-
- News
- Books
Featured Books
- pcb007 Magazine
Latest Issues
Current IssueThe Hole Truth: Via Integrity in an HDI World
From the drilled hole to registration across multiple sequential lamination cycles, to the quality of your copper plating, via reliability in an HDI world is becoming an ever-greater challenge. This month we look at “The Hole Truth,” from creating the “perfect” via to how you can assure via quality and reliability, the first time, every time.
In Pursuit of Perfection: Defect Reduction
For bare PCB board fabrication, defect reduction is a critical aspect of a company's bottom line profitability. In this issue, we examine how imaging, etching, and plating processes can provide information and insight into reducing defects and increasing yields.
Voices of the Industry
We take the pulse of the PCB industry by sharing insights from leading fabricators and suppliers in this month's issue. We've gathered their thoughts on the new U.S. administration, spending, the war in Ukraine, and their most pressing needs. It’s an eye-opening and enlightening look behind the curtain.
- Articles
- Columns
- Links
- Media kit
||| MENU - pcb007 Magazine
The Designer and Manufacturer Must Be in Sync
February 7, 2024 | Dana Korf, Korf ConsultancyEstimated reading time: 1 minute
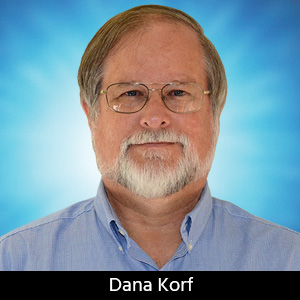
“Why can’t we all just get along?”—Henry Liberman, TEDx
It’s no industry secret that most PCB data packages sent to fabricators from designers cannot be built as-is. The finished boards often seem to work, despite a factory estimating what the designer wanted vs. what the documentation showed, then jointly rectifying issues through lengthy technical query (TQ) cycles. In general, everyone seems to be satisfied with this process, so why do we need to improve the designer/manufacturer relationship? Why is the best solution a strong designer/manufacturer relationship, and is it even possible?
Let’s perform a traditional root cause analysis and define the function of a designer vs. a manufacturer. Oxford Language definitions:
Designer: A person who plans the form, look, or workings of something before its being made or built, typically by drawing it in detail.
Manufacturer: A person or company that makes goods for sale.
This seems pretty straightforward. The manufacturer builds the product based on the supplied documentation. Unfortunately, the manufacturer’s front-end engineering team typically completes a portion of the design after the data package is received because it can’t be built as submitted. The manufacturer must update the design to maximize yield, meet cost targets, ensure reliability, and meet all performance requirements.
Typical design functions performed by the manufacturer include creating a material stackup that meets the specified mechanical thicknesses/tolerances, material selection, line width/spacing modification to generate the specified impedance/tolerance, creating the assembly array/panel design/documentation, and ensuring compliance with regulatory requirements, such as UL.
To read this entire article, which appeared in the January 2024 issue of PCB007 Magazine, click here.
Suggested Items
Discover the New Podcast Series on Thermal Management—Now Available
03/05/2025 | I-Connect007In this premiere podcast episode, Ryan Miller of NCAB breaks down why thermal management is a must for PCB designers. What are the main causes of excess heat in our designs today? Why does it matter? And how can designers keep their boards cool under pressure?
Harnessing Knowledge: A New IPC Course Now Available
01/27/2025 | Nolan Johnson, I-Connect007Didem Üstün is a mechanical engineer and subject matter expert about military cable design who’s now teaching a wire harness and semiconductor course through IPC. Here, she and Kel Allen, IPCs online instructor-led training manager, discuss the mechanics of the course and why you should consider taking it—especially if you have limited knowledge of wire harness.
I-Connect007 Editor’s Choice: Five Must-Reads for the Week
12/13/2024 | Andy Shaughnessy, I-Connect007This week, Peter Tranitz discusses the upcoming Pan-European Electronics Design Conference, set for Jan. 29-30 in Vienna, Austria. Pete Starkey brings us a review of the most recent EIPC Technical Snapshot webinar, which featured a global PCB maker update by Dr. Hayao Nakahara. Don't miss our interview with Manfred Huschka, who explains how companies can begin their own China Plus One plan. Stan Farnsworth breaks down photonic soldering and discusses its use in soldering materials that are not typically compatible. I also enjoyed Dan Beaulieu’s discussion on the value of consistency, and why just showing up for work is half the battle, especially in an inconsistent, evolving industry like ours.
It’s Only Common Sense: Results Come from Action, Not Intention
11/11/2024 | Dan Beaulieu -- Column: It's Only Common SenseEverybody has an excuse, and especially in business, there’s no shortage. Every day we hear why something didn’t work, a target wasn’t met, or an opportunity was missed. Excuses are easy. Action is hard. If you want to achieve results, stop making excuses and start acting. It’s only common sense.
Real Time with... SMTAI 2024: LPKF Laser Depaneling—Debunking the Heat Myth
10/29/2024 | Real Time with...SMTAILPKF's Jake Benz shares the testing results he presented at the SMTAI conference showing that laser depaneling is not a significant source of heat to PCBAs. Benz goes into details why.