-
- News
- Books
Featured Books
- pcb007 Magazine
Latest Issues
Current IssueInventing the Future with SEL
Two years after launching its state-of-the-art PCB facility, SEL shares lessons in vision, execution, and innovation, plus insights from industry icons and technology leaders shaping the future of PCB fabrication.
Sales: From Pitch to PO
From the first cold call to finally receiving that first purchase order, the July PCB007 Magazine breaks down some critical parts of the sales stack. To up your sales game, read on!
The Hole Truth: Via Integrity in an HDI World
From the drilled hole to registration across multiple sequential lamination cycles, to the quality of your copper plating, via reliability in an HDI world is becoming an ever-greater challenge. This month we look at “The Hole Truth,” from creating the “perfect” via to how you can assure via quality and reliability, the first time, every time.
- Articles
- Columns
- Links
- Media kit
||| MENU - pcb007 Magazine
Estimated reading time: 4 minutes
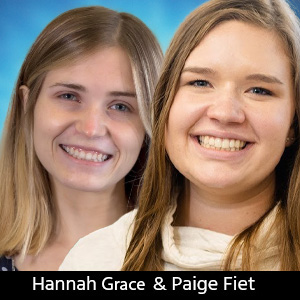
The New Chapter: A Day in the Life of a Process Engineer
College students often ask me what a day in the life of a process engineer entails. While each day is vastly different than the last, here is a “typical” day in the life of a process engineer in the PCB manufacturing industry.
7:45–8:30 a.m.
My day begins with a giant tumbler of black coffee. My morning ritual includes checking emails, following up on previous shifts’ daily logs, and reviewing the previous day’s quality and throughput reports. From there, I begin my action item list. I will write down any concerns from the shift logs, emails that need to be responded to, and any jobs that need to be reviewed for poor yields. On Monday mornings, this time will include creating a chart for my department of the previous week’s defects and ways we can work to improve the top defects.
8:30–10 a.m.
My coffee has now been completed with the first wave of emails for the day. Time to check in with my department. With 10 processes and over 50 operators, my department is one of the largest at TTM-Logan. So, with my action list in hand, I will walk through each of the processes in chronological order. At each stop along the way, I ask the operators how things are going, verify the machine settings, answer any questions, and review any jobs that are on hold for engineering review. If a machine is down or a new tool is needed, it will be added to the action list for the day.
10–11 a.m.
Wow, the morning is flying by! At this point, I am getting a start on my to-do list. Typically, this involves answering questions about manufacturing for my front-end department, ordering new materials for the solder mask department, and/or checking in with the quality team on their audits of my department. Occasionally, this time is spent meeting with other process engineers at the Logan facility to discuss interdepartmental issues and brainstorm solutions to the problem(s). Other times, I am on a bi-weekly call with a fellow solder mask engineer at another facility discussing best practices and ways to help the other site improve.
11 a.m.–noon
Now that things have quieted down (for now), I begin working on a long-term research project to test machine capabilities. I will typically meet with a senior front-end engineer to bring my test vehicle design to life. We discuss the purpose of the test along with what materials might be best to use. Once the panels are created, this time will be used to process them through my department. I will change the necessary settings and document as many variables as possible for later data analyzation.
Noon–1 p.m.
Lunch time! Sometimes I will head out for burgers with coworkers but most of the time you can find me at home enjoying lunch with my cat.
1–1:30 p.m.
Back in the office and I’m heading straight to my department. This time it’s a quicker run-through to answer any new questions, make processing decisions, and confirm proper completion on any maintenance.
1:30–2:30 p.m.
Time to meet with the solder mask department leaders. Every other week, we meet to discuss quality trends, improvement plans, and production complaints.
2:30–3 p.m.
Day shift is now done, and swing shift is starting their workday. I head down to the department and join them for their start-of-shift stretching session. While they stretch, we review the previous day’s quality and throughput. Again, if it’s a Monday, we will review the prior week’s quality concerns.
3–4:30 p.m.
Back to my research project. If need be, I will review my progress with the department’s technician and ask for help in furthering my testing. If the test vehicles are ready for analysis, I will review the designated points under various microscopes and will typically take my own cross-sections for further review. Next begins the analysis. All data and images will be recorded and analyzed based on my previous test plan. Once these are understood, they will drive changes to the manufacturing capability and processing of parts.
4:30–5 p.m.
After one last quick walk-through in the department, it is time to answer any unread emails and start a to-do list for the next day.
Of course, there is no typical day in PCB manufacturing. Although ideal, this timeline is not always accurate. Some days involve hours of hands-on work with machines and digging into root causes. Other days, I am at my desk updating processes and creating temporary process instructions to test a new process. One week may be spent visiting another facility to learn about their processing while the next may include working with suppliers to install new equipment. I’ve come to love the unpredictability of the job. Each day brings its own challenges and excitement.
This column originally appeared in the November 2022 issue of PCB007 Magazine.
More Columns from The New Chapter
The New Chapter: The Benefits of Continuing EducationThe New Chapter: Navigating Maternity Leave in the Electronics Industry
The New Chapter: The Impact of Parasitics on PCB Design
The New Chapter: I’ve Found My ‘Why’
The New Chapter: Artificial Intelligence in PCB Design
The New Chapter: Lessons From the Best Engineer I’ve Ever Known
The New Chapter: Attracting ‘Generation Green’
The New Chapter: Dip Your Hand in the IPC APEX EXPO Candy Jar