How Intel Supports a Circular Economy
November 25, 2022 | IntelEstimated reading time: 3 minutes
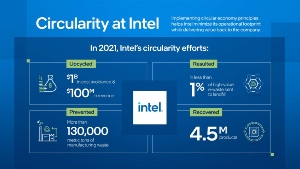
An integral part of Intel’s sustainability strategy is reducing waste, while finding innovative ways to recover, reuse and upcycle. This “circular economy” approach means keeping products and materials in use for as long as possible and then giving them a new life. Implementing circular economy principles helps Intel minimize its operational footprint while delivering value back to the company. In 2021, Intel’s circularity efforts delivered over $100 million in revenue, more than $1 billion in cost avoidance and enabled the company to avoid, recycle, reuse or recover more than 130,000 metric tons of manufacturing waste.
“Keeping waste out of landfills is a critical priority for reducing our operational footprint as we deliver the technologies that power our digital world. Intel’s circular economy practices are a win-win – not only are they better for the environment but they also reduce our operational costs. These efforts benefit our business, customers, stakeholders and the communities in which we operate," says Keyvan Esfarjani, Intel executive vice president, chief global operations officer and general manager of Manufacturing, Supply Chain and Operations
What It Means for Intel’s Manufacturing: Much of Intel’s waste is generated by construction and manufacturing activities. In order to meet its ambitious 2030 goals to achieve zero waste to landfill and implement circular economy strategies for 60% of its manufacturing waste streams, the company is looking across the business to find ways to upcycle materials. Examples include:
To enable solvent reuse, Intel works with vendors to separate one of its primary solvents used in the wafer fabrication etch process from other solvents. In 2021, these efforts recovered more than 8,000 metric tons of the solvent, which was then sold back through a third-party marketplace. Looking ahead, new Intel fabs will have collection systems specifically for this solvent, making it easier to upcycle and moving toward full circularity.
To minimize packaging waste as products are transferred between Intel sites, boxes have been redesigned for reuse by using latches instead of sealing tape. Together with new packaging guidelines, this has reduced demand for packaging materials by more than 180 metric tons per year.
In 2021, Intel and its suppliers repurposed more than 1,700 metric tons of material containing precious metals from 40 countries. These efforts support metal reuse, minimize e-waste and highlight the importance of the value chain coming together.
What It Means for Product Design: Intel also designs for circularity in its products. For example:
As part of its announcement to achieve net-zero greenhouse gas emissions across its operations by 2040, Intel committed to help customers achieve carbon reductions in platform designs. This includes innovations like circuit boards that can be more easily separated into materials and components when recycling, reducing e-waste.
All Intel NUCs are designed to allow for upgradeability and repairability. In 2021, the team achieved a 91% recovery rate of products, in part due to asset recovery from product returns. Further, some of Intel’s NUC mini-PCs use up to 75% post-consumer recycled (PCR) plastics. This is a challenge, because recycling plastics can cause the material to become less stable. Therefore, the amount used is carefully controlled so the Intel NUC remains reliable and can sustain drops, shocks, vibration and other extreme exposure.
“Sustainability can’t be an add-on; it needs to be factored in from the beginning,” says Jennifer Huffstetler, Intel’s chief product sustainability officer “By harnessing Intel’s prowess as an integrated design manufacturer, we can accelerate adoption and scale availability of more sustainable silicon features, products and solutions that help reduce climate impact. We are uniquely positioned to partner with and help our customers achieve their sustainability goals.”
What It Means for Product Longevity: Extending the life of products is a critical component of the circular economy — it reduces additional consumption of energy and materials needed to create new assets. For example:
Across a global network of test and repair sites, product returns are recovered for use as replacement spare stock or sold in reuse markets. This helped Intel achieve a greater than 50% recovery and reuse rate on product returns in 2021.
Intel collaborates with the Open Compute Project (OCP) to advance modular designs, establish carbon footprint metrics and set reduction goals. The OCP’s Data Center-Modular Hardware system is a new server design that places components in specific modules that can be removed independently of the entire platform. The result will be server elements that can be reused generation over generation — leading to significantly lower e-waste.
Improved hardware modularity and repairability can extend the life of a PC, but a common barrier for donation or resale is that users often don’t know how to erase stored data. One benefit Intel offers for business customers is remote secure erase in vPro platforms, which makes it easier to erase the entire solid-state drive (SSD). This streamlines businesses’ ability to prolong the life of used technologies.
Testimonial
"Our marketing partnership with I-Connect007 is already delivering. Just a day after our press release went live, we received a direct inquiry about our updated products!"
Rachael Temple - AlltematedSuggested Items
Meet the Author Podcast: Martyn Gaudion Unpacks the Secrets of High-Speed PCB Design
07/16/2025 | I-Connect007In this special Meet the Author episode of the On the Line with… podcast, Nolan Johnson sits down with Martyn Gaudion, signal integrity expert, managing director of Polar Instruments, and three-time author in I-Connect007’s popular The Printed Circuit Designer’s Guide to... series.
Intervala Hosts Employee Car and Motorcycle Show, Benefit Nonprofits
08/27/2024 | IntervalaIntervala hosted an employee car and motorcycle show, aptly named the Vala-Cruise and it was a roaring success! Employees had the chance to show off their prized wheels, and it was incredible to see the variety and passion on display.
KIC Honored with IPC Recognition for 25 Years of Membership and Contributions to Electronics Manufacturing Industry
06/24/2024 | KICKIC, a renowned pioneer in thermal process and temperature measurement solutions for electronics manufacturing, is proud to announce that it has been recognized by IPC for 25 years of membership and significant contributions to electronics manufacturing.
Boeing Starliner Spacecraft Completes Successful Crewed Docking with International Space Station
06/07/2024 | BoeingNASA astronauts Barry "Butch" Wilmore and Sunita "Suni" Williams successfully docked Boeing's Starliner spacecraft to the International Space Station (ISS), about 26 hours after launching from Cape Canaveral Space Force Station.
KIC’s Miles Moreau to Present Profiling Basics and Best Practices at SMTA Wisconsin Chapter PCBA Profile Workshop
01/25/2024 | KICKIC, a renowned pioneer in thermal process and temperature measurement solutions for electronics manufacturing, announces that Miles Moreau, General Manager, will be a featured speaker at the SMTA Wisconsin Chapter In-Person PCBA Profile Workshop.