Estimated reading time: 19 minutes
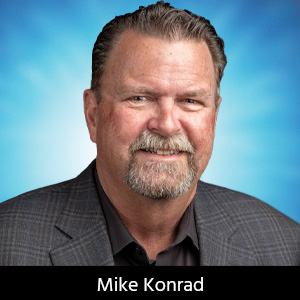
The Knowledge Base: The Role of Automated Inspection Systems
What are some of the common challenges or limitations associated with automatic inspection systems in electronics manufacturing, and how can they be addressed?
D'Amico: The continuing evolution toward advanced miniature packaging has led to ever-increasing PCB density and complexity. This adds an increased number of challenges and limitations for each automated inspection system within the manufacturing process. For instance, smaller discrete devices such as 01005s and 030015s, as well as micro-BGA and CSP devices, require very small solder depositions, and that adds a level of complexity for the SPI process. These smaller devices also require higher resolution optics, lighting, and 3D inspection capability for the AOI machine as well. Furthermore, as PCB density increases, the proximity decreases between taller devices and lower lying discrete components, creating a challenge with shadowing. To overcome this challenge, the AOI machine must be configured with multi-angle 3D projection technology as well as the capability to process taller devices up to 25 mm. Lastly, the increased use of bottom terminated devices increases the requirement for X-ray inspection capability for verification of proper electrical connectivity. The good news is that the technology exists to overcome each of these challenges.
Scutchfield: On the mechanical side, shiny and hidden joints can be challenging, so systems had to be created (special lighting and side camera technology) to overcome these challenges. Beyond that, management and processing of the immense amount of 3D data being generated creates additional challenges. Again, we continue to refine everything involved with doing this, as it continues to be a moving target where more and more data will be generated as we go forward.
Virani: Some common challenges associated with automatic inspection systems include:
- Long programming time for each new board type, which is amplified when components on a board change
- Poor suitability for covering a wide variety of inspection tasks at different stages of manufacturing (e.g., many systems are not suitable for final assembly inspection for inspecting a fully-populated board with components of different sizes, shapes, and height, and different types, such as SMT, through-hole, wires, etc.)
- Highly sensitive to minor acceptable variations resulting in high false positive rates
Could you describe the role of machine vision and image processing algorithms in automatic inspection systems for electronics manufacturing?
D'Amico: Most automated inspection systems use some form of machine vision. As the inspection process becomes more complex, these systems must be configured with high-speed, high-resolution optics, lighting, and 3D technology to capture multiple images of each region of interest for data processing. The most advanced systems use a combination of 2D and 3D algorithms to analyze this data to determine the integrity of each phase of the manufacturing process. For solder deposition, SPI algorithms are used to analyze the area, volume, shape, and offset of each deposition as well as bridging between depositions. AOI systems use a combination of complex algorithms to determine the length, width, height, and coplanarity for both the body and leads of each device, as well as volumetric measurement of every solder joint. X-ray systems offer computed tomography (CT) scanning with specialized algorithms for detailed cross-sectional 3D analysis of a given region of interest at multiple different angles and levels.
Scutchfield: This is probably the most important feature when it comes to capability, accuracy, and repeatability. Image acquisition is the first big step in the inspection process, and it must be done properly for the system to have any chance of providing a reliable, trustworthy result. The success of the inspection effort depends on a combination of the camera, optical resolution, and the number of images acquired, along with pattern creation source (digital, analog, or both). These combinations result in a data set, and size of the data set which needs to be processed and analyzed. In most cases the more data, the better the image clarity and more accurate the results the system can provide. But large data sets take longer to process, especially if many tests are being executed. To be fully capable of meeting both superior image acquisition and fast processing (fact inspection cycle times), systems must employ all features and capabilities, plus both powerful and very optimized algorithms.
Virani: Machine vision and, in particular, machine learning, helps to overcome the limitations of traditional automated inspection systems. By automating the programming step, one can significantly increase productivity, as the system can quickly learn new boards with ease and accommodate variations in board designs and components used. Moreover, machine learning makes defect detection more robust, reducing false positive rates while maintaining high defect detection rates. Additionally, it enables us to inspect objects that were previously only possible with human operators.
