-
- News
- Books
Featured Books
- pcb007 Magazine
Latest Issues
Current IssueSales: From Pitch to PO
From the first cold call to finally receiving that first purchase order, the July PCB007 Magazine breaks down some critical parts of the sales stack. To up your sales game, read on!
The Hole Truth: Via Integrity in an HDI World
From the drilled hole to registration across multiple sequential lamination cycles, to the quality of your copper plating, via reliability in an HDI world is becoming an ever-greater challenge. This month we look at “The Hole Truth,” from creating the “perfect” via to how you can assure via quality and reliability, the first time, every time.
In Pursuit of Perfection: Defect Reduction
For bare PCB board fabrication, defect reduction is a critical aspect of a company's bottom line profitability. In this issue, we examine how imaging, etching, and plating processes can provide information and insight into reducing defects and increasing yields.
- Articles
- Columns
- Links
- Media kit
||| MENU - pcb007 Magazine
Estimated reading time: 5 minutes
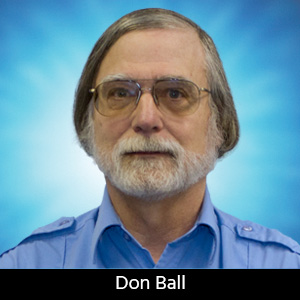
The Chemical Connection: The Subtractive Vision
The November 2022 issue of PCB007 Magazine included a fair amount of discussion on the growing need for ultra-high-density interconnects (UHDI), an area replete with manufacturing challenges due not only to the feature sizes this technology requires (< 50 micron or < 2 mils), but also the lack of familiarity U.S. manufacturers have with this technology. In an interview with Calumet’s Todd Brassard and Meredith LaBeau, they stated that the U.S. is roughly 30 years behind the curve in manufacturing UHDI, which is likely the result of companies offshoring UHDI manufacturing for many years. How can we catch back up?
In an interview titled “Understanding the UHDI Market,” Calumet’s Todd Brassard and Meredith LaBeau stated that the U.S. is roughly 30 years behind the curve in manufacturing UHDI, which is likely the result of companies offshoring UHDI manufacturing for many years. With this gap in manufacturing expertise, we are left asking: How can we catch up? The CHIPS Act may help us shine some light on semiconductor technologies, but if we truly want to see the rapid change necessary to successfully compete against overseas companies that have been in this business for over 20 years, we will need an edge in the market. To get ahead of the competition, we need to push for improvements in subtractive processes and move toward a subtractive-driven PCB fabrication process.
From Semi-additive to Subtractive Manufacturing
By subtractive-driven process, I am referring to a PCB manufacturing process that does not require the use of a semi-additive process (SAP) to meet specifications. Moving to a subtractive-driven process for manufacturing PCBs would significantly impact the industry. Currently, SAP is necessary to obtain ultra-high-definition features; but because SAP requires additional plating steps, PCB fabrication becomes much more expensive. This is because plating is a technically challenging process, requiring lots of expertise and time on the part of highly skilled workers. Plating is also a lengthy process that adds to manufacturing time. With so many factors at play in producing UHDI resolution, there’s always a significant chance that some panels will not meet specifications—especially considering the current state of expertise and technology in the United States. For U.S. manufacturers, UHDI is very much a high-cost low-yield process. The industry has been exploring different ways to make fine features more obtainable, but so far, if you want to have a high-volume production facility, there is no way around SAP.
Although the situation puts the U.S. at a disadvantage, what if it we could skip the middle plating processes entirely while still achieving UHDI level resolution? This may be the PCB fabricator’s dream, but a subtractive-driven process might make this dream a reality. Here is how a subtractive-driven process could theoretically benefit manufacturers:
- More floor space
- Reduced fabrication time
- Less need for specialized workers
- Reduction of plating chemicals in storage
- Reduction of waste from plating processes
- Less process maintenance
If you can eliminate the need for the middle plating processes, your PCB fabrication process will become more efficient. To realize this goal, the industry would need to overcome several barriers.
Revitalizing Copper Etch Chemistry
To become independent from SAP, we need to obtain better etch factors. Recall that etch factor is the ratio of downward etching to sideways etching. In the field of copper etching, the current standard etch factor is 3:1, but can go as high as 4:1 depending on the etchant being used. If we want to side-step SAP and have a subtractive approach to UHDI resolution, we need to obtain a bare minimum etch factor. Feature size requirements will depend on the final copper thickness needed (see Figure 1).
As shown from the diagram, the finer the features, the bigger the jump in etch factor requirements. For example, if we want to etch finer features on panels with thicker copper layers, our etch factors must compensate for that extra etch depth. Unfortunately, regarding copper, there is currently no sufficient way to dramatically improve etch factor. While there is some room for improvement on the fluid dynamics end, to reach etch factors of 20:1 or 40:1, we will need to see an improvement in the base chemistry.
An improvement could look like an entirely new etchant, or an additive to the etchants that are currently used through the industry. As I mentioned in my August 2022 column “The Etch Factor,” we did get fairly close to having straight sidewalls with a PCB etchant via an additive to ferric chloride etchant that helped restrict the sideways etch. This etching process—called PERI etch—never took off in PCB manufacturing because it requires an etchant that can’t be regenerated, thus significantly increasing the cost of etching. However, since we have had modest success in approaching the high etch factors necessary to break from SAP, focusing our research efforts into copper etch chemistry might result in revolutionary developments for the industry.
To achieve this, we will need to grab the attention of the younger generation (those with a chemistry background, in particular) and bring their attention to this issue. If we can manage to get the next generation and academia invested in copper etch chemistry, we may see a rapid shift in the industry. Even if we discover that etch factors on a scale of 20:1 is impossible, PCB manufacturers still stand to benefit from general improvements in etch factor. Although it would be ideal to achieve fine features without SAP, we can still use SAP to further improve the features we have. Improving etch factors will open doors to obtaining the fine features necessary for UHDI resolution.
Conclusion
Improvements in etch factor will drive PCB manufacturing into the future and potentially allow U.S. manufacturers to get ahead of the market. Improvements in etch factor may result in a rapid shift towards subtractive-driven manufacturing processes. To achieve such progress, significant investment needs to be made in research on copper etching chemistry, which will allow us to determine how far etch factor limitations can be pushed.
This column originally appeared in the January 2023 issue of PCB007 Magazine.
More Columns from The Chemical Connection
The Chemical Connection: Sales Organization from a Capital Equipment PerspectiveThe Chemical Connection: Through-glass Vias in Glass Substrates
The Chemical Connection: Reducing Defects in Circuit Board Production
The Chemical Connection: Common Misconceptions in Wet Processing
The Chemical Connection: Surface Finishes for PCBs
The Chemical Connection: Earthquakes, Astronauts, and Aquatics—A Lighter Look at the Past
The Chemical Connection: Better Fabs Attract a Better Workforce
The Chemical Connection: Can Changing Spray Nozzles Improve My Etch Quality?