-
- News
- Books
Featured Books
- smt007 Magazine
Latest Issues
Current IssueWhat's Your Sweet Spot?
Are you in a niche that’s growing or shrinking? Is it time to reassess and refocus? We spotlight companies thriving by redefining or reinforcing their niche. What are their insights?
Moving Forward With Confidence
In this issue, we focus on sales and quoting, workforce training, new IPC leadership in the U.S. and Canada, the effects of tariffs, CFX standards, and much more—all designed to provide perspective as you move through the cloud bank of today's shifting economic market.
Intelligent Test and Inspection
Are you ready to explore the cutting-edge advancements shaping the electronics manufacturing industry? The May 2025 issue of SMT007 Magazine is packed with insights, innovations, and expert perspectives that you won’t want to miss.
- Articles
- Columns
- Links
- Media kit
||| MENU - smt007 Magazine
SMT Tooling, PSA: 'Perfect Marriage of Innovation and Product'
October 26, 2022 | Nolan Johnson, I-Connect007Estimated reading time: 4 minutes
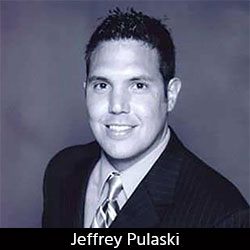
Jeffrey Pulaski describes the recent partnership between SMT Tooling and PSA, which brings SMT Tooling’s innovation and PSA’s manufacturing capabilities together. Pulaski also shares news on product development, and what visitors to SMTA International can expect to see in SMT Tooling’s floor presence.
AUDIO INTERVIEW TRANSCRIPT:
Nolan Johnson: Joining me for this conversation is Jeffrey Pulaski. He is a project manager at SMT Tooling. Jeffrey, thanks for joining me.
Jeffrey Pulaski: Nolan, thank you. It’s a pleasure to be here with you.
Johnson: It’s been in the news recently that SMT Tooling and Production Systems Automation, Incorporated, PSA has joined forces in some fashion. Can you talk to us about that?
Pulaski: Production Systems Automation is owned by Michael McHale, and it deals mainly with automation, machinery, and robotics. We have a contract in the DoD with some drone work, contract work. Now one of the divisions is SMT Tooling, and that came about through Michael and Charlie Moncavage’s relationship.
Johnson: I presume then that there are some market conditions or developments that are helping fuel this partnership. What might those be?
Pulaski: Michael’s interest is always pretty broad. He’s an entrepreneur. And him and Charlie’s relationship is very fruitful for them both. Charlie has been the previous inventor of Grid-lok and Quick-tool, and now his latest rendition of the board support that started this venture is Matrix, so that’s what we’re producing. The market called for tighter tolerances with the way that industry is going with pin placement and tighter tolerance is required. The retooling of Charlie’s invention and the development of Matrix has been a perfect marriage. PSA’s facilities—we have three, one in western Pennsylvania in Lawrence; the main one in Duryea, which is northeast Pennsylvania; then down in Aston toward Philadelphia—we have over 80 plus engineers in house manufacturing facilities and fabrication facilities throughout our campus.
Johnson: So, how do the core competencies for the two companies benefit each other?
Pulaski: So, with Charlie’s innovation of the tooling and Michael’s extensive knowledge of manufacturing and automation, equipment, and fabrication, as the two merged together, it just was a perfect marriage of innovation and product. We’re going to take Charlie’s invention to the next level. We could control the quality of the products put out better. We have elaborate inspection stations and the fabrication portion of PSA, along with its connections throughout the industry is a great place for SMT Tooling to get a lot of traction in the industry.
Johnson: For those who aren’t maybe that familiar with your product, you’ve mentioned, let’s talk a little bit more about that.
Pulaski: Sure. Matrix is a module that is pin-driven. It’s an under-board support for PCBs surface mount tool. This is a revised rendition of the previous invention that Charlie had, Quick-tool, made better. I should say maintenance-free, the production is better, the tolerances are better, pin placement is tighter. So, along with the updates coming through the industry with the PCBs and the tighter tolerance is required for support. Matrix provides that, which no other company can. We right now produce 12-inch, 15-inch, 18-inch, up to 24-inch, but we could do custom sizes. We had produced one as big as 48 inches, which was unprecedented in the industry.
Johnson: Who would be a target user for the Matrix product? There must be some applications for which this just shines.
Pulaski: Yes, of course. Solder paste printers, pick and place machines. Anyone that’s in the PCB production industry that has those machines within their facility, we could help support.
Johnson: What makes the SMT Tooling products and your processes so unique in the industry?
Pulaski: Well, it goes back to that relationship with Michael and Charlie. PSA’s well-established within the automation community and robotics. We have an extensive machine shop, inspection stations. All the work is done in-house. It’s all American made. Charlie’s device is all built within our facility at SMT Tooling. There’s very little outsourcing. Everything is produced right within our facility, so we could control exactly how this is built and inspected; it just makes for a better product.
Johnson: Will you be present at SMTA International in the beginning of November?
Pulaski: Yes, we will. Well, we’re looking forward to that show. We just came from a Long Island show yesterday, and our product was very well received. Along with Matrix, we are planning on launching our own version of a screen printer called the Marksman. It’s a tabletop semi-automatic screen printer targeting the $10,000 to $12,000 price range for low production run, high quality. It entails integrated vision and alignment systems. It’s preconfigured to accept Matrix, which kind of ties the two products together. We’re really excited about this. There’s a lot of innovation that is put into this, and we believe it’s going to offer a lot to the customer, the end user. We will have Matrix at the show and SMTAI coming up here shortly.
Johnson: Thank you for taking the time to talk with us today.
Pulaski: Thank you. My pleasure.
Testimonial
"Advertising in PCB007 Magazine has been a great way to showcase our bare board testers to the right audience. The I-Connect007 team makes the process smooth and professional. We’re proud to be featured in such a trusted publication."
Klaus Koziol - atgSuggested Items
Weller Tools Supports Future Talent with Exclusive Donation to SMTA Michigan Student Soldering Competition
07/23/2025 | Weller ToolsWeller Tools, the industry leader in hand soldering solutions, is proud to announce its support of the upcoming SMTA Michigan Expo & Tech Forum by donating a limited-edition 80th Anniversary Black Soldering Set to the event’s student soldering competition.
Koh Young Appoints Tom Hattori as President of Koh Young Japan
07/21/2025 | Koh YoungKoh Young Technology, the global leader in True 3D measurement-based inspection solutions, announced the appointment of Tom Hattori as President of Koh Young Japan (JKY).
Silicon Mountain Contract Services Enhances SMT Capabilities with New HELLER Reflow Oven
07/17/2025 | Silicon Mountain Contract ServicesSilicon Mountain Contract Services, a leading provider of custom electronics manufacturing solutions, is proud to announce a significant upgrade to its SMT production capability with the addition of a HELLER 2043 MK5 10‑zone reflow oven to its Nampa facility.
Knocking Down the Bone Pile: Addressing End-of-life Component Solderability Issues, Part 4
07/16/2025 | Nash Bell -- Column: Knocking Down the Bone PileIn 1983, the Department of Defense identified that over 40% of military electronic system failures in the field were electrical, with approximately 50% attributed to poor solder connections. Investigations revealed that plated finishes, typically nickel or tin, were porous and non-intermetallic.
SHENMAO Strengthens Semiconductor Capabilities with Acquisition of PMTC
07/10/2025 | SHENMAOSHENMAO America, Inc. has announced the acquisition of Profound Material Technology Co., Ltd. (PMTC), a premier Taiwan-based manufacturer of high-performance solder balls for semiconductor packaging.