Estimated reading time: 4 minutes
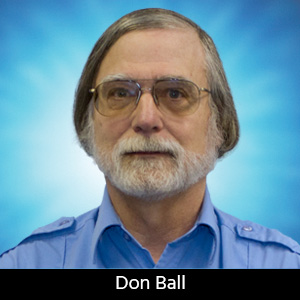
The Chemical Connection: Closing the Innovation Gap
In Nolan Johnson’s September 2022 column, “New Era Manufacturing,” he referred to the carriage whip manufacturing businesses that met their fate by failing to adapt while other carriage businesses with more robust product applications remained standing. He said this relates to our industry in the sense that the needs of our world are evolving, that the wants and needs of PCB fabricators and their customers are bound to change. There will always be a demand for PCBs, since it is the foundation of modern technology, but market challenges are inevitable. PCB fabricators are dealing with increasing material and labor costs, all while major quick-turn-around jobs are declining. The questions we must ask are: Where do we go from here? How can PCB fabricators overcome these challenges and get an edge in the market? How can we best adapt?
First, let’s look at how our industry has adapted. There have been many advancements in automation technology applications since we entered the fourth generation of the Industrial Revolution. We are introducing robotics and advanced data analytics to our PCB fabrication processes. This has certainly been a step in the right direction for us to combat the before-mentioned obstacles. Although automation brings a lot to the table, will it ever be enough? For some fabricators, it may seem sufficient. However, this may be a relatively short-term solution. But we must address the growing issue of where we will find engineers who will innovate and influence PCB manufacturing technology—before it eventually throttles the growth of the industry.
I was also interested in Paige Fiet’s September 2022 column, “Let’s Make Manufacturing ‘Cool’ Again.” She wrote that the new generation of engineers is not as interested in manufacturing anymore, as she made mention of the large shift toward computer science where generally there is a higher status and cozier jobs. Although that field is gaining popularity, don’t write off manufacturing just yet. There is plenty of interest in manufacturing in the electronics industry, just not in the field of PCBs. The semiconductor industry is keeping the newer generation interested in manufacturing jobs. I believe the main influencers are education and awareness.
I attended IPC APEX EXPO for the first time this year and since then I have noticed a recurring theme among those who get involved in PCB manufacturing: Before they started working in the field, most did not have much awareness of our sector. In fact, before I became a process engineer at Chemcut, I was one of them. This was primarily because I was not exposed to it in college. While I was aware that my chemical engineering degree could be applied to the semiconductor industry, I did not associate it with circuit boards. At my university, there were even a handful of professors who specialized in semiconductor research, so it seems that students are more exposed to semiconductors than to PCBs. This appears to heavily influence where these students choose to take their careers.
If our industry wants to adapt for the better, it must start from the ground-up—starting where students get exposure to our industry. More exposure means more scientific developments and progress in PCB technology. If more students are made aware of the opportunities in the PCB industry, we can bring in fresh, new minds that will look at our manufacturing limitations from different perspectives. The more interest in PCB manufacturing we can bring to young engineers, the better. Although it is necessary to gain overall interest in PCBs, it’s important that we steer some in the direction of engineering capital equipment (i.e., printers, etchers, platers, etc.). If PCB manufacturers are to get an edge in the market, it is likely to come from advancements in fabrication technology. This is because innovation in this area will effectively lead to greater opportunities in PCB quality, productivity, and overall profit. In principle, if the equipment manufacturers grow and innovate, so should the rest of the industries they support. Making the upcoming generations interested in all aspects of PCB fabrication may just be the adaptation our industry needs to handle the changing wants and needs of the market. Once the new generation gains interest in our industry, PCB manufacturers should have a bright future ahead of them.
That leaves us with the question of how we can best appeal to the next generation and get them interested in PCBs. Creating outreach programs and other similar efforts are likely the way to go because half of the battle is bringing awareness of how PCBs are made. I propose that the other half of the battle is introducing the nuances of our industry and the current matters we would like to improve. If you are trying to appeal to young engineers, the best way to do that is to give them a challenge and show them there is still plenty of room for intellectual growth in our industry.
This column originally appeared in the October 2022 issue of PCB007 Magazine.
More Columns from The Chemical Connection
The Chemical Connection: Sales Organization from a Capital Equipment PerspectiveThe Chemical Connection: Through-glass Vias in Glass Substrates
The Chemical Connection: Reducing Defects in Circuit Board Production
The Chemical Connection: Common Misconceptions in Wet Processing
The Chemical Connection: Surface Finishes for PCBs
The Chemical Connection: Earthquakes, Astronauts, and Aquatics—A Lighter Look at the Past
The Chemical Connection: Better Fabs Attract a Better Workforce
The Chemical Connection: Can Changing Spray Nozzles Improve My Etch Quality?