KSG Group Puts Horizontal OSP Line for Organic Surfaces into Operation
July 31, 2023 | KSG GroupEstimated reading time: 1 minute
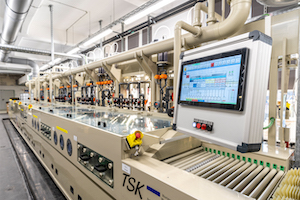
The KSG Group has expanded its capacities in the field of organic surface coating by bringing a new wet-chemical horizontal system online. The OSP line from TSK Schill enables the printed circuit board (PCB) manufacturer to implement a higher production volume and also features optimised processing operations, improved occupational safety and health, and a high degree of user-friendliness.
As an alternative to metallic surface finishes, OSP (organic solderability preservative/organic surface protection) is a favourable and RoHS-compliant variant that produces a flat soldering surface and can be renewed several times without damaging the PCB. The nickel-free coating is also suitable for high-frequency applications and can be combined with electroplated nickel/gold (NiAu) if necessary. The KSG Group can now take full advantage of these and further benefits to obtain not only a higher capacity, but also high-quality results with a uniform layer thickness and a very homogeneous surface: the new OSP line is characterised by improved rinsing and drying technology as well as a constant etching rate of the pretreatment through a feed-and-bleed dosing of the pickle.
Occupational safety and health have also been increased as part of the new acquisition: since the plant has automatic dosing of the chemistry as well as automatic pH monitoring and adjustment by the controller, the plant operator does not need to perform as much manual handling of the chemicals. Intuitive and clearly structured system software as well as a touch PC simplify the operation of the new OSP line, which was reliably installed within the desired project framework by TSK Schill GmbH.
Testimonial
"We’re proud to call I-Connect007 a trusted partner. Their innovative approach and industry insight made our podcast collaboration a success by connecting us with the right audience and delivering real results."
Julia McCaffrey - NCAB GroupSuggested Items
KOKI to Showcase Analytical Services and New HF1200 Solder Paste at SMTA Guadalajara 2025
07/31/2025 | KOKIKOKI, a global leader in advanced soldering materials and process optimization services, will exhibit at the SMTA Guadalajara Expo & Tech Forum, taking place September 17 & 18, 2025 at Expo Guadalajara, Salón Jalisco Halls D & E in Guadalajara, Mexico.
Weller Tools Supports Future Talent with Exclusive Donation to SMTA Michigan Student Soldering Competition
07/23/2025 | Weller ToolsWeller Tools, the industry leader in hand soldering solutions, is proud to announce its support of the upcoming SMTA Michigan Expo & Tech Forum by donating a limited-edition 80th Anniversary Black Soldering Set to the event’s student soldering competition.
Silicon Mountain Contract Services Enhances SMT Capabilities with New HELLER Reflow Oven
07/17/2025 | Silicon Mountain Contract ServicesSilicon Mountain Contract Services, a leading provider of custom electronics manufacturing solutions, is proud to announce a significant upgrade to its SMT production capability with the addition of a HELLER 2043 MK5 10‑zone reflow oven to its Nampa facility.
SHENMAO Strengthens Semiconductor Capabilities with Acquisition of PMTC
07/10/2025 | SHENMAOSHENMAO America, Inc. has announced the acquisition of Profound Material Technology Co., Ltd. (PMTC), a premier Taiwan-based manufacturer of high-performance solder balls for semiconductor packaging.
Hands-On Demos Now Available for Apollo Seiko’s EF and AF Selective Soldering Lines
06/30/2025 | Apollo SeikoApollo Seiko, a leading innovator in soldering technology, is excited to spotlight its expanded lineup of EF and AF Series Selective Soldering Systems, now available for live demonstrations in its newly dedicated demo room.