What criteria should be considered when selecting an automatic inspection system for a specific electronics manufacturing process?
D'Amico: The criteria considered for selecting any automatic inspection system is really based on the manufacturer’s budgetary and production requirements. We should consider:
- What are the manufacturer’s budgetary requirements?
- Is this an in-line or off-line production application?
- What is the smallest component that is currently used in the manufacturing process? What will this be in the foreseeable future?
- Is there a requirement for multiple bottom terminated devices?
- Is there a requirement for inspection of tall devices up to 25 mm?
- Is there a requirement for wafer-level devices with highly reflective surfaces?
Scutchfield: Considerations can be a bit different depending on the inspection application, but the core features and considerations center around selection of a provider/partner which can serve all current and potential future needs, and to not make the mistake of looking at the system being acquired as a one-time buy. The needs you have today are just that, and chances are good that your needs will expand over time, especially as you learn what multiple inspection points on the line can do for you. Selecting a provider that has a very proven track record with systems that serve all the various inspection functions on the SMT line, and has the strong commitment to developing the software tools to tie all systems together and truly enable Smart factory realization, is what will ensure your business will be taken to the next level. You will have the opportunity to remain state of the art and cutting edge with your SMT operation.
Virani: Criteria to be considered include:
- Type of inspection: Through-hole, final assembly, and cosmetic inspection require unique optics and lighting to properly identify defects.
- Cycle time: How fast does the inspection need to be completed?
- Quality target: What is the level of accuracy required at the stage of production?
- Value (or ROI): Cost of alternative (e.g., human inspector) or prevention of defects.
How do automatic inspection systems handle component and PCB (printed circuit board) variations, such as different shapes, sizes, and colors?
D'Amico: Once again, this really depends on whether the process is in-line or off-line. To process odd-shaped PCBs in-line, the manufacturer would have to use some sort of pallet for transport through each stage of the manufacturing process. Off-line inspection systems are more forgiving in this respect and they typically include a work fixture for processing these odd shapes.
Different PCB colors such as white and red may be problematic for some inspection systems and should be addressed as an upfront requirement. Some 2D and 3D systems simply cannot handle these variations. For instance, 2D bridge inspection may be problematic for white PCBs as this may create false calls. To cope with this issue, the inspection machine must be configured with an advanced lighting system. The same is true for 3D laser inspection systems that will be more susceptible to PCB color variation than a 3D moiré system due to absorption and reflectivity of the laser light. Once again, it is imperative to address these requirements as part of the equipment evaluation process.
Scutchfield: The key here is to use a core technology and subsystems (under the hood) that are immune to color variations and can handle a wide range of component sizes and heights. Some technologies are more suitable than others when it comes to this (back to the moiré vs. laser conversation), and the number and types of acquisition methods (analog/digital, etc.) being used.
Virani: Typical automatic inspection systems require manual re-programming to handle such variations, which is a very time-consuming and tedious trial-and-error process. As mentioned previously, machine learning/AI systems can automate this process and be robust/adapt to different shapes, sizes, colors, etc.
Can you discuss the integration of automatic inspection systems with other manufacturing processes and quality control measures?
D'Amico: Industry 4.0 is a topic of much discussion within the electronics manufacturing industry. In the most simplistic of terms, Industry 4.0 is a trend toward automation and data exchange within the manufacturing process. This basically requires connectivity and communication from machine-to-machine within the manufacturing line. The challenge is to collect data from each of the systems within the line and make that data available to the rest of the machines. Without test and inspection, there is no Industry 4.0. The whole purpose of test and inspection is to collect actionable data that may be used to reduce defects and maximize efficiency within the manufacturing line. The goal is to minimize scrap and get a really good handle on those process parameters that need to be put in place to manufacture products the right way the first time. For maximum efficiency, three inspection systems are required within the production line. These are solder paste inspection (SPI) post-solder deposition, automated optical inspection (AOI) post-placement, and AOI post-reflow. This requires a substantial investment, however, the combination of all three inspection machines is really the only true way to provide feedback for each stage of the manufacturing process.
