Challenges of DFM Analysis for Flex and Rigid-Flex Design, Part 3
June 14, 2023 | Mark Gallant, DownStream TechnologiesEstimated reading time: 2 minutes
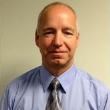
(Editor’s note: This is the final installment of a three-part series. To read Part 2, click here.)
What a True Rigid-flex DFM Analysis Solution Must Include
DFM analysis tools for the last several decades have focused on a typical rigid PCB or some variant. While many standard DFM constraints are applicable, flex has many unique requirements that cannot be addressed with typical DFM analysis. Flex and rigid-flex DFM must be targeted toward the unique materials and processes used to produce flex and rigid-flex designs.
One such example is board outline vs. layer profile. Some CAD systems do not support boundaries on a per layer basis. For most rigid-flex designs, all that is provided is a cumulative board outline that is the extent of all layer shapes. Without a defined boundary per layer, there may be no prevention of routing traces or placing components outside, or off of, a layer in the CAD system. The CAD DRC may also miss these items because they are within the boundary of the cumulative board outline. Having a DFM tool capable of analyzing each layer against its unique profile can detect when conductors are outside, or off of, their respective layers.
Here is a categorized list of the types of analyses and features a flex or rigid-flex DFM tool should have.
1. Trace fracture
Trace or copper fracture in bend areas. Some examples include presence of trace corners, width transitions, or traces non-perpendicular to the bend axis in a bend area. Also, I-beaming where traces are coincident on adjacent flexible layers.
2. Delamination
Pads or vias in bend areas with improper pad shapes or coverlay exposures. When it is required to have vias or other pads in bend areas, special care must be taken when designing the coverlay to reduce delamination potential. Often in these conditions, the coverlay overlaps the pad area to prevent delamination. In other designs, pads are adorned with tabs to extend under the coverlay.
3. Tearing
The absence of tear stops on slits or inside corners. Copper segments, arcs, circles, or other shapes are added to prevent tear around slits or inside corners.
4. Squeeze out
Epoxy leakage onto adjacent copper or other layer surfaces. In order to prevent epoxy squeeze out, a perimeter air gap or fence must be present around adjacent layer content. For example, a larger annular ring may be required on the epoxy layer than its corresponding coverlay annular ring. This prevents epoxy from squeezing out onto adjacent copper or traces.
5. Button plating
Absence of exposures in coverlay for vias. The most common method of plating vias in a bend area is button plating. This requires vias to be plated have an exposure on their adjacent coverlay. Absence of an exposure on the coverlay would prevent plating.
To read this entire article, which appeared in the June 2023 issue of Design007 Magazine, click here.
Testimonial
"We’re proud to call I-Connect007 a trusted partner. Their innovative approach and industry insight made our podcast collaboration a success by connecting us with the right audience and delivering real results."
Julia McCaffrey - NCAB GroupSuggested Items
50% Copper Tariffs, 100% Chip Uncertainty, and a Truce
08/19/2025 | Andy Shaughnessy, I-Connect007If you’re like me, tariffs were not on your radar screen until a few months ago, but now political rhetoric has turned to presidential action. Tariffs are front-page news with major developments coming directly from the Oval Office. These are not typical times. President Donald Trump campaigned on tariff reform, and he’s now busy revamping America’s tariff policy.
Global PCB Connections: Understanding the General Fabrication Process—A Designer’s Hidden Advantage
08/14/2025 | Markus Voeltz -- Column: Global PCB ConnectionsDesigners don’t need to become fabricators, but understanding the basics of PCB fabrication can save you time, money, and frustration. The more you understand what’s happening on the shop floor, the better you’ll be able to prevent downstream issues. As you move into more advanced designs like HDI, flex circuits, stacked vias, and embedded components, this foundational knowledge becomes even more critical. Remember: the fabricator is your partner.
MKS’ Atotech to Participate in IPCA Electronics Expo 2025
08/11/2025 | AtotechMKS Inc., a global provider of enabling technologies that transform our world, announced that its strategic brands ESI® (laser systems) and Atotech® (process chemicals, equipment, software, and services) will showcase their latest range of leading manufacturing solutions for printed circuit board (PCB) and package substrate manufacturing at the upcoming 17th IPCA Show to be held at Pragati Maidan, New Delhi from August 21-23, 2025.
MKS Showcases Next-generation PCB Manufacturing Solutions at the Thailand Electronics Circuit Asia 2025
08/06/2025 | MKS Instruments, Inc.MKS Inc, a global provider of enabling technologies that transform our world, today announced its participation in Thailand Electronics Circuit Asia 2025 (THECA 2025), taking place August 20–22 at BITEC in Bangkok.
Point2 Technology, Foxconn Interconnect Technology Partner to Revolutionize AI Cluster Scalability with Terabit-Speed Interconnect
08/06/2025 | BUSINESS WIREPoint2 Technology, a leading provider of ultra-low-power, low-latency mixed-signal SoC solutions for multi-terabit interconnect, and Foxconn Interconnect Technology (FIT), a global leader in precision interconnect solutions, have signed a Memorandum of Understanding (MOU) to accelerate the commercialization of next-generation Active RF Cable (ARC) and Near Pluggable e-Tube (NPE) solutions.