-
- News
- Books
Featured Books
- design007 Magazine
Latest Issues
Current IssueRules of Thumb
This month, we delve into rules of thumb—which ones work, which ones should be avoided. Rules of thumb are everywhere, but there may be hundreds of rules of thumb for PCB design. How do we separate the wheat from the chaff, so to speak?
Partial HDI
Our expert contributors provide a complete, detailed view of partial HDI this month. Most experienced PCB designers can start using this approach right away, but you need to know these tips, tricks and techniques first.
Silicon to Systems: From Soup to Nuts
This month, we asked our expert contributors to weigh in on silicon to systems—what it means to PCB designers and design engineers, EDA companies, and the rest of the PCB supply chain... from soup to nuts.
- Articles
- Columns
Search Console
- Links
- Media kit
||| MENU - design007 Magazine
Forming Standards for Ultra HDI
October 25, 2022 | Andy Shaughnessy, Design007 MagazineEstimated reading time: 3 minutes
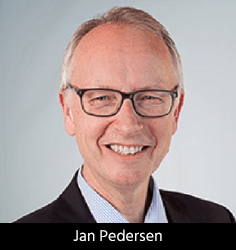
To get the latest news about ultra high-density interconnections (UHDI), we checked in with Jan Pedersen, NCAB Group’s director of technology. Jan is co-chair of IPC D-33AP, and a great source of overall DFM expertise as well. We asked him to give us a snapshot of UHDI in the industry, where we’re headed, and what this means to PCB designers.
Q: How do you define ultra HDI? What is the cutoff in mils or microns?
A: UHDI is defined in the IPC UHDI task group as a PCB design with lines and spaces below 50 microns, dielectric thickness below 50 microns, and microvias below 75 microns. These are attributes beyond the existing IPC-2226 Producibility level C.
Q: Tell us about your work on IPC’s UHDI committee. What are you working on right now? Are the standards keeping up with UHDI technology?
A: The UHDI task group has now developed a basic description and parameters. We are ready to hand over our work to the next group at IPC to start building the standards structure, starting with design, followed by performance and acceptance standards.
The standards will keep up with UHDI technology, but this will need our full attention for the standard to reflect current production capabilities globally.
Q: Much of the ultra HDI we see involves semi-additive technology. Can you clear up the differences between mSAP and A-SAP, and what it means to designers and design engineers?
A: SAP stands for semi-additive processes, and there are a few versions out there such as mSAP and A-SAP. We call them semi-additive because they all start with a thin layer of copper before creating the circuitry. This can be either from a copper-clad material, similar to what we use in traditional PCB manufacturing but with thinner copper, or a non-clad material where the PCB factory plates the seed layer. The difference between mSAP and A-SAP is the thickness of the seed layer where mSAP starts with a copper layer, typically 3–4 microns, while A-SAP starts from an unclad material activating the surface, adding a very thin chemical copper layer of less than 1 micron. Then both processes use photolithographic methods to plate up copper traces to around 20-micron thickness before flash etching the seed layer. Basically, the thickness of the seed layer, as we see with A-SAP, is the main factor for the process to create thinner traces.
Q: How is designing in the ultra HDI arena different from designing a typical PCB? What are some of the hurdles?
A: Designing ultra HDI is a challenge today because of a lack of standards, both for PCB production and material availability. The big hurdle today is fabrication availability. There are processes and some materials available, but very few PCB factories can offer anything below 40-micron trace and space. Some factories claim to offer UHDI, but that is very often only down to 35- to 40-micron traces, while the components you want to use requires traces and spaces below 30 microns.
Q: Are there any resources—books, websites, instructors, etc.—for UHDI design techniques?
A: For designers who want to learn more about UHDI, there are a limited number of resources. I would start with Tara Dunn’s Altium blogs and her I-Connect007 columns, which often cover semi-additive and UHDI. Anyone considering moving into ultra HDI should follow the NCAB blogs, available on our website and on LinkedIn. Read everything that you can.
Q: What advice would you give designers who are considering moving into UHDI?
A: The best advice I can offer is to find a supplier and be sure that you design within their capabilities. NCAB has a plan to be providing high-mix, low-volume UHDI starting as early as 2023. Today all factories that offer less than 35-micron traces have extremely long lead times. Not to sound commercial, but NCAB Group has a clear plan to change that. We are not there yet but will be very soon.
I am leading the NCAB Technical Council, and one of the focus teams is working actively with ultra HDI. As soon as we have a factory that can offer shorter lead times on UHDI, we will develop design guidelines and webinars, and provide workable parameters for designers. We need safe parameters to secure manufacturing yields and product quality from the start. It is paramount for NCAB Group to be transparent about what we can offer and how ready we are with new technologies.
This interview originally appeared in the October 2022 issue of Design007 Magazine.
Suggested Items
Unlocking Advanced Circuitry Through Liquid Metal Ink
10/31/2024 | I-Connect007 Editorial TeamPCB UHDI technologist John Johnson of American Standard Circuits discusses the evolving landscape of electronics manufacturing and the critical role of innovation, specifically liquid metal ink technology, as an alternate process to traditional metallization in PCB fabrication to achieve ever finer features and tighter tolerances. The discussion highlights the benefits of reliability, efficiency, and yields as a tradeoff to any increased cost to run the process. As this technology becomes better understood and accepted, even sought out by customers and designers, John says there is a move toward mainstream incorporation.
Fresh PCB Concepts: The Critical Nature of Copper Thickness on PCBs
10/31/2024 | Team NCAB -- Column: Fresh PCB ConceptsPCBs are the backbone of modern electronics and the copper layers within these boards serve as the primary pathways for electrical signals. When designing and manufacturing PCBs, copper thickness is one of the most critical factors and significantly affects the board’s performance and durability. The IPC-6012F specification, the industry standard for the performance and qualification of rigid PCBs, sets clear guidelines on copper thickness to ensure reliability in different environments and applications.
Book Excerpt: The Printed Circuit Designer’s Guide to... DFM Essentials, Ch. 1
10/25/2024 | I-Connect007The guidelines offered in this book are based on both ASC recommendations and IPC standards with the understanding that some may require adjustment based on the material set, fabricator processes, and other design constraints. This chapter details high-frequency materials, copper foil types, metal core PCBs, and the benefits of embedded capacitance and resistor materials in multilayer PCBs.
The Cost-Benefit Analysis of Direct Metallization
10/21/2024 | Carmichael Gugliotti, MacDermid AlphaCarmichael Gugliotti of MacDermid Alpha discusses the innovative realm of direct metallization technology, its numerous applications, and significant advantages over traditional processes. Carmichael offers an in-depth look at how direct metallization, through developments such as Blackhole and Shadow, is revolutionizing PCB manufacturing by enhancing efficiency, sustainability, and cost-effectiveness. From its origins in the 1980s to its application in cutting-edge, high-density interconnects and its pivotal role in sustainability, this discussion sheds light on how direct metallization shapes the future of PCB manufacturing across various industries, including automotive, consumer electronics, and beyond.
Connect the Dots: Designing for Reality—Pattern Plating
10/16/2024 | Matt Stevenson -- Column: Connect the DotsIn the previous episode of I-Connect007’s On the Line with… podcast, we painted the picture of the outer layer imaging process. Now we are ready for pattern plating, where fabrication can get tricky. The board is now ready to receive the copper traces, pads, and other elements specified in the original CAD design. This article will lay out the pattern plating process and discuss constraints in the chemistries that must be properly managed to meet the customer's exacting manufacturing tolerances.