Innovation within Sustainable Electronics Manufacturing
November 11, 2022 | PRNewswireEstimated reading time: 2 minutes
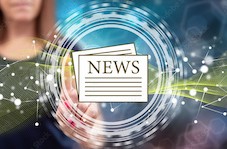
With COP27 underway, sustainability is once again at the forefront of global discussion. Debates surrounding emissions reductions, water security, and renewable energy are at centre-stage with many politicians, businesses, investors, and think tanks enthusiastic to bring about meaningful change. In IDTechEx's report, "Sustainable Electronics Manufacturing 2023-2033", methods of reducing emissions within one of the most polluting industries are evaluated and discussed with a view to cost-effective and widespread implementation.
With the electronics industry accounting for 4 % of global greenhouse gas emissions, it is a sector that requires substantial innovation to reduce its environmental footprint. IDTechEx's latest report explores how the environmental impact of manufacturing printed circuit boards (PCBs) and integrated circuits (ICs) can be reduced through innovative materials choices and processing methods. This includes implementing low-temperature processing, eliminating superfluous wasteful steps, recycling and re-using materials where possible, and adopting novel approaches where the long-term potential is foreseen. IDTechEx expects that within a decade, 20% of PCBs could be manufactured using more sustainable methods such as dry etching, printing, and low-temperature solder component attachment. The report explores what many well-known electronics manufacturers are doing to enact cost-effective and sustainable measures, including Samsung, IBM, Intel, Toshiba, Apple, and Dell, among others.
Sustainable Manufacturing Methods Covered in this Report
The report assesses sustainable methods of electronics manufacturing and concentrates on innovations within printed circuit boards and integrated circuits. The report evaluates how sustainable innovation can drive forward the new era of flexible electronics and covers different materials and manufacturing processes that can deliver effective long-term sustainability improvements. Covering each key stage of the value chain for PCB and IC manufacturing, the report identifies areas that can benefit from innovation. These are compared not just in terms of the emissions, materials, and water consumption but also in terms of what is scalable and cost-effective to implement.
The analysis covers the following areas:
- Different material choices for PCB and IC substrates
- Alternatives to traditional wet etching.
- Additive approaches such as printing metallic traces.
- Low-temperature component attachment materials
- Shifts towards new dielectrics as integrated circuits reduce in dimension.
- End of life analysis
Emerging Flexible Electronics Benefit From Sustainable Innovations
Most electronics today are manufactured on rigid substrates; however, flexible electronics are on the rise as a wide range of different application areas grow, including wearable technology and flexible displays. The flexible PCB substrate market is expected to reach US$1.2 billion by 2033, largely led by polyimide – a bendable plastic substrate already used in the PCB industry. Polyimide is an expensive material and is also environmentally unfriendly. The report discusses the use of cheaper materials such as polyethylene terephthalate (PET) but also biodegradable materials such as paper and natural fibers. While these appear some way away from appearing in everyday devices, many household names have pursued pilot projects employing biodegradable PCBs, including Microsoft and Dell.
A key advantage to the next generation of electronics is that its success depends upon innovation. Liberated from traditional processing routes, pioneering approaches can be adopted from the get-go that save time, reduce waste, and cut emissions. These approaches may involve something relatively simple such as switching to low-temperature solder, or something more revolutionary such as adopting a partial or fully additive manufacturing approach. The advantages and compromises to implementing sustainable innovations are fully evaluated in IDTechEx's report, "Sustainable Electronics Manufacturing 2023-2033".
Testimonial
"Our marketing partnership with I-Connect007 is already delivering. Just a day after our press release went live, we received a direct inquiry about our updated products!"
Rachael Temple - AlltematedSuggested Items
Indium Corporation to Highlight High-Reliability Solder Solutions at SMTA Guadalajara Expo
09/04/2025 | Indium CorporationIndium Corporation, a leading materials refiner, smelter, manufacturer, and supplier to the global electronics, semiconductor, thin-film, and thermal management markets, will feature a range of innovative, high-reliability solder products for printed circuit board assembly (PCBA) at the SMTA Guadalajara Expo and Tech Forum, to be held September 17-18 in Guadalajara, Mexico.
Dr. Jennie Hwang to Present on ‘Solder Joint Reliability’ at SMTA International 2025
09/03/2025 | Dr. Jennie HwangDr. Jennie Hwang to address “Solder Joint Reliability” at the 2025 SMTA International Conference on Monday, October 20. Leveraging her decades of extensive real-world experiences and deep knowledge,
Indium to Highlight Energy-Efficient, High-Reliability Solder Solutions for EV and Electronics at Productronica India
09/03/2025 | Indium CorporationIndium Corporation, a leading materials refiner, smelter, manufacturer, and supplier to the global electronics, semiconductor, electric vehicle (EV), thin-film, and thermal management markets, will feature a range of sustainable, high-reliability solder products at Productronica India, to be held September 17-19 in Bengaluru, India.
Altus Supports Datalink Electronics with Advanced Selective Soldering Solution to Boost Manufacturing Efficiency
09/02/2025 | Altus GroupDatalink Electronics has partnered with Altus Group to integrate a cutting-edge automated soldering solution, enhancing its production capabilities and reinforcing its strategic focus on quality, automation, and scalability.
Connect the Dots: How to Avoid Five Common Causes of Board Failure
09/04/2025 | Matt Stevenson -- Column: Connect the DotsBoards fail for various reasons, and because I’ve been part of the PCB industry for a long time, I’ve seen most of the reasons for failure. As part of my ongoing crusade to help designers design for the reality of manufacturing, here are five common causes for board failure and how to avoid them.