-
- News
- Books
Featured Books
- pcb007 Magazine
Latest Issues
Current IssueInventing the Future with SEL
Two years after launching its state-of-the-art PCB facility, SEL shares lessons in vision, execution, and innovation, plus insights from industry icons and technology leaders shaping the future of PCB fabrication.
Sales: From Pitch to PO
From the first cold call to finally receiving that first purchase order, the July PCB007 Magazine breaks down some critical parts of the sales stack. To up your sales game, read on!
The Hole Truth: Via Integrity in an HDI World
From the drilled hole to registration across multiple sequential lamination cycles, to the quality of your copper plating, via reliability in an HDI world is becoming an ever-greater challenge. This month we look at “The Hole Truth,” from creating the “perfect” via to how you can assure via quality and reliability, the first time, every time.
- Articles
- Columns
- Links
- Media kit
||| MENU - pcb007 Magazine
Estimated reading time: 5 minutes
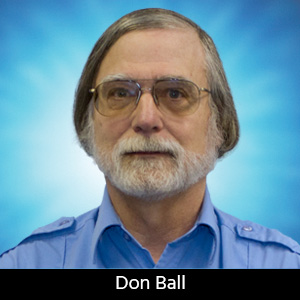
The Chemical Connection: Cupric Chloride Regeneration Options
Cupric chloride (CuCl2), if you recall my June 2022 column “Etchants of the Industry: Cupric vs. Alkaline,” is the second-most used etchant in PCB etching next to alkaline etchant. It holds many benefits such as simple maintenance, easy wastewater treatment, reduced cost of etching, and efficient regeneration. Many times, I have discussed how critical it is to implement regeneration because it allows you to maintain a consistent etch quality and reduces the cost of etching. What makes cupric’s etch regeneration simple is that it is a matter of what you choose to use. Thankfully, utilizing any regeneration option for cupric chloride is as simple as feeding your regeneration chemicals into the etch bath and letting the chemistry take place. Although all are relatively simple to implement, some have certain benefits over others.
When it comes to regeneration for CuCl2, you have three options: hydrogen peroxide (H2O2) and hydrochloric acid (HCl), sodium chlorate (NaClO3) and HCl, or chlorine gas (Cl2). The regeneration reactions for the listed reagents are shown in Table 1, and how these reactions all tie in together is shown in Figure 1.
Hydrogen Peroxide and HCl
The first regeneration option is H2O2 and HCl. One great benefit of this option is it only has one byproduct to the reaction: water. As a byproduct, this water is not problematic because it can be used for maintaining the specific gravity (SG) of your etching solution. As you etch more copper, the SG of your etching solution will increase because of the metal content rising. With water being the byproduct of this reaction, your water consumption will be reduced. What is also useful about this option is that you can use a simple pump system to feed it into your etcher. This pump system would connect to the chemical drums and tie it in with a few controls (i.e., metering pumps, ORP monitors, and/or panel counters). These controls will be used to cue the pump system to provide your etcher with an adequate supply of regenerating reagents (Figure 2).
The drawback of this option is that H2O2 is a thermodynamically unstable molecule, and over time it will decompose and become water. This means the longer it is sitting idly in a drum after opening, the less effective your regeneration controls will be because you will no longer have an accurate understanding of your H2O2 concentration. There are typically some additives to ensure the H2O2 does not break down too quickly, but it is still a possibility. With H2O2 there may also be additional safety measures required since it is a highly reactive oxidizer.
Sodium Chlorate and HCl
Utilizing NaClO3 and HCl for regeneration will look similar to how regeneration is done with H2O2 and HCl, since it can also be set up with a simple pump system. Utilizing these reagents provides the same benefit of reducing water consumption in maintaining SG. NaClO3 will give the same benefits as H2O2 without the worry of your chemicals decomposing over time. Both NaClO3 and H2O2 are strong oxidizers, but NaClO3 is easier and safer to handle. Perhaps these are the reasons why regeneration through NaClO3 is the most popular of the three options.
Although it has some great benefits, it has the drawback where water is no longer the only byproduct. For this reaction, NaCl is also a byproduct and over time, as you are etching and performing regeneration, you will accumulate salt inside your etcher. At a certain point, the salt content will be so high that the salt will take the form of a solid inside your etcher, which can be difficult to remove. This can be problematic from a few standpoints. From a production standpoint, it can interfere with how effective your etching process is by plugging up your nozzles and it can cause abrasions on your PCBs or damage the photoresist. From another standpoint, it can also impact the longevity of your equipment. If it goes untreated long enough, you may see more mechanical issues with your machine. Although salt build-up could be severely problematic, it can easily be prevented with routine maintenance and cleaning.
Chlorine Gas
Chlorine gas for regeneration may be the most efficient option available. This is because the Cl2 regeneration reaction produces no byproducts that can accumulate or mess with the balance of the etchant. It is also highly economical because the cost of the gas is significantly lower than the other reagents. Although it is generally considered the best option, it is a method that is not highly used due to the number of regulations that are imposed on the use of Cl2. Even with the reagent cost being significantly low, in some cases, the amount of regulations and safety precautions add up to making it more expensive than the counterpart options.
If you do get the opportunity to use Cl2 for regeneration, you should note that feeding it into your etching system will be a different process than the previous options. To bring the Cl2 into your etching solution you will need to pull it into your etcher by vacuum. This vacuum will pull the Cl2 from the storage tank and introduce it to the spent etchant via sparging or feeding into a recirculating loop (see Figure 3). This feeding method is a safety measure to prevent major releases of Cl2 in case there is a leak in one of the connections between the tank and the etcher.
Summary
Regenerating CuCl2 can be relatively simple, and it is mostly a matter of picking which option you want. Which option you choose will likely depend on your location. The best option to go for is chlorine gas regeneration because it is cost-effective, but depending on your location, there may be too many regulations and barriers to entry for that to be a feasible option. If Cl2 is not a valid choice for you, then the other two options can come down to many different factors that can be unique to your process. With the information I have provided, you should be able to make an informed decision about which one would suit your cupric etch process best.
References
- “Process Guidelines for Cupric Chloride Etching,” Chemcut.net
This column originally appeared in the November 2022 issue of PCB007 Magazine.
More Columns from The Chemical Connection
The Chemical Connection: Sales Organization from a Capital Equipment PerspectiveThe Chemical Connection: Through-glass Vias in Glass Substrates
The Chemical Connection: Reducing Defects in Circuit Board Production
The Chemical Connection: Common Misconceptions in Wet Processing
The Chemical Connection: Surface Finishes for PCBs
The Chemical Connection: Earthquakes, Astronauts, and Aquatics—A Lighter Look at the Past
The Chemical Connection: Better Fabs Attract a Better Workforce
The Chemical Connection: Can Changing Spray Nozzles Improve My Etch Quality?