-
- News
- Books
Featured Books
- pcb007 Magazine
Latest Issues
Current IssueSales: From Pitch to PO
From the first cold call to finally receiving that first purchase order, the July PCB007 Magazine breaks down some critical parts of the sales stack. To up your sales game, read on!
The Hole Truth: Via Integrity in an HDI World
From the drilled hole to registration across multiple sequential lamination cycles, to the quality of your copper plating, via reliability in an HDI world is becoming an ever-greater challenge. This month we look at “The Hole Truth,” from creating the “perfect” via to how you can assure via quality and reliability, the first time, every time.
In Pursuit of Perfection: Defect Reduction
For bare PCB board fabrication, defect reduction is a critical aspect of a company's bottom line profitability. In this issue, we examine how imaging, etching, and plating processes can provide information and insight into reducing defects and increasing yields.
- Articles
- Columns
- Links
- Media kit
||| MENU - pcb007 Magazine
Estimated reading time: 5 minutes
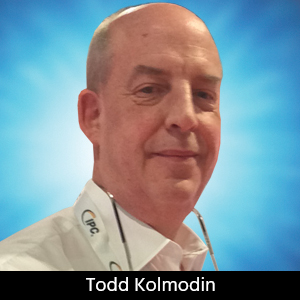
Testing Todd: Induction Junction, What’s Your Function?
Historically electrical test has processed product with passive inductor features without really knowing what they were, other than causing continuity threshold violations. This is usually due to the long traces that exhibit higher resistance than the 10- or 20-ohms threshold. Typically, these have been delaying traces or heater traces. Usually, a waiver of allowance is made for these high resistive traces and business carries on as usual.
However, there can be a lot more going on than just a long or coiled trace. Figure 1 shows a typical heater scenario. As you can see in the illustration, each is a single net with a long trace. The characteristic of this design is specific, and the entire trace is necessary. The problem is whether any of the long trace shorts to itself. In a standard continuity test, this defect will go undetected as a short to itself and will not present a change in resistance significant enough to fault. However, the circuit itself now fails against its intended design.
There are two possible solutions to capturing this defect. The 4-wire Kelvin Test may capture the small change in resistance, but with this much copper the accuracy of the test may be compromised to the point that the change would have to be too significant to trigger a fault. The other option is testing the inductance of the network. There is technology available to perform this test on a flying probe. Pre-programmed values can be provided to the machine and when the test encounters this device it will check the value and compare to expected. This test records all values and can provide a report for post-test analysis.
Now, in my above example we discussed a very basic scenario of a heater or timing trace. However, inductors can play a very active role in circuit design. So, strap in and take your Dramamine because the ride now gets a little bumpy.
Inductors or coils usually play a role as transformers or sometimes electromagnetic motors. Using a primary and secondary winding, these devices can step-up or step-down voltages or create an electromagnetic field that can spin an armature in a motor assembly. However, in PCB design they can do some very interesting things. The primary and secondary of a coil are created by making “turns” of a wire around a form or core. The ratio of the number of turns in the primary to the number of turns in the secondary determines the characteristics of performance. We don’t see the use of transformers on a PCB per se, but they perform other functions quite well.
Although coils can be used to boost or augment voltages, they are primarily used to manipulate signals. This is particularly important in RF designs. In high-speed digital or RF circuits, stray RF or parasitic components are extremely detrimental to product performance. Here is where the inductors play a very important role. When you play in the RF arena you deal with VSWR, reactance and attenuation. Remember that I said a coil is a device that has a core and a primary and secondary winding?
Well, an active coil could be created using just the PCB. PCB manufacturing uses dielectrics between layers (hey, a core material) and depending on the design, an inductor can be made. We can run a trace between layers, say 1 to 3, back to layer 1, back to layer 3, and so on until we have the number of “turns” we need. We do the same for the other winding. We have created a primary and secondary winding around a core. An inductor! Todd, you say, that’s all fine and good but what are we doing?
As it sits, we can boost a signal or impedance match a circuit with that. But we don’t stop there. If we add resistance or capacitance to this circuit, we start getting into reactance. Coils act differently when coupled with resistors or capacitors. We start playing in the world of inductive reactance and capacitive reactance. This is where it gets important with RF and microwave applications. Reactivity plays a significant role. Whether the circuit has inductive reactivity or capacitive reactivity depends on the matching. In an RF application, if the inductive reactivity equals the capacitive reactivity the circuit resonates, and full power is presented to the feed point of the transmitting port or antenna (if applicable).
Figure 2 illustrates a Smith Chart where reactivity is plotted. When either inductance or capacitance in the circuit is higher than the other, the reactivity changes and influences the performance. If the circuit is more inductive, current in the circuit will lead the voltage by a phase angle specific to the amount different from resonance. Conversely, if the circuit is more capacitive the voltage will lag the current by a phase angle specific to the difference from resonance.
Figure 2: Smith Chart.
Still with me? What has this all got to do with the PCB? We have a coil on the PCB. Now, if we had capacitance in parallel to the primary winding, we could make some magic. By adding capacitance to the inductor, we can create filters. Specifically, filtering can be done to signals that stop certain frequencies from passing or allow only a specific range of frequencies to pass. These are called “band pass” and “band stop” filters. So, when using a coil (inductor) with a capacitor/resistor, we are doing what is called “tuning the circuit.” This allows the pre-determined signals to process optimally, while stopping or eliminating parasitic signals.
What does this all mean? The inductance in a passive or active inductor within the PCB is critical to final performance. Therefore, the standard electrical test of the coil’s primary and secondary windings cannot be satisfied. A short within the primary or secondary windings may not trigger a fault but will affect the performance of the tuned circuit. Thus, measuring the proper inductance of the coil is critical. Although an inductor circuit may pass the standard opens and shorts test, it does not mean that the circuit is stable.
That is why inductance should be tested whenever buried coils or inductors are manufactured within the PCB with specific end results expected.
This column originally appeared in the October 2022 issue of PCB007 Magazine.
More Columns from Testing Todd
Testing Todd: Why 4-wire Kelvin?Testing Todd: Why TDR?
Testing Todd: Positivity Boosts Employee Morale
Testing Todd: Preparing Employees for the Long Haul
Testing Todd: Where Can We Improve?
Testing Todd: Turning Into the Wind
Testing Todd: Coming Back to Life—Design Recovery
Testing Todd: Decision Time—Invest or Delegate?