A Quantic Leap into Foils and Embeddeds With John Andresakis
March 29, 2023 | Andy Shaughnessy, Design007 MagazineEstimated reading time: 4 minutes
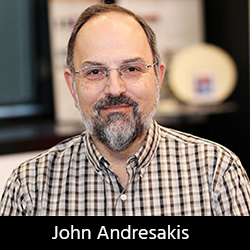
Andy Shaughnessy talks with John Andresakis about how the merger of resistive foil technologies from Ohmega and Ticer has evolved under the new ownership of Quantic. Andresakis also shares how these materials are finding new applications, especially in the embedded component application space, as the company reaches out to the new generation of PCB designers and design engineers.
Andy Shaughnessy: John, it’s been a long time since we talked last. Now you’re with a different company, Ohmega. Tell me about it.
Andresakis: Yes, that’s right. I’m the director of business development for Quantic Ohmega Ticer. A lot of people know Ohmega and Ticer because of their resistive foil technology. A couple of years ago, Arcline investment acquired Ohmega, and then soon after that they bought Ticer and put them under the Quantic group to bring both resistor technologies under one umbrella. The difference is that Ohmega is a plated nickel phosphorous technology and the Ticer approach is a nickel chrome that’s sputtered onto the copper. We can use various copper foils based on what material we need to adhere to and electrical performance.
Shaughnessy: This is a little bit different from what you’ve been doing before.
Andresakis: Yes, I recently came from DuPont, working on laminate materials for the flex and rigid segments of the industry. We also sold embedded capacitor materials, and now I’m working with embedded resistor materials. I’ve kind of been in the embedded business for quite a while and when I worked at Oak-Mitsui we actually were–and continue to be now that they’re Denkai America–the copper supplier to the Ohmega and Ticer technology. So we have a good partnership. We can use a number of copper sources, but they’re the main supplier of our copper foil to make our material.
Shaughnessy: Now you have a new set of customers. Are you seeing different challenges from these customers?
Andresakis: What we’re seeing now is very similar to what copper foil suppliers have been seeing, in that the higher performance materials require lower profile coppers to adhere to their materials. Our material is the interface between the copper foil and the laminate material. We’ve been doing a lot of work in that area to make sure that we have good adhesion to the laminate substrate, and people are putting it into higher performance work. For example, we are on PTFE as well as PPO based materials. We can also be put on polyimide flex materials; it all depends on the application.
And we’re seeing new applications. When the technology first started out it was mainly for resistors in very high-end systems. It’s been used in several space applications; we have material circling the earth and even have material on Mars. It’s very robust and very reliable and it helps with miniaturization and electrical performance. For any place where space and weight are a problem, it’s a great technology, but it’s also seeing more use in commercial applications, like in high-end MEMS microphones.
The technology has been around for decades; it’s not new technology. Now that people are trying to improve electrical performance at higher frequencies, it’s coming into its own. We’re seeing it used in flat panel antennas, optimizing out the resistor elements to get much better electrical performance. It can also be an RF/MW absorber material. Micro-heaters are another application. There are applications where you want spot heating (such as medical and space) where you can actually embed a heater. In space, for example, it’s pretty cold up there. So, if you want to heat circuits–if a circuit or an IC needs a certain temperature to operate, you can locally warm from inside the circuit. Just a few examples where we’re seeing the need for this type of material.
Shaughnessy: What is Ohmega demonstrating at DesignCon now?
Andresakis: We’re showing our different materials and their applications. People know us for resistors, but we’re trying to show the use of our resistive materials like RF microwave-type application. You can use it for a power divider circuit. The idea is we’re trying to spur the creativity inside the designer’s head, let them know the materials are there and some of its attributes so they can add it to their toolbox. Designers always need more tools to get their job done. As an example, we came out with a product that is a termination resistor. It’s a 10-ohm material that you can put right at the end of the trace. So, if you need terminating resistors on the surface, now you can build that right into the circuit. If space is an issue, this allows you to take advantage of this design. While a lot of people know about the technology, our current challenge is to reach a whole new group of designers who haven’t been exposed to it.
Shaughnessy: Sounds like you hit the ground running in this company.
Andresakis: Yes, it’s great working with the combined Ticer and Ohmega teams. We also now have the parent company in Quantic, with companies that make discrete capacitors, RF and microwave modules and other devices, so we have some cross business unit synergies which helps. We can try a new concept with them or do joint marketing in certain areas. Having that corporate group brings additional depth to our organization that we didn’t have before. That helps quite a bit.
Shaughnessy: Great talking with you John. Thanks.
Andresakis: Thank you, Andy.
Testimonial
"We’re proud to call I-Connect007 a trusted partner. Their innovative approach and industry insight made our podcast collaboration a success by connecting us with the right audience and delivering real results."
Julia McCaffrey - NCAB GroupSuggested Items
50% Copper Tariffs, 100% Chip Uncertainty, and a Truce
08/19/2025 | Andy Shaughnessy, I-Connect007If you’re like me, tariffs were not on your radar screen until a few months ago, but now political rhetoric has turned to presidential action. Tariffs are front-page news with major developments coming directly from the Oval Office. These are not typical times. President Donald Trump campaigned on tariff reform, and he’s now busy revamping America’s tariff policy.
Global PCB Connections: Understanding the General Fabrication Process—A Designer’s Hidden Advantage
08/14/2025 | Markus Voeltz -- Column: Global PCB ConnectionsDesigners don’t need to become fabricators, but understanding the basics of PCB fabrication can save you time, money, and frustration. The more you understand what’s happening on the shop floor, the better you’ll be able to prevent downstream issues. As you move into more advanced designs like HDI, flex circuits, stacked vias, and embedded components, this foundational knowledge becomes even more critical. Remember: the fabricator is your partner.
MKS’ Atotech to Participate in IPCA Electronics Expo 2025
08/11/2025 | AtotechMKS Inc., a global provider of enabling technologies that transform our world, announced that its strategic brands ESI® (laser systems) and Atotech® (process chemicals, equipment, software, and services) will showcase their latest range of leading manufacturing solutions for printed circuit board (PCB) and package substrate manufacturing at the upcoming 17th IPCA Show to be held at Pragati Maidan, New Delhi from August 21-23, 2025.
MKS Showcases Next-generation PCB Manufacturing Solutions at the Thailand Electronics Circuit Asia 2025
08/06/2025 | MKS Instruments, Inc.MKS Inc, a global provider of enabling technologies that transform our world, today announced its participation in Thailand Electronics Circuit Asia 2025 (THECA 2025), taking place August 20–22 at BITEC in Bangkok.
Point2 Technology, Foxconn Interconnect Technology Partner to Revolutionize AI Cluster Scalability with Terabit-Speed Interconnect
08/06/2025 | BUSINESS WIREPoint2 Technology, a leading provider of ultra-low-power, low-latency mixed-signal SoC solutions for multi-terabit interconnect, and Foxconn Interconnect Technology (FIT), a global leader in precision interconnect solutions, have signed a Memorandum of Understanding (MOU) to accelerate the commercialization of next-generation Active RF Cable (ARC) and Near Pluggable e-Tube (NPE) solutions.