king, as well as some potential non-traditional materials that may see growth soon. Dana invited John Strubbe, TUC VP of technology, to join in the conversation.
Nolan Johnson: Dana, what’s new in the materials world? What are you seeing?
Dana Korf: If you look at straight FR-4, there’s not much going on. There are more high-voltage requirements in the automotive, so there’s a little bit of tweaking of FR-4 to handle voltages around 1,500 or 2,000 volts. Of course, they want long-term reliability, but that’s a relatively minor technical requirement to obtain. With HDI, it’s just a matter of working with thinner glass fabric with the traditional HDI resins, because layers are getting thinner and the number of required lamination cycles increases every year, but that’s more of an adjustment of material properties.
Chip packaging is becoming a constraint. Many companies, like TUC, are now offering chip level packaging materials because there’s just more demand for it than the market can handle. That has a fairly long approval process, just like automotive.
John Strubbe: Most of my work is in low-loss materials for digital. Trying to, as I often say, “get down to free space, no loss,” for the same price as FR-4. There’s a lot of work in copper foil and resins, and a lot of analysis on the glass fabrics. They’re starting to look at quartz again and polymeric materials. They’re trying to get down to really low losses for digital, but the designers are running into the problem that even if you get the losses down to that level, it’s still not good enough. There’s analysis about whether the loss-budget gains you get vs. the cost will be worth it or even possible. That’s what most of the large material folks are working on now. In the RF space, they’re pretty much just working on better controlled RF materials to get the cost down.
Korf: When I was working in China, I was seeing digital designers looking at RF materials to get their losses down. The RF folks were looking at digital performance materials to get the cost down, and that’s still going on. I see that most of the material development work is primarily being driven to reduce the loss, Df, primarily in the digital space. There are umpteen varieties of FR-4, so they seem to be covering the market well; the high voltage for automotive is stressing the specs a little bit, but not too much.
What’s interesting on the material side is we’re starting to look at non-glass alternatives. For example, we’re looking at quartz again, like we did in the 1980s. The problem with quartz glass is that when you hit it with a laser, it melts and balls up. It doesn’t evaporate away. That was a challenge many years ago when we tried it.
Johnson: That makes it tough for laser applications.
Korf: It does make it interesting.
Johnson: What are some of the nontraditional materials being evaluated?
Strubbe: We can talk about the coppers getting down to zero roughness, what’s going on there, and limitations. Does it stick to the resin at the end of the day? Like a lot of technologies, they tend to cycle every 20 or 30 years, and improve with every cycle. Fundamentally, it’s stuff that’s been looked at before.
To read this entire conversation, which appeared in the September 2022 issue of PCB007 Magazine, click here.
Suggested Items
Elephantech: For a Greener Tomorrow
04/16/2025 | Marcy LaRont, PCB007 MagazineNobuhiko Okamoto is the global sales and marketing manager for Elephantech Inc., a Japanese startup with a vision to make electronics more sustainable. The company is developing a metal inkjet technology that can print directly on the substrate and then give it a copper thickness by plating. In this interview, he discusses this novel technology's environmental advantages, as well as its potential benefits for the PCB manufacturing and semiconductor packaging segments.
Trouble in Your Tank: Organic Addition Agents in Electrolytic Copper Plating
04/15/2025 | Michael Carano -- Column: Trouble in Your TankThere are numerous factors at play in the science of electroplating or, as most often called, electrolytic plating. One critical element is the use of organic addition agents and their role in copper plating. The function and use of these chemical compounds will be explored in more detail.
IDTechEx Highlights Recyclable Materials for PCBs
04/10/2025 | IDTechExConventional printed circuit board (PCB) manufacturing is wasteful, harmful to the environment and energy intensive. This can be mitigated by the implementation of new recyclable materials and technologies, which have the potential to revolutionize electronics manufacturing.
Connect the Dots: Stop Killing Your Yield—The Hidden Cost of Design Oversights
04/03/2025 | Matt Stevenson -- Column: Connect the DotsI’ve been in this industry long enough to recognize red flags in PCB designs. When designers send over PCBs that look great on the computer screen but have hidden flaws, it can lead to manufacturing problems. I have seen this happen too often: manufacturing delays, yield losses, and designers asking, “Why didn’t anyone tell me sooner?” Here’s the thing: Minor design improvements can greatly impact manufacturing yield, and design oversights can lead to expensive bottlenecks. Here’s how to find the hidden flaws in a design and avoid disaster.
Real Time with... IPC APEX EXPO 2025: Tariffs and Supply Chains in U.S. Electronics Manufacturing
04/01/2025 | Real Time with...IPC APEX EXPOChris Mitchell, VP of Global Government Relations for IPC, discusses IPC's concerns about tariffs on copper and their impact on U.S. electronics manufacturing. He emphasizes the complexity of supply chains and the need for policymakers to understand their effects.