-
- News
- Books
Featured Books
- pcb007 Magazine
Latest Issues
Current IssueInventing the Future with SEL
Two years after launching its state-of-the-art PCB facility, SEL shares lessons in vision, execution, and innovation, plus insights from industry icons and technology leaders shaping the future of PCB fabrication.
Sales: From Pitch to PO
From the first cold call to finally receiving that first purchase order, the July PCB007 Magazine breaks down some critical parts of the sales stack. To up your sales game, read on!
The Hole Truth: Via Integrity in an HDI World
From the drilled hole to registration across multiple sequential lamination cycles, to the quality of your copper plating, via reliability in an HDI world is becoming an ever-greater challenge. This month we look at “The Hole Truth,” from creating the “perfect” via to how you can assure via quality and reliability, the first time, every time.
- Articles
- Columns
- Links
- Media kit
||| MENU - pcb007 Magazine
Estimated reading time: 4 minutes
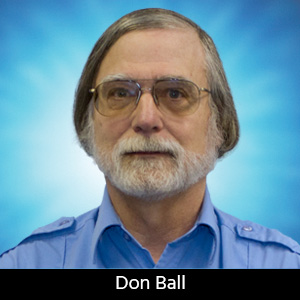
The Chemical Connection: Solutions for Better Etch Uniformity
In my very first column, “Etch Uniformity and The Puddle Problem,” I wrote about a phenomenon in the PCB etching process called the “puddle effect,” which causes large PCB panels to have varying etch quality across the board, typically on the top side. This variation exists because as you are spraying etchant onto the top of a panel, you begin to accumulate spent etchant. It creates a layer that inhibits the fresh etchant from reaching the board’s copper surface that needs to be etched.
With this problem, often the edges of panels will have the fastest etching while the middle has the slowest. This is because the flow of etchant as it accumulates onto the top of the panel will to run out to the sides and fall through. Hypothetically, if someone were trying to etch large PCBs or a sheet of multiple PCBs on a single stock panel, they could place through-holes around the panel. If holes could be created through the middle parts of the panel, to provide another area for the etchant to escape, then the puddle effect would be significantly reduced. Of course, in most cases, this is not realistic for PCB manufacturers. Since the solution is not so straightforward, manufacturers often must depend on wet processing technology that focuses on obtaining better etch uniformity. Here are some of today’s technologies to approach the puddle effect.
Optimized Spray
Optimized spray is not necessarily an anti-puddling measure on its own, however it is still a technology implemented inside etching machines to provide better uniformity. Optimized spray describes an attribute inside the main etch chamber. Functionally, it means that the spray tube pressures are calibrated and adjusted with the expectation that etching will vary across the panel. In practice, this means that spray tubes located over the edges of your panels must be adjusted to provide a less aggressive etch in comparison to the middle spray tubes. Optimized spray is highly important for all matters of etch uniformity. Without good baseline spraying, using any additional counter-puddling technology will just make the process more complicated and may even exacerbate variations.
Etch Adjust
Etch adjust is a process that can be used to counteract the puddle effect. This process focuses on side-to-side uniformity of panels. Side-to-side uniformity refers to the edges of a panel that are parallel to the conveyor side rails. Etch adjust functions in a similar way to optimized spray in that it allows you to make spray zones and provide them with a spray pressure that would reduce any variation caused by the puddle effect. The etch adjust module differs because it’s a unit of operation separate from the main etching chamber. It can target more refined spray zones and thus give you greater control over the side-to-side variations. This type of process can be useful if you copper plate your own panels. Depending on how your plating process operates, the stock material for your PCBs can have thicker copper on one end. With etch adjust, you can more easily compensate for this variation than you could with optimized spray alone.
Intermittent Spray
Intermittent spray is a counter-puddling measure that you can take if you want to improve the etch uniformity of your PCBs from the leading-to-trailing edges. This refers to the edge perpendicular to the direction of travel. The leading edge enters the horizontal etching machine first, while the trailing edge enters last. Variation on this part of the panel is the most difficult to control because of how the panel gets pulled through the etching machine. When you adjust for side-to-side variations, the solution mostly likely is having higher spray pressures in the middle than on the edges. These can continuously spray and target the areas you want to change.
With leading-to-trailing uniformity, you cannot simply have a continuous spray and improve uniformity (at least not with today’s technology). To achieve leading-to-trailing uniformity, etching must start and stop only in the middle; this is effectively what intermittent spray does. To improve leading-to-trailing uniformity, intermittent spray uses a sensor to indicate where the first edge of a panel is located in an etching machine. Once the panel is partially through the module, intermittent spray initiates and targets a spray of etchant only in the middle of the panel, shutting off before reaching the trailing edge. By doing this, you gain greater control over the middle sections that tend to be under-etched.
Conclusion
There are many different tools available to approach etch uniformity. The few that were shared in this column only touch on a handful of options that are available to you. With this information, you should now be aware of some of the etch uniformity technology that exists today and what exactly each option does.
This column originally appeared in the June 2023 issue of PCB007 Magazine.
More Columns from The Chemical Connection
The Chemical Connection: Sales Organization from a Capital Equipment PerspectiveThe Chemical Connection: Through-glass Vias in Glass Substrates
The Chemical Connection: Reducing Defects in Circuit Board Production
The Chemical Connection: Common Misconceptions in Wet Processing
The Chemical Connection: Surface Finishes for PCBs
The Chemical Connection: Earthquakes, Astronauts, and Aquatics—A Lighter Look at the Past
The Chemical Connection: Better Fabs Attract a Better Workforce
The Chemical Connection: Can Changing Spray Nozzles Improve My Etch Quality?