-
- News
- Books
Featured Books
- pcb007 Magazine
Latest Issues
Current IssueThe Hole Truth: Via Integrity in an HDI World
From the drilled hole to registration across multiple sequential lamination cycles, to the quality of your copper plating, via reliability in an HDI world is becoming an ever-greater challenge. This month we look at “The Hole Truth,” from creating the “perfect” via to how you can assure via quality and reliability, the first time, every time.
In Pursuit of Perfection: Defect Reduction
For bare PCB board fabrication, defect reduction is a critical aspect of a company's bottom line profitability. In this issue, we examine how imaging, etching, and plating processes can provide information and insight into reducing defects and increasing yields.
Voices of the Industry
We take the pulse of the PCB industry by sharing insights from leading fabricators and suppliers in this month's issue. We've gathered their thoughts on the new U.S. administration, spending, the war in Ukraine, and their most pressing needs. It’s an eye-opening and enlightening look behind the curtain.
- Articles
- Columns
- Links
- Media kit
||| MENU - pcb007 Magazine
Estimated reading time: 12 minutes
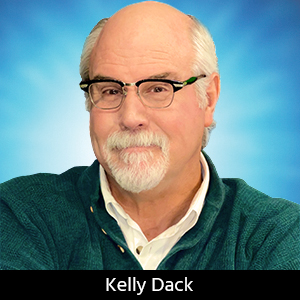
Contact Columnist Form
Target Condition: Keeping Your Design on the Road
Is CAD data output enough to move your design through to global manufacturing success? Form, fit, and function are often referred to in the context of part interchangeability. How well will parts fit together with other parts after rolling off a manufacturing production line? Without key specification limits for these physical performance requirements, a PCB design is destined for quotation delays, no-bids, or outright manufacturing rejection. These can kill time-to-market product development goals.
CAD Data is Absolute
If you have ever opened a CAM file generated from your CAD layout tool, you have seen hundreds of numeric values, each representing a geometric data point in the design. Some of these values specify where the center of a trace is to be located after printing, plating, and etching. Some values represent a location for the center of a hole to be drilled or a milling path for a slot or board edge. Some of the data tells a machine how fast to spin and where to rotate or move to perform the work. All CAD layout tools output absolute data, and those points nominally represent the exact, theoretical position—the target condition—of a geometric feature.
CAD Data Doesn’t Account for Manufacturing Process Tolerance
Manufacturing tools, machinery, and materials introduce a vast, complex set of subjective variables for which the manufacturer must adjust to match the manufactured part feature to the absolute dimensional design data points. But since perfection in manufacturing is nearly impossible to achieve, the challenge for the manufacturer is to know how far a processed feature can stray from perfection and still be form, fit, and functionally acceptable. For example, in a PCB outline, the absolute CAD data may reflect a horizontal (X direction) value of 6.00937". But there is not a machine, material, or process in our universe which can form a glass-epoxy laminate board to such a degree of accuracy. When a PCB designer’s data shows a coordinate of 6.00937" and a run of parts are cut measuring 6.006”, 6.012”, 6.013” and 6.014”, must they all be scrapped? Who says, and by what criteria? Manufacturing stakeholders must be given a range of dimensional acceptability because the yield of their processes vary.
Setting Your DRC Within Legal Limits
Drive down a country road and you’re bound to see a speed limit sign. How do you process this and adjust your driving speed? Whatever your process, you are considering a driving constraint and making the first attempt to hit the target condition for a rate of speed. If the posted limit is 60 mph, most drivers will adjust their car’s rate of speed right up to the limit. Why? Is it human nature to set things right to the edge? Do we think—erroneously—that by setting a complex system to a particular value the result will be exactly 60 mph? It will not. “Exact” is subjective to the context within which the subject must inter-relate with other parts of the system. This is especially true when it comes to the complex systems applied in volume production.
The manufacturing system which produced the car’s speedometer and cruise control module is subject to a “stackup” of manufacturing process tolerances. As the modules are assembled, they must be calibrated for accuracy due to the differing manufacturing variations. To compound the challenge of system accuracy, these modules are then installed into automobile systems which have another set of system variables the manufacturer cannot foresee. The variables of heavy, off-road tire diameter, road grades, and differing temperatures will challenge a cruise control system’s ability to achieve any kind of consistent perfection. According to the NPR program “Car Talk,” cruise control systems can vary from the set value by a factor of ±10%. So, even if you set the cruise control at 60 mph, the variables in play could send the car whizzing by a county sheriff at 66 mph. You may soon be having a discussion with the local gendarme about accounting for tolerance when setting the cruise control. Should we all set our cruise controls to 54.5 mph to allow for a system tolerance of ±10%?
