-
- News
- Books
Featured Books
- pcb007 Magazine
Latest Issues
Current IssueInventing the Future with SEL
Two years after launching its state-of-the-art PCB facility, SEL shares lessons in vision, execution, and innovation, plus insights from industry icons and technology leaders shaping the future of PCB fabrication.
Sales: From Pitch to PO
From the first cold call to finally receiving that first purchase order, the July PCB007 Magazine breaks down some critical parts of the sales stack. To up your sales game, read on!
The Hole Truth: Via Integrity in an HDI World
From the drilled hole to registration across multiple sequential lamination cycles, to the quality of your copper plating, via reliability in an HDI world is becoming an ever-greater challenge. This month we look at “The Hole Truth,” from creating the “perfect” via to how you can assure via quality and reliability, the first time, every time.
- Articles
- Columns
- Links
- Media kit
||| MENU - pcb007 Magazine
Estimated reading time: 4 minutes
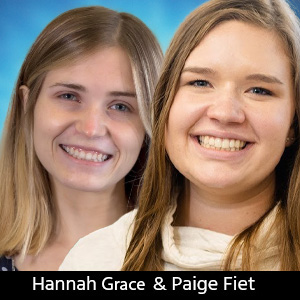
The New Chapter: The Pros and Cons of Tribal Knowledge
Tribal knowledge is important and quite common in the electronics manufacturing industry—for good reason. Many engineers, technicians, and operators have formed their careers around building PCBs. Some even worked alongside the founding fathers of electronics. Newer, young minds stand on the shoulders of this knowledge base. As a process engineer, I work with operators who have been coating panels with solder mask longer than I’ve been alive. Some know the exact coating parameters required for the toughest of designs. To watch them hand-screen panels is like learning the nuances of a family recipe handed down through generations.
What happens when those operators retire? It’s so risky to leave this vital knowledge only in their minds as they leave the industry. Will we be left with 30+ years of knowledge just briefly passed to a new employee who is hoping to avoid similar mistakes that might have been made in those 30 years? Can that information be quantified and written down for the next generation, so young engineers continue to push the envelope further?
Losing this database of experience can be detrimental if not properly passed on during the training process. It may not be intentional and may just be the result of unquantified information required for success. For example, while working recently with a team of engineers on processing guidelines for our front-end engineering (FEE) team, the team asked the lamination engineer about signs that could exist in an unbalanced design to cause severe warpage. The plan was to use these details to create a knowledge database that any engineer could access to create an adequate process flow for a new job. Unfortunately, we were met with the all-too-common response, “I can just tell by looking at the design and stackup.” It took some time and a lot of conversation to begin the process of quantifying information he hadn’t even thought to quantify before.
Once initial information had been collected, it was properly documented in a living document. Inevitably, the FEE team came back with more problems not initially included in the document. This allowed the document to grow with details that were previously forgotten. The most important part of this story is that the information was captured for years to come. Five to 10 years after our lamination engineer is long retired, the new lamination engineer can reference documents that include this pertinent information instead of taking a considerable amount of time to learn it for himself.
Beyond the risk of losing the knowledge curated by experience, tribal knowledge can be dangerous to the productivity of a facility. For example, if plating operators need to ask the engineering team about the current, processing time, or waveforms that should be used on every new job booked, the plating engineer could not get much done outside of setting up new jobs. What would happen if the plating engineer took a two-week vacation with no cell service? Would all the new jobs have to wait until that person returned? A less extreme example might be operators who are able to perform the set-up of most product on a plating line but have not learned the subtleties of waveforms for more complex work. Even for the most experienced operators, the details may be lost in translation. Why take the time to wait for one person to respond to an email if that same information can be readily available to anyone requiring it?
The biggest trouble with tribal knowledge is the effect it can have on company culture. Sometimes, tribal knowledge can lead to an “us vs. them” mentality within a working team. Rather than working together to solve a problem, more knowledgeable individuals may intentionally gatekeep information to maintain their status as “valuable” to the company. This mentality can prevent the team from making headway on problems, especially if newer employees feel they don’t have as much to add. New employees can also feel overwhelmed by the amount of information required to perform their job. Without documentation they can refer to, they may feel embarrassed to ask what an acronym stands for or how to perform an undocumented process step. These feelings are damaging to any company looking to create a team-based culture.
While tribal knowledge is crucial to the success of all companies, it can be equally troubling. To maintain a baseline of information needed to advance, this information should be documented and readily available to the necessary parties. It should also be shared freely as a way to develop a team-based culture. However, to be truly helpful, when tribal knowledge is recorded, it must be accurate and relevant. Information should be shared in a consistent manner and format. It needs to be controlled by a small group of individuals to prevent loss of pertinent information. What information at your facility can be put into a formalized archive for the future generation to learn from?
This column originally appeared in the September 2023 issue of PCB007 Magazine.
More Columns from The New Chapter
The New Chapter: The Benefits of Continuing EducationThe New Chapter: Navigating Maternity Leave in the Electronics Industry
The New Chapter: The Impact of Parasitics on PCB Design
The New Chapter: I’ve Found My ‘Why’
The New Chapter: Artificial Intelligence in PCB Design
The New Chapter: Lessons From the Best Engineer I’ve Ever Known
The New Chapter: Attracting ‘Generation Green’
The New Chapter: Dip Your Hand in the IPC APEX EXPO Candy Jar