-
- News
- Books
Featured Books
- pcb007 Magazine
Latest Issues
Current IssueInventing the Future with SEL
Two years after launching its state-of-the-art PCB facility, SEL shares lessons in vision, execution, and innovation, plus insights from industry icons and technology leaders shaping the future of PCB fabrication.
Sales: From Pitch to PO
From the first cold call to finally receiving that first purchase order, the July PCB007 Magazine breaks down some critical parts of the sales stack. To up your sales game, read on!
The Hole Truth: Via Integrity in an HDI World
From the drilled hole to registration across multiple sequential lamination cycles, to the quality of your copper plating, via reliability in an HDI world is becoming an ever-greater challenge. This month we look at “The Hole Truth,” from creating the “perfect” via to how you can assure via quality and reliability, the first time, every time.
- Articles
- Columns
- Links
- Media kit
||| MENU - pcb007 Magazine
Estimated reading time: 3 minutes
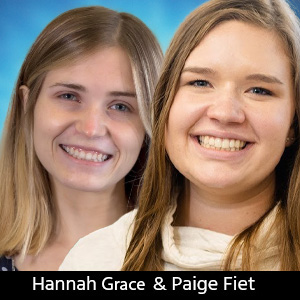
The New Chapter: A Mini Manufacturing Ecosystem
A manufacturing facility is set up like a miniature business ecosystem. Within it, a product is handed from one department to another, with more features and materials added in each step in the process. Most of the time, one process will greatly affect those that follow it. For example, targets created at an imaging step will verify proper registration in a drill step. Sometimes the effect can be negative, such as when too much warp in a panel at the lamination stages creates downstream issues for imaging.
Unfortunately, even processes within a department can cause headaches for subsequent processes. A thicker layer of solder mask on a panel may require a longer tack dry and exposure time. An imaging defect in resist can cause troubles in etching, and the list goes on. But there are remedies. For instance, creating a culture where the next department is viewed as “the customer” can help achieve desired quality standards in all departments.
The first step in developing this type of culture is to open lines of communication. How does one department know the targets of other departments in the process if they never see what they do? Creating and maintaining an open dialogue that helps solve issues can allow, for example, each area of the manufacturing floor to get the tools they need to properly perform the job. Holding meetings with those who make up an entire department provides time to discuss areas of mutual concern so both sides can understand the impact of their actions. They are a time to brainstorm a plan of action.
Promoting a team environment leads to better communication. Each department should feel part of a team working toward a common goal for the entire facility, which should reduce competition across departments. (If there is competition, it should be within departments to continuously improve the quality of their own work.) Giving out small awards, like a gift card from a local business or a team T-shirt, increases team morale, promotes a stronger work culture, and achieves long-term goals. Teams should also participate in activities outside their day-to-day work activities, such as movie days, golf tournaments, and pizza parties. This helps build personal relationships, trust among teams, and better communication among colleagues.
Another important step is to establish cross-training among multiple departments. For many, it’s helpful to talk about how a bent corner on a panel can cause an inkjet machine to flag an error for the wrong thickness, but few will understand it completely unless they see it done. If there’s not enough time to fully cross-train an operator, then departmental trainings and presentations are the next best thing.
Site tours are a way to quickly show processes, too. Once an employee has spent a few months learning the business, a tour can show them the critical role their process plays. The tribal knowledge that is learned from working in other areas of the manufacturing facility is priceless for everyone. It only takes a couple of people to understand all the steps in the process for a department to benefit and learn as a team.
The best way to maintain cross-training, communication, and team spirit is to have a unified leadership team. The operations and engineering teams should meet with all areas of the department to assist with this. Good leaders encourage all operators within a department (across areas and shifts) to learn about other processes in their area and to discuss opportunities for improvement. Leaders set the tone for everyone to feel part of the group—one unit working together toward a common goal.
A company culture that invites all manufacturing areas to improve their processes is a winning strategy for everyone. It starts at the top, with leaders who assist both individual departments and the entire facility in achieving long-term goals. Well-trained operators know what is required of their products before they leave their area and go on to the next department. In a sense, they act as the supplier serving its customer, and thus are important to the success of the business. Internal customers can be equally important.
This column originally appeared in the May 2023 issue of PCB007 Magazine.
More Columns from The New Chapter
The New Chapter: The Benefits of Continuing EducationThe New Chapter: Navigating Maternity Leave in the Electronics Industry
The New Chapter: The Impact of Parasitics on PCB Design
The New Chapter: I’ve Found My ‘Why’
The New Chapter: Artificial Intelligence in PCB Design
The New Chapter: Lessons From the Best Engineer I’ve Ever Known
The New Chapter: Attracting ‘Generation Green’
The New Chapter: Dip Your Hand in the IPC APEX EXPO Candy Jar