DRC Settings Must Allow for Manufacturing System Tolerances
Generally speaking, PCB designers manually adjust their CAD tool’s DRC settings like a driver sets a car’s cruise control. Many inexperienced designers set DRC values to the “reduced manufacturability” Class 3 limits supplied by local prototype suppliers. If a hot-shot prototype supplier can provide .003” finished traces and spaces, designers are somehow inclined to set the DRC for .003” traces and spaces. If the proto shop says they can produce within an impedance tolerance of ±2%, many times we find that same strict value stuck in the fabrication notes even though a more lenient value would perform sufficiently.
Some designers think that a proto supplier’s CNC drilling equipment is so accurate that annular ring sizing can be drastically reduced without concerns for breakout conditions. They fail to understand that drilling tolerances are only part of the system PCB manufacturing operation and attributes which must come together in order to perform a concentric plated through-hole. There are also printing, etching, and plating variables. There are even material stretching, expansion and contraction factors which the supplier must allow room for. In the often-misunderstood world of PCB prototyping, an amazing feat of fabrication success is deliverable, even when the design layout is red-lining on the upper limits of prototype supplier capabilities.
But what many PCB designers do not understand is that in order to furnish the extraordinary, “impossible” design capabilities mentioned in their advertising, the proto shop will have to build ridiculous amounts of extra parts to yield enough to deliver the small order. Now, it may be easier for some to realize why they are being charged $500 each for that quick-turn run of 10 tiny PCBs: $4,500 of the order went to pay for time and materials for the other 100 parts on the manufacturing panel which did not meet spec and had to be scrapped. The cost was high because the yield was so low.
In fact, for a few years now, CAD tool companies have picked up on this trend and have been working with PCB manufacturing companies to capture their capabilities—their speed limits, so to speak—in hopes of PCB shops developing automated design “cruise controls” for layout in the same fashion as towns, counties and states post their speed limits.
The outcomes of these endeavors have been hopeful at best. They have been able to publish some design constraints and even automatically provide a quote after running a quick, automated DFM review based upon their own unique manufacturing constraints. “Just set it and forget it” is the DRC concept being sold here. This business strategy makes a lot of sense to quick-turn prototype suppliers and CAD tool companies. They are trying to solve the problem of their tools being used to create unmanufacturable PCBs.
But guiding next-generation PCB designers to use rules uniquely achievable only by these isolated resource service arrangements seems to miss the point when a design must eventually scale to production. The real world of volume manufacturing requires more relaxed DRC settings for volume, cost constraints, and design material allowances. If our volume manufacturing stakeholders had a nickel every time they heard a customer complain, “Well, the prototype shop could do it,” they could all retire. Unfortunately, by way of our onshore, custom prototyping capabilities, many PCB designers are groomed to expect their offshore stakeholders to machine to exact numeric values and meet exact material and stackup recipes.
How Tolerant is Your PCB Design Layout?
Have you ever been to traffic school? Years ago, I sat in a room with other offenders listening to rules about driving that I thought I already knew. It all seemed quite boring until we got to the slideshow of actual images of accident scenes. These images depicted the potential cost of operating a vehicle system outside of the acceptable limits.
Similarly, PCB designers cause accidents caused every day by operating their layout tools on cruise control. PCB designers are being given the “keys” to PCB layout tools with default settings they do not understand, producing data output to be supplied to PCB manufacturing stakeholders whose capabilities are off their map. Fabrication and assembly stakeholders see the real-world cost of operating outside your EDA tool’s limits in the form of shorted connections, hole breakout, non-wetted leads, poor solder fillets, and tombstoned components. You can see some of these non-conforming images for yourself in the PCB acceptability standards IPC-A-600 and IPC-A-610.
The current buzz about using artificial intelligence for PCB layout could compound the issue of PCB designers not understanding global limitations, and could drive the PCB layout process autonomously. From what I gather, these visionaries do not appear to be partnering with global manufacturing supplier constraints in mind. Some are partnering with costly, smaller scale, onshore fabrication and assembly services which specialize in prototype quantities. We in volume production often hear from our customer’s project management team leaders who want to scale their assemblies without loosening design constraints: “Well, our proto shop never complained. Why are your suppliers seeing issues now?”
‘Traffic School’ for PCB Design Engineers
Have you ever attended a traditional drafting school? Surprisingly, it is possible to earn a four-year electronics engineering degree without ever taking a design drafting course. Our brilliant EEs, young and old, seem to know everything about “design automation,” electromagnetic fields, physics, and how to make electrons flow. But expecting them to pick up a CAD tool and create a manufacturable PCB design is like giving an inexperienced driver the keys to an autonomous vehicle not set up for busy traffic. Without any training, they are led to believe the intuitive settings will finish the job with little understanding of what’s really required behind the scenes.
A meaningful, thorough understanding of manufacturing tolerance specification is required to create a successful PCB design. A PCB is a component which must perform by interfacing with hundreds or thousands of other mechanical component part features, all while supporting the electrical requirements of the design. Remember, nothing is perfect; everything has a tolerance. It is the job of the PCB designer to consider cost and performance constraints from all the project stakeholders for the design to achieve success. Yes, we have “intelligent data,” and we are moving toward data for Smart manufacturing. But CAD data output is still absolute and the systems which presently create PCBs are subject to variables which affect performance. The question remains: By how much can performance vary? Limits of variation or tolerance must be calculated and declared if a PCB is going to work within a system.