Scutchfield: There is a lot of work going on to create real time communication and connectivity between inspection tools and the systems that are most likely to create defects, to allow for real time auto-adjustment, which can potentially eliminate those defects from being created. This is being done through both CFX communication protocol and the use of AI tools for both the screen printing and pick-and-place processes. This is now a daily reality and will continue to expand and grow in capability as time goes on.
Virani: With the digitization of inspection records and data, there is a promising opportunity to integrate it with other data sets. One of the most frequent demands we receive from our customers is to integrate inspection data with MES data. By integrating detailed quality data and supporting metadata (information about inspection, and production), it’s possible to gain insights into drivers of yield and potential improvements.
What are some recent advancements or trends in automatic inspection systems for electronics manufacturing, and how are they impacting the industry?
D'Amico: The widespread adoption of artificial intelligence (AI) is perhaps the most prolific current trend in automated inspection. In today's electronics manufacturing industry, standards for defect and quality control are stricter than ever due to advancements of electronic products and increasing safety and environmental regulations. Electronics manufacturers are forced to maximize their production efficiency by implementing Lean manufacturing initiatives and optimizing production processes. Manufacturers are relying upon AOI equipment to streamline the manufacturing process and provide real time root cause analysis of manufacturing defects. The objective is to increase profitability by improving production yields and reducing costly rework. In recent years, 3D AOI machines have developed rapidly, and many new functions have been added. While these performance improvements are welcome, they have added another level of complexity to the programming and optimization of the inspection system. 3D AOI machines require much more parameter manipulation for teaching and debugging, resulting in increased dependency on the skill of the process engineer.
This presents a host of new challenges. If a skilled employee is replaced or a new employee is introduced due to the addition of more SMT lines, productivity may be adversely affected until the skill level of the employee is improved. Such uncertainty and instability are something that electronics manufacturers must avoid to maintain quality control. This is where the need for AI is highlighted. In short, the goal of using AI is to reduce the level of operator proficiency required to maintain the highest levels of manufacturing quality and efficiency.
Scutchfield: Everything right now is revolving around Smart factory realization, where the data is applied real time to improve processes and drive toward “self-healing” initiatives. Through this, PCB assemblers are becoming less reliant on human need and intervention, and improving their yields (less rework), all of which adds up to reducing their costs. Beyond that, backend inspection is gaining a lot of traction, where we can now apply frontend concepts and technology to backend/box and module build applications. This will continue to grow significantly over the next few years.
Virani: Some advancements and trends include:
- Foundation AI models: These are pre-trained AI models tailored to specific types of products and defects. Traditionally, manufacturers had to build in-house AI and automation teams to build AI systems for different tasks, which can take years to become production ready. Choosing an automated inspection company which has foundation models specifically for PCBA/electronics defects will reduce time-to-production for automated inspection from years to weeks.
- Digitization: Multiple systems (IoT, imaging systems, MES) now allow manufacturers to collect large-scale metadata. Manufacturers can use this data, including product quality data gathered from inspection systems, to identify production issues, optimize product design for efficient manufacturing, and facilitate customer-facing teams to address product defects in the field.
These advancements help electronics manufacturers reduce waste and improve quality, ultimately making them more profitable and competitive.
This column originally appeared in the October 2023 issue of SMT007 Magazine.
Page 2 of 2More Columns from The Knowledge Base
The Knowledge Base: The Pivotal Role of Solder PasteThe Knowledge Base: Enhancing Customer Loyalty and Product Quality
The Knowledge Base: The Value of Industry Certifications
The Knowledge Base: The Difference Between Critical and Distracting Decision-making
The Knowledge Base: The Transformative Role of AI and ML
The Knowledge Base: A CM’s Perspective on Box Build Practices
The Knowledge Base: Mastering Trade Show Success for Exhibitors
The Knowledge Base: The Evolution of Conscious Marketing