-
- News
- Books
Featured Books
- pcb007 Magazine
Latest Issues
Current IssueInventing the Future with SEL
Two years after launching its state-of-the-art PCB facility, SEL shares lessons in vision, execution, and innovation, plus insights from industry icons and technology leaders shaping the future of PCB fabrication.
Sales: From Pitch to PO
From the first cold call to finally receiving that first purchase order, the July PCB007 Magazine breaks down some critical parts of the sales stack. To up your sales game, read on!
The Hole Truth: Via Integrity in an HDI World
From the drilled hole to registration across multiple sequential lamination cycles, to the quality of your copper plating, via reliability in an HDI world is becoming an ever-greater challenge. This month we look at “The Hole Truth,” from creating the “perfect” via to how you can assure via quality and reliability, the first time, every time.
- Articles
- Columns
- Links
- Media kit
||| MENU - pcb007 Magazine
Estimated reading time: 4 minutes
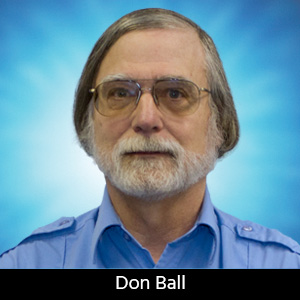
The Chemical Connection: Don’t Just Blame the Etcher
If your HDI or UHDI production process is quality challenged, don’t assume your etcher is to blame. Many factors impact the quality of the final product, so assess broadly, and you may find that “the devil is in the details.”
Generally, the first place most people can get good product specification measurement is at the end of the etching process. It’s natural and easy to blame quality shortcomings on the etcher. By all means, look at your etcher and invest some time trying to improve its performance but don’t stop there. Other factors may be affecting the etch uniformity.
Each process step prior to etching adds variation to the final product. In most cases, the added variation is small, but as the features on the etched panel get smaller and closer together, they become more important.
For example, back in the days when 0.004" (100 µm) lines and spaces were state-of-the-art (yes, I have been around that long), a circuit board manufacturer that had been mostly producing consumer boards requiring lines and spaces of around 0.008" or more took on a job requiring the then state-of-the-art 0.004" lines and spaces. Their yields went from more than 95% on their 0.008" line-and-space product to less than 50% for the 0.004" space product and they lost money on that job. A lot of time and effort was spent on etcher optimization, which improved yields significantly but not to the point of profitability.
In this instance, it was found that a change in procedures in the photoresist exposure step solved their problem. For most of their production panels, the exposure was made as soon as the vacuum gauges indicated full vacuum. For the 0.004" space panels, it was found that by delaying the panel exposure for 30 seconds after full vacuum was drawn, it brought their yields back to the 95% range. The extra time allowed the phototool to come into closer contact with the resist and prevented leakage from their non-collimated light source from causing shorts across the narrower spaces. Ultimately, they upgraded their exposure units to ones with collimated light sources and better and more consistent vacuum drawdowns to meet the specifications of the then high-tech products.
By today’s standards, this is a relatively crude example, but it does show that some attention to other process steps as well as etching can solve some problems involved with high density circuit production.
A more recent example is provided by two companies I assisted with about two years ago. Both companies were making high-density flex circuits using a reel-to-reel process. Company B was consistently outcompeting Company A for business and Company A could not understand why. Both companies were long time customers and familiar with each other, so Company A was aware that Company B had a newer model etcher. They assumed that this was the problem, asked for an audit of their etcher, and for information on the latest advances in etcher technology.
Company A’s etcher had been purchased in the mid-’90s but had been well maintained and optimized for their production. When I ran and analyzed my test panels, I saw that their etcher performance was on par with the etcher in my lab, which was the same model and vintage as Company B’s (circa 2015 or so). I informed the management that I didn’t think a new etcher would improve their competitive outlook. This advice was not well received. If not the etcher, what else could it be?
The difference was that when Company B decided to get into HDI production (UHDI was still in the future), they took the time to study each process step in the production line, from incoming materials to outgoing packaging, and looked at how to optimize each step. In the etching process, they looked in detail at surface prep, types of photoresists, resist application, phototools, resist exposure, developing, and etching.
By “in detail,” I mean they analyzed such things as roller temperature for dry film lamination, exposure times and intensities, developer concentrations, etc., to find the most efficient and cost-effective ways to accomplish their goals for high density interconnects. The research took two to three years to complete but, in the end, they were positioned to succeed in a highly competitive market.
Some equipment upgrades were required but, for the most part, all that was needed was to tighten operating procedures and find the best operating parameters for each process. As far as I know, Company A is still looking for that silver bullet in terms of new etcher technology that will make them more competitive.
The moral of the story: As circuit features shrink and are squeezed into smaller and smaller spaces, one should focus on optimizing every step in the circuit formation process and not just one small area where you assume the problems exist.
This column originally appeared in the September 2023 issue of PCB007 Magazine.
More Columns from The Chemical Connection
The Chemical Connection: Sales Organization from a Capital Equipment PerspectiveThe Chemical Connection: Through-glass Vias in Glass Substrates
The Chemical Connection: Reducing Defects in Circuit Board Production
The Chemical Connection: Common Misconceptions in Wet Processing
The Chemical Connection: Surface Finishes for PCBs
The Chemical Connection: Earthquakes, Astronauts, and Aquatics—A Lighter Look at the Past
The Chemical Connection: Better Fabs Attract a Better Workforce
The Chemical Connection: Can Changing Spray Nozzles Improve My Etch Quality?