-
- News
- Books
Featured Books
- pcb007 Magazine
Latest Issues
Current IssueInventing the Future with SEL
Two years after launching its state-of-the-art PCB facility, SEL shares lessons in vision, execution, and innovation, plus insights from industry icons and technology leaders shaping the future of PCB fabrication.
Sales: From Pitch to PO
From the first cold call to finally receiving that first purchase order, the July PCB007 Magazine breaks down some critical parts of the sales stack. To up your sales game, read on!
The Hole Truth: Via Integrity in an HDI World
From the drilled hole to registration across multiple sequential lamination cycles, to the quality of your copper plating, via reliability in an HDI world is becoming an ever-greater challenge. This month we look at “The Hole Truth,” from creating the “perfect” via to how you can assure via quality and reliability, the first time, every time.
- Articles
- Columns
- Links
- Media kit
||| MENU - pcb007 Magazine
Estimated reading time: 3 minutes
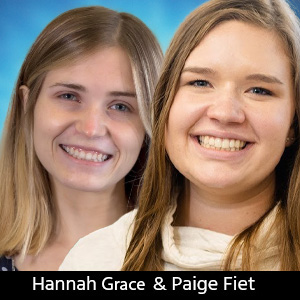
The New Chapter: Four Steps to Developing an Improvement Process
Just the other day, my colleague and I were discussing the daunting process of creating a quality management system from scratch for a company. He said, “Can you imagine starting up your own company and creating the quality management system? How would you know where to start?” We then began a debate on what processes we would create first and where we would store the database and each of the documents. Thinking about this was, for both of us, overwhelming and fascinating at the same time.
As this discussion progressed, my coworker mentioned that he would begin his TQM with common audit concerns. He claimed this was the best place to start as you are satisfying a customer requirement, and it prepares the company for passing audits with flying colors. I agreed this was the best way to start a new quality management system, but what about an existing system that just needs improvement?
As per typical cubicle chatter, this evolved into a larger conversation among those of us in the quality engineering department. One mentioned customer satisfaction as the best place to focus improvements while another had a firm opinion that it should be focused on employee engagement. We weighed the pros and cons of quality management from our previous employers. How did each of these companies store their quality documents? What sorts of documents exist in their quality system? Toward the end of our less than heated debate, we agreed: Several factors must be in place when developing the improvement process of any quality management system, regardless of the workplace.
1. Strong Customer Interaction and Satisfaction
The first accepted pillar in the improvement process is through customer interaction and satisfaction. Once we create the foundation of our quality system, it must be constantly updated through customer feedback. They provide a hard look into what’s lacking in your systems. Sometimes this looks like a process review or an update to an outdated training document. At other times, the customer can steer the direction into technology and material advancements. Whatever the case may be, a business is in business to make money. In most industries, the money is made by selling products. Why not first listen to those buying the products?
2. Consider Company Culture
The next agreement we made was that the quality management system should factor in the culture of the facility or company. Is it easy for all the employees to access documents in the QMS? Are the employees looking to constantly improve the quality systems around them? How are the employees able to communicate any ideas they have for improvement to leadership? How willing are the employees to not only present ideas for advancement but for them to follow through with said ideas? A business won’t survive without employees (unless AI takes over the world, that is). So, a QMS needs to fit into the everyday culture such that it creates continual improvement at all levels of the business.
3. Assigning Responsibility
Our conversation then shifted away from the people side of quality and into the system that prompts it. Organization and communication are needed to maintain the documents needed to continue to shape the quality environment. It’s important to know who is responsible for the upkeep of each document and when to renovate them as they become outdated. These documents should also have buy-in from multiple leaders in the business.
4. Show Me the Data
The final factor we defined is the use of data. Any company can “feel” that their quality system is robust and gets the job done. But at the end of the day, it’s just an opinion. Where are the numbers showing the system is robust? Statistics need to be the driving force, regardless of the continual improvement made. It’s what drives the “M” in SMART goals and shows strengths and weaknesses. Data will drive the initiatives worth focusing on.
At the end of our probably too long conversation, my colleagues and I had mostly agreed that we were happy to be on the improvement side of the quality management system and not at the start. We concluded that it’s incredibly empowering to be a part of a system that is always trying to revise itself, one in which the best advancements of today will be standard practice tomorrow.
This column originally appeared in the July 2023 issue of PCB007 Magazine.
More Columns from The New Chapter
The New Chapter: The Benefits of Continuing EducationThe New Chapter: Navigating Maternity Leave in the Electronics Industry
The New Chapter: The Impact of Parasitics on PCB Design
The New Chapter: I’ve Found My ‘Why’
The New Chapter: Artificial Intelligence in PCB Design
The New Chapter: Lessons From the Best Engineer I’ve Ever Known
The New Chapter: Attracting ‘Generation Green’
The New Chapter: Dip Your Hand in the IPC APEX EXPO Candy Jar