-
- News
- Books
Featured Books
- smt007 Magazine
Latest Issues
Current IssueWhat's Your Sweet Spot?
Are you in a niche that’s growing or shrinking? Is it time to reassess and refocus? We spotlight companies thriving by redefining or reinforcing their niche. What are their insights?
Moving Forward With Confidence
In this issue, we focus on sales and quoting, workforce training, new IPC leadership in the U.S. and Canada, the effects of tariffs, CFX standards, and much more—all designed to provide perspective as you move through the cloud bank of today's shifting economic market.
Intelligent Test and Inspection
Are you ready to explore the cutting-edge advancements shaping the electronics manufacturing industry? The May 2025 issue of SMT007 Magazine is packed with insights, innovations, and expert perspectives that you won’t want to miss.
- Articles
- Columns
- Links
- Media kit
||| MENU - smt007 Magazine
The Nuts and Bolts of Advanced Packaging
January 24, 2023 | I-Connect007 Editorial TeamEstimated reading time: 3 minutes
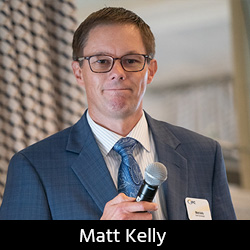
The I-Connect007 Editorial Team asked IPC Chief Technologist Matt Kelly: Will you help us understand what advanced packaging means? This informative conversation touched on topics for both assembly and board fabrication. To that end, we will present this conversation in two parts. In this issue of SMT007 Magazine, Matt helps define not only what advanced packaging is, but the approach EMS companies must take when looking ahead. Think it’s about just adding some new equipment and software? Think again. There are logistics, onboarding, and so much more.
To read an excerpt from this interview that was previously published in the November 2022 issue of PCB007 Magazine, click here.
Nolan Johnson: Matt, I was on the exhibition floor at a technical conference recently and heard a lot of questions about advanced packaging: What is it, how does it apply, what does it mean to EMS providers, etc.? Would you help to define and provide a framework about advanced packaging?
Matt Kelly: There are two terms to define. An advanced package is an electronic component; it’s as simple as that. It has a few elements—it’s comprised of a semiconductor chip (typically silicon) and an interposer and/or substrate—followed by interconnection and assembly of the component. Advanced packaging is the process by which these elements are integrated, assembled, and tested. Advanced packages represent a very specific class of electronic components called active devices. They are called active devices because they contain silicon that provides compute, memory, or other logical device functions. Advanced packaging is critical because the combination of performance, reliability, cost, and functionality that future consumers are demanding can only be met by integrating silicon chips through an advanced packaging process.
Keep in mind this is just one of many different components in a system. While these components are important—they’re the brain of a system—they’re still just one of many different component types. Advanced packaging is a very specific component type. But what types of components are they? These advanced packages have different functions, the first of which is compute. It’s the Intel chip inside your laptop (CPU), graphics accelerators (GPU), AI-based neuro-network chips (NPU). It’s also the solid-state memory (DRAM, NVRAM, NAND Flash) within your phones and computers. These packages can also serve as sensors, analog, mixed signal, and system integration functions. Basically, they are actively doing something within the circuit design. Those are the main functions of an advanced package.
There’s also a difference between definitions of advanced packaging in the past, what it means today, and what it will mean in the future. For example, for at least 50 years, there’s been an active type of component called monolithic silicon, a single chip that is mounted to a substrate and then packaged into a component. A class of those are called multi-chip modules (MCM) and have been in use for decades.
As we move forward with the monolithic silicon, the idea of Moore’s Law becomes less economically viable and advanced packaging is morphing.
For example, when you think about a circuit card from the past, you typically had a compute chip and DRAM (memory banks), which were two different things connected on a printed circuit board. Those are now merging using chiplet-based heterogeneous integration architectures that are now integrating compute and high bandwidth memory (HBM) together within the same electronic package. The result is faster speeds and reduced latencies within a single component package. The resurgence in advanced packaging is driving increased functionality, performance, and speeds within a single device.
Johnson: Increased functionality, increased speed, and an overall smaller package means leaving more real estate available to further integrate more things.
Kelly: Absolutely. For example, if you look at images of a recent Apple Watch teardown, it’s unbelievable what can be accomplished in these small spaces. There are numerous small chips performing many functions within a very small area. Next generation designs continue driving miniaturization, increased functionality, and speeds. On the downside, these configurations are power hungry, meaning there are more power and thermal needs—thus challenges—that need to be addressed with these architectures.
To read this entire conversation, which appeared in the January 2023 issue of SMT007 Magazine, click here.
Suggested Items
The Global Electronics Association Releases IPC-8911: First-Ever Conductive Yarn Standard for E-Textile Application
07/02/2025 | Global Electronics AssociationThe Global Electronics Association announces the release of IPC-8911, Requirements for Conductive Yarns for E-Textiles Applications. This first-of-its-kind global standard establishes a clear framework for classifying, designating, and qualifying conductive yarns—helping to address longstanding challenges in supply chain communication, product testing, and material selection within the growing e-textiles industry.
IPC-CFX, 2.0: How to Use the QPL Effectively
07/02/2025 | Chris Jorgensen, Global Electronics AssociationIn part one of this series, we discussed the new features in CFX Version 2.0 and their implications for improved inter-machine communication. But what about bringing this new functionality to the shop floor? The IPC-CFX-2591 QPL is a powerful technical resource for manufacturers seeking CFX-enabled equipment. The Qualified Product List (QPL) helps streamline equipment selection by listing models verified for CFX compliance through a robust third-party virtual qualification process.
Advancing Aerospace Excellence: Emerald’s Medford Team Earns Space Addendum Certification
06/30/2025 | Emerald TechnologiesWe’re thrilled to announce a major achievement from our Medford, Oregon facility. Andy Abrigo has officially earned her credentials as a Certified IPC Trainer (CIT) under the IPC J-STD-001 Space Addendum, the leading industry standard for space and military-grade electronics manufacturing.
Magnalytix and Foresite to Host Technical Webinar on SIR Testing and Functional Reliability
06/26/2025 | MAGNALYTIXMagnalytix, in collaboration with Foresite Inc., is pleased to announce an upcoming one-hour Webinar Workshop titled “Comparing SIR IPC B-52 to Umpire 41 Functional & SIR Test Method.” This session will be held on July 24, 2025, and is open to professionals in electronics manufacturing, reliability engineering, and process development seeking insights into new testing standards for climatic reliability.
IPC Rebrands as Global Electronics Association: Interview With Dr. John W. Mitchell
06/22/2025 | Marcy LaRont, I-Connect007Today, following a major announcement, IPC is embracing the rapid advancement of technology with a bold decision to change its name to the Global Electronics Association. This name more accurately reflects the full breadth of its work and the modern realities of electronics manufacturing. In this exclusive interview, Global Electronics Association President and CEO Dr. John W. Mitchell shares the story behind the rebrand: Why now, what it means for the industry, and how it aligns with the organization’s mission.