Alex Stepinski on High-reliability Fabrication
October 23, 2023 | I-Connect007 Editorial TeamEstimated reading time: 1 minute
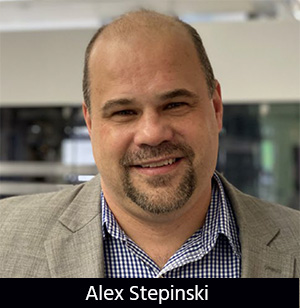
Alex Stepinski, principal and president of Stepinski Inc., and principal of Smart Process Design, has designed leading-edge PCB facilities and introduced a variety of novel systems and technologies into PCB manufacturing. We asked Alex to share his thoughts on high-reliability fabrication techniques, where manufacturers go wrong, and what fabricators need to do to step up their reliability game.
Barry Matties: Where does high reliability intersect with bare board fabrication and what should readers be thinking about?
Alex Stepinski: It’s about service life. That's what the clients want. They want high reliability so it doesn't fail in the field, and when it does, it's very far away in time. You must do accelerated testing to confirm that your product will be reliable for “X amount” of time, and that it also de-risked from white rhino/black swan events and T0/latent fails.
I would break down high reliability management into two influential categories: process design and product design. During the product design, what do they control? Fabricators control KPIs to get high reliability. They should have a model, or a set of rules based upon prior history, as to what works and what doesn't work. They should also have these rules correlated to qualification methods, because one OEM might use IST, another uses a different type with different conditions, and so on.
Reliability is a subset of the test conditions, and the higher the reliability, the higher the potential product value/willingness to pay, so fabs must make sure that they correlate their testing results to their product design attributes. But that precise regression is missing in a lot of cases, and there's a lot of diversity of test/qual methods. The big question is: What are the defects and/or parametric conditions that lead to reliability failure and can they be normalized? Today, many people are talking about HDI failures. Stacking microvias has been a common topic lately.
To read this entire conversation, which appeared in the October 2023 issue of PCB007 Magazine, click here.
Suggested Items
Real Time with… IPC APEX EXPO 2024: Magnalytix's Services and Trends in the Electronics Industry
05/10/2024 | Real Time with...IPC APEX EXPOMike Bixenman, president of Magnalytix, explains Magnalytix's services, including third-party validation, test boards, electrical testing, and comprehensive reports. He also discusses emerging trends such as power electronics and reliability. Standards and design improvements also form part of this conversation.
Real Time with… IPC APEX EXPO 2024: The Driving World of e-Mobility with Indium
05/08/2024 | Real Time with...IPC APEX EXPOIn the competitive EV market, technology plays a crucial role facing the challenges of infrastructure. As Brian O'Leary explains, Indium's e-Mobility product suite includes proven solder and thermal management products for high reliability.
Seeking Employment: Palash Pranav Vyas
05/03/2024 | Barry Matties, I-Connect007Despite skilled worker shortages across the industry, there are many educated and qualified individuals ready to contribute to electronics manufacturing. Here we profile Palash Pranav Vyas, a Ph.D. candidate at Auburn University whose work in drop shock reliability won him Best Student Poster at IPC APEX EXPO 2024.
Real Time with... IPC APEX EXPO 2024: Adhesive Materials and Equipment Update with Dymax
05/01/2024 | Real Time with...IPC APEX EXPOVirginia Hogan, global business development manager at Dymax, discusses adhesive materials, dispensing and curing equipment, a new, high-reliability conformal coating, and various materials and dispensing methods.
Empowering Electronics Assembly: Introducing ALPHA Innolot MXE Alloy
04/16/2024 | MacDermid Alpha Electronics SolutionsIn the rapidly evolving electronics industry, where innovation drives progress, MacDermid Alpha Electronics Solutions is committed to setting a new standard. Today, we are pleased to introduce ALPHA Innolot MXE, a revolutionary alloy meticulously engineered to address the critical needs of enhanced reliability and performance in modern electronic assemblies.