-
- News
- Books
Featured Books
- pcb007 Magazine
Latest Issues
Current IssueInventing the Future with SEL
Two years after launching its state-of-the-art PCB facility, SEL shares lessons in vision, execution, and innovation, plus insights from industry icons and technology leaders shaping the future of PCB fabrication.
Sales: From Pitch to PO
From the first cold call to finally receiving that first purchase order, the July PCB007 Magazine breaks down some critical parts of the sales stack. To up your sales game, read on!
The Hole Truth: Via Integrity in an HDI World
From the drilled hole to registration across multiple sequential lamination cycles, to the quality of your copper plating, via reliability in an HDI world is becoming an ever-greater challenge. This month we look at “The Hole Truth,” from creating the “perfect” via to how you can assure via quality and reliability, the first time, every time.
- Articles
- Columns
- Links
- Media kit
||| MENU - pcb007 Magazine
Estimated reading time: 4 minutes
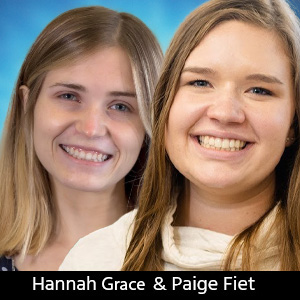
The New Chapter: Teach the Terminology
Imagine you've just graduated college and are off to start a career at an electronics manufacturer. Week one is filled with meeting the team, orienting your way around the floor, and learning the general flow of PCB manufacturing. Wow, there are so many steps! The next week is off to a similar start but with a team meeting to review a new part. Suddenly, the friendly team you met is speaking what sounds like a foreign language. Words are thrown around, such as buried vias, 370HR, back drill, and routed plated edges. None of these terms were taught during the college education you've just completed. Then, an overwhelming feeling kicks in, and you wonder if you will ever learn to speak this new language as fluently as your team.
There is often a similar disconnect between employers looking for qualified graduates and eager graduates in search of a career. A higher education cannot begin to teach the dictionary used in each industry a student may join. So, how is this terminology gap better bridged for the success of all parties involved? Fortunately, there are several initiatives that may be taken by a company to reduce the time it takes for an employee to learn the necessary terminology required for job performance.
1. A PCB Reference Guide
Let's face it, if all the words used daily in a fab house were written down, a new Webster’s Dictionary could be created around circuit boards alone. Having a document with images and definitions to describe the most common vocabulary allows an employee to make a quick reference without having to "bother" a colleague for the difference between ENEPIG and EPAG for the fourth time in a week. A document like this creates confidence in the employee to learn at their own pace between onboarding activities. PCB reference guides may include a basic process flow, animated/real images of defects and basic definitions for the top 100+ words and phrases. One good resource is IPC-T-50N, “Terms and Definitions for Interconnecting and Packaging Electronics Circuits.”
2. Internships
Internships are the best way to ease an employee into the industry. They create a lower pressure environment for students to work on projects relevant to potential careers whilst unconsciously picking up on new terminology. Along with the increased recruitment opportunities for the employer, internships are a wonderful opportunity for interns to work in multiple areas of a manufacturing facility with members of their future team. By the end of the summer, an intern will have the experience and understanding of PCB manufacturing not commonly held by their peers.
3. Mentorships
This is my personal favorite because I believe all good training programs involve a level of mentorship. Mentors can provide a verbal explanation with real examples in a timely manner. The mentee in this relationship will learn deep skills of the craft over a designated amount of time. While mentees may learn more vocabulary centered on certain areas of the manufacturing process, they will develop a general repertoire used by their colleagues. Note: A mentorship approach should be paired in conjunction with another approach to increase the knowledge base across the manufacturing processes.
4. PCB 101 Class
A PCB 101 course is a quick and easy way for all levels of employees to quickly learn the basic terminology heard on the floor. Both operators and technical positions can benefit from a one- to two-hour crash course into the makings of a PCB. A PCB 101 class is best when completed within the first three months of employment to allow the employee to connect what they are seeing each day. A bonus with this approach is that everyone participating in the class is at the same knowledge level with the course being taught. IPC offers a video course which may suit this need, titled, “Fundamentals of PCB Fabrication & Assembly.”
5. A Day With Final Inspection
Spending time with the final inspection department is one of the best opportunities to learn about defects in the manufacturing process. Just a couple of hours in the final inspection department is a lesson into conformance vs. non-conformance with reasoning why. An experienced final inspector can define the differences between measling, crazing, and haloing, or inkjet splatter and bleeding. These team members use industry standards and language to determine “good” vs. “bad.” Frankly, they are an invaluable resource from those who have seen (most of) it all while bringing the PCB process full circle. If you’re looking for a reference guide for inspection, IPC-A-600K, “Acceptability of Printed Boards,” is a good place to start.
Conclusion
Terminology can be troubling for new hires but there are ways to prevent it from becoming a barrier between employer and employees. Unfortunately, most employees will not come into a PCB manufacturing environment from another industry or higher education with the terminology base needed to succeed. If employers can quickly provide employees with the tools needed to speak their common language with one or two simple programs, both the employer and employee will reap the benefits. What tools can your company use to reduce the terminology barrier?
This column originally appeared in the November 2023 issue of PCB007 Magazine.
More Columns from The New Chapter
The New Chapter: The Benefits of Continuing EducationThe New Chapter: Navigating Maternity Leave in the Electronics Industry
The New Chapter: The Impact of Parasitics on PCB Design
The New Chapter: I’ve Found My ‘Why’
The New Chapter: Artificial Intelligence in PCB Design
The New Chapter: Lessons From the Best Engineer I’ve Ever Known
The New Chapter: Attracting ‘Generation Green’
The New Chapter: Dip Your Hand in the IPC APEX EXPO Candy Jar