Transistors Repurposed as Microchip ‘Clock’ Address Supply Chain Weakness
January 25, 2023 | Purdue UniversityEstimated reading time: 3 minutes
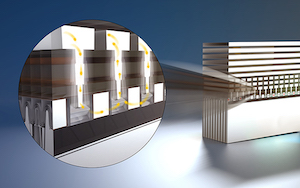
Microchip fab plants in the United States can cram billions of data processing transistors onto a tiny silicon chip, but a critical device, in essence a “clock,” to time the operation of those transistors must be made separately – creating a weak point in chip security and the supply line. A new approach uses commercial chip fab materials and techniques to fabricate specialized transistors that serve as the building block of this timing device, addressing the weak point and enabling new functionality through enhanced integration.
“You would have one chip that does everything instead of multiple chips, multiple fabrication methods and multiple material sets that must be integrated – often overseas,” said Dana Weinstein, a Purdue University professor of electrical and computer engineering, who is developing acoustic resonators with the processes used to produce industry-standard fin field-effect transistors (FinFETs). “There’s a need for America to advance its capabilities in chip manufacturing, and an advance of this nature addresses multiple concerns in supply chain, national security and hardware security. By moving the whole clock inside the processor, you harden the device against clock-glitching attacks, and you enable new functionality such as acoustic fingerprinting of the packaged chip for tamper detection.”
Like all transistors – the devices that undergird modern microelectronics – FinFETs are a voltage-activated on/off gate. As its name suggests, a FinFET passes a current along a fin of semiconducting material that runs through the gate. In the closed, or off, state, the fin does not conduct electricity. A voltage applied to the top of the gate builds an electric charge in the fin, allowing electricity to flow in an open, or on, state.
But transistors must be synchronized to perform operations for microprocessors, sensors and radios used in all electronic devices. The devices that do this are built on sound, the resonant frequency that some structures emit, much as a glass bowl may sound a specific note when pinged. The regular repeating wave of this so-called acoustic resonator serves as a cadence that is incorporated into a larger microelectromechanical system and used to mark time. Current commercial microelectromechanical resonators cannot be fabricated in a standard chip fabrication process and must be made separately and later bundled with microchips for use.
Weinstein’s innovation is to build an acoustic resonator with the existing repertoire of materials and fabrication techniques available in a standard complementary metal oxide semiconductor chip fab. In a recent paper in Nature Electronics, her research team reports its most advanced design to date. Using a commercial process run at the GlobalFoundries Fab 8 facility in New York and described in the GlobalFoundries 14LPP FinFET technology design manual, team members fabricated a specialized set of FinFETs capable of producing a frequency in the range of 8-12?gigahertz, which exceeds the typical native clock rates of microprocessors.
The elegant solution essentially repurposes data processing transistors into a timing device.
“With our approach, the chip fab runs this device through the same process they would use for a computer’s central processing unit or other application,” said Jackson Anderson, a Purdue graduate student in electrical and computer engineering and first author on the Nature Electronics paper. “When the microprocessor and other components are done, so is the resonator. It doesn’t have to undergo further fabrication or be sent somewhere else for integration with a separate microprocessor chip.”
Although the on or off state of a transistor ordinarily directs current to serve as the 0s and 1s of binary code, all transistors can also be used as capacitors to store and release a charge. Weinstein’s team does exactly that with arrays of “drive” transistors, squeezing and releasing a thin layer of dielectric materials between the fin and the gate.
“We’re squeezing those layers between the gate and the semiconductor, pushing and pulling on that thin region between the gate and the fin,” Jackson said. “We do this alternately on adjacent transistors – one compressing, one stretching – building vibrations laterally in the device.”
The drive transistors are sized to guide and amplify the vibrations into building upon themselves into a specific resonant frequency. This, in turn, stretches and compresses the semiconductor material in an adjacent group of “sense” transistors, which alters the characteristics of a current across those transistors, translating the vibration into an electrical signal.
“Every single piece of high-performance electronics that you have uses FinFETs,” Weinstein said. “Integrating these functions advances our microelectronics capabilities beyond just digital microprocessors. If the technology changes, we can adapt, but we would be moving forward with an integrated microprocessor system.”
Testimonial
"Our marketing partnership with I-Connect007 is already delivering. Just a day after our press release went live, we received a direct inquiry about our updated products!"
Rachael Temple - AlltematedSuggested Items
Happy’s Tech Talk #38: Novel Metallization for UHDI
05/07/2025 | Happy Holden -- Column: Happy’s Tech TalkI have been involved in high-density electronics substrates since 1970 when I joined Hewlett-Packard’s RF semiconductor group after college. Figure 1 shows the difference between trace/space lithography for substrates and silicon starting in 1970. My projects involved sapphire circuits for RF devices, but the figure displays the state of PCBs and integrated CMOS circuits and their packaging, not discreet RF devices. Even then, semiconductors were 50X higher density.
New Database of Materials Accelerates Electronics Innovation
05/05/2025 | ACN NewswireIn a collaboration between Murata Manufacturing Co., Ltd., and the National Institute for Materials Science (NIMS), researchers have built a comprehensive new database of dielectric material properties curated from thousands of scientific papers.
New Database of Materials Accelerates Electronics Innovation
05/02/2025 | ACN NewswireIn a collaboration between Murata Manufacturing Co., Ltd., and the National Institute for Materials Science (NIMS), researchers have built a comprehensive new database of dielectric material properties curated from thousands of scientific papers.
Micron Announces Business Unit Reorganization to Capitalize on AI Growth Across All Market Segments
04/23/2025 | MicronMicron Technology, Inc., a leader in innovative memory and storage solutions, announced a market segment-based reorganization of its business units to capitalize on the transformative growth driven by AI, from data centers to edge devices.
Connected Commercial Drone Market to Reach $37.3 Billion Worldwide by 2029
04/04/2025 | Berg InsightBerg Insight, a leading IoT market research provider, today released a new report covering connected commercial drones used for industrial and governmental purposes.