It is not until we get outside of the data onto the PCB fabrication drawing that we hope to see the acceptance criteria for the feature. When quality assurance inspectors can see a dimension and tolerance callout specified for the edge-to-edge distance on the PCB outline, they know the acceptance criteria. They know the range of allowable form. If the designer has calculated the dimensional range correctly, the part is guaranteed to fit and function with other mating parts in the next assembly.
PCB fabrication and assembly drawings are still the common means to communicate tolerances. There has been much headway in documentation automation. But with next-generation PCB designers entering the industry without training, we are now seeing automatically output PCB drawings missing the very specifications that they are intended to convey.
Long ago, PCB designers learned the foundational aspects of the trade as a branch of a more in-depth design drafting program offered by community colleges. These programs helped teach the language of engineering: documentation concepts (including geometric construction), third-angle projection, ANSI standard drawing practices, and the fundamental aspects of geometric dimensioning and tolerancing (GDT), to name just a few. With very few of these school programs available to teach the documentation process, manufacturing engineers are often left scratching their heads while trying to quote or produce a PCB. CAD tool suppliers have done only half the job by evolving capabilities to perform drafting and documentation.
As in all things, capability without understanding can be as dangerous. The industry continues to see an onslaught of documentation output by new designers who are “running with scissors.” Now, with auto-dimensioning capability, we are seeing dozens of unnecessary dimensions added to parts inappropriately, causing double-dimensioning nightmares. We see auto-generated PCB stackup details embellished with laminate attributes which were clearly not understood by the designer and cannot be produced. Who will finish educating our designers on how to wield these tools?
Global Autonomous Design and Manufacturing Still a Distant Vision
In driving school, we learned that the prima facie speed limit means, “Do not drive faster or slower than conditions permit.” Always safely adjust for the surrounding conditions. Anyone who designs a PCB must be in touch with the prima facie limits of manufacturing specification and tolerance capability. Our industry continues to preach this prima facie concept through DFM. But this concept has become so subjective it is rendered meaningless to our global manufacturers. How can designers incorporate DFM if they don’t know the production supplier or manufacturing capabilities? PCB designers are the last to know where in the world their design may be produced as it scales to volume.
Free DFM reviews by onshore prototyping services read much differently than DFM reviews from China, Ireland, India, or Vietnam. Adjusting a CAD tool’s DRC settings to consider every supplier’s unique manufacturing limitation in hope of achieving DFM is a distinct challenge. It seems global suppliers are unwilling to share their limitations unless you send business to them. So, what are the options?
Top DFM ‘Speeding Tickets’ Issued by Suppliers
- Failure to provide design geometry to meet IPC-6012 manufacturing process and class specification
- Failure to provide tangible dimensions and tolerances defining form, fit acceptance criteria
- Failure to provide IPC-D-356 netlist (ODB++ is not utilized sufficiently offshore)
- Failure to declare copper thickness specification as “base” or “finished”
- Failure to locate an intelligent design origin relevant to the PCB such as a mounting hole
- Failure to allow for generic laminate material substitution
Where can an inexperienced designer learn more? IPC holds PCB design classes, such as those taught by Kris Moyer, as well as the CID and CID+ certification classes and exams. A variety of design classes are available at IPC APEX EXPO, DesignCon, and the PCB East and West shows. Altium’s John Watson also teaches basic and advanced PCB design at Palomar College near San Diego. There are great design classes out there, and some that are not so great, so investigate the instructor’s bona fides before forking over your benjamins.
IPC specifications and training courses have already laid the foundation—the prima facie—for collaborative PCB design and manufacturing specifications. They serve the global industry as a type of owner’s manual for our industry systems. They are produced and represented by diverse groups of industry professionals who are subject matter experts in the PCB industry. Manufacturers aim toward these specifications to define the target conditions of our PCBs. PCB designers need to become familiar, specify, and form their design strategies around the limits published in these documents in order to fit and function with fellow supply chain stakeholders. Designers must realize that when they create a layout without consideration for global prima facie production capabilities, they are not creating a design. They are creating an accident waiting to happen.
Now y’all have a good day and just don’t drive so fast, ya hear?
This column originally appeared in the June 2023 issue of Design007 Magazine.
More Columns from Target Condition
Target Condition: From Dream House to Drill FilesTarget Condition: Designing vs. Inventing
Target Condition: ‘Boomer to Zoomer: Do You Copy?’
Target Condition: Advanced Packaging Technologies—Look Before You Leap
Target Condition: My Anti-venom to PCB Cost Adders
Target Condition: Taking the Stand at Your Own Design Review
Target Condition: Designing Unconventional Geometries
Target Condition: What the Heck? A PCB Tech Spec Check