-
- News
- Books
Featured Books
- pcb007 Magazine
Latest Issues
Current IssueSales: From Pitch to PO
From the first cold call to finally receiving that first purchase order, the July PCB007 Magazine breaks down some critical parts of the sales stack. To up your sales game, read on!
The Hole Truth: Via Integrity in an HDI World
From the drilled hole to registration across multiple sequential lamination cycles, to the quality of your copper plating, via reliability in an HDI world is becoming an ever-greater challenge. This month we look at “The Hole Truth,” from creating the “perfect” via to how you can assure via quality and reliability, the first time, every time.
In Pursuit of Perfection: Defect Reduction
For bare PCB board fabrication, defect reduction is a critical aspect of a company's bottom line profitability. In this issue, we examine how imaging, etching, and plating processes can provide information and insight into reducing defects and increasing yields.
- Articles
- Columns
- Links
- Media kit
||| MENU - pcb007 Magazine
Estimated reading time: 7 minutes
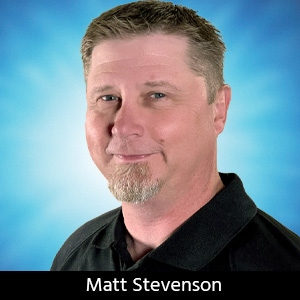
Connect the Dots: Are You Ready for 2024?
After an eventful 2023, we are excited to begin 2024 with new partners, challenges, and opportunities. I see 2023 as one of the most exciting and significant years at Sunstone Circuits since I began my career with the organization. We joined forces with American Standard Circuits (ASC), an organization that excels in producing ultra HDI, metal-backed/core, RF/microwave, flex, and rigid-flex PCBs for diverse industries.
We are excited about what this strategic alliance will bring in 2024, and with our universe expanding, I’ve taken another look at some of the topics we covered during the past year. My goal for these articles is to help connect the dots from concept to design to prototyping in order to help designers of every experience level get the most out of their PCBs by:
- Prioritizing high-payoff activities
- Avoiding parts-related manufacturability pitfalls
- Designing for efficient drilling
- Choosing the right CAD tool
With the expansive capabilities ASC brings to the table, we will engage designers on a wider range of projects and larger-scale production. It is worthwhile to review key topics from 2023 that are vital to a smooth process from design to assembly.
Prioritizing High-payoff Activities1
High-payoff activities (HPAs) are vital to achieving production excellence and fall into five categories:
- Safety
- Quality
- On-time delivery
- Cost reduction/efficiency gain
- Continuous improvement
Safety
Safety should be the top priority for every PCB manufacturer. Key HPAs in the safety arena include:
- Utilize engineering controls to error-proof (Poka-Yoke) safety standards.
- Use personal protective equipment (PPEs) to improve the safety of a working environment, especially in departments where chemical processes are used.
- Offer ongoing training to both new and current employees to ensure safety on the production floor.
Quality
Quality should be top of mind with respect to every aspect of production and embedded in the organization’s culture. The quality cycle begins with process development and persistent evaluation of production output data in search of process variances. This will help to determine where in the manufacturing cycle process quality output meets or exceeds expectations.
On-Time Delivery
Quality products do not arrive late. To ensure on-time delivery, manufacturers should focus on the following HPAs:
- Process the order correctly the first time
- Know the capacity limitations of the facility
- Continuously learn to overcome processing challenges using root cause analysis
Cost Reduction/Efficiency Gain
Efficiency gains and cost reductions sound like the same thing, but they are more like two sides of the same coin.
- Cost reduction is measured by use of fewer consumables
- Efficiency gains are the result of utilizing less labor
To improve both, manufacturers need meaningful, granular metrics in place to measure how much of each is being used. It is essential to understand labor costs at a granular level, including how process and technology impact operational efficiency down to the individual level.
Continuous Improvement
Continuous improvement is arguably the most important of the five HPAs. Manufacturers who implement and sustain quality management systems (QMS) will realize continuous improvement across the production floor.
- Common elements of successful continuous improvement programs include:
- Utilize Lean, Six Sigma, 5S, and 5-Why root cause analysis.
- Perform daily process walks, known as Gemba in the Lean Manufacturing philosophy. These provide daily observation of processes occurring in real-time and can uncover resource gaps.
Set the stage for solid countermeasures with processes like Plan-Do-Check-Act (PCDA), a method to continually improve and measure results that will prevent reoccurrence of an observed weakness or gap in the process.
Putting the five HPAs into daily practice in any production process will help keep the production team laser focused on achieving production excellence through the continual improvement cycle.
Avoiding Parts-Related Manufacturability Pitfalls2
Issues with parts fit are one of the most frequent causes of delay and cost overruns. These are five methods to avoid common, parts-related manufacturability issues.
- Pay close attention to pinhole size. It’s important to check component physical dimensions, take dimension tolerances into consideration, and account for variation that can impact fit. In addition to watching part sizes, pay close attention to the minimum, nominal, and maximum material conditions for the original part.
- What to do when the land pattern differs from pin size. One of the most frustrating mismatches with alternate through-hole parts is when the land pattern matches, but the pin size is off. When designing the land pattern, the pin size and tolerance range for components can be found in the product datasheet. Use that information to plan the proper hole size.
- Datasheets can disagree with CAD software. Third-party CAD libraries can contain millions of different parts, so discrepancies are inevitable. When the datasheet and the library part don't match up, address the delta before submitting the design. Always check any library part for accuracy before using it the first time.
- Pay attention to pinouts when using alternate vendor parts. Even if pin size and through-hole size are a confirmed match, and even if solder joints appear sound, a part can still not work as expected. Similar parts with the same footprint might look like they should act identically, but they won't always have the same pinout. Each transistor has a gate, drain, and source, but different manufacturers can differ in what goes where.
- Be aware of mechanical fit. Physical size of a component can keep parts from fitting into designated spaces. MMC body size should be the rule, so pay close attention to the tolerance range. As parts get larger or are sourced from multiple vendors, footprint size may need to expand considerably to accommodate all dimension and tolerance variables.
Designing for Efficient Drilling3
Drilling is one of the most fundamental steps in printed circuit board manufacturing. Designers can take several steps to improve the efficiency of drilling and help cut down on errors:
- Reduce the variety of through-hole sizes from the PCB design, allowing fewer tool changes.
- Avoid unnecessary design elements that can increase the chances for burring. Among these are higher copper weights and anything that can keep layered boards from sitting flat against each other.
- Minimize hole sizes to reduce the amount of material that needs to be drilled and removed from a board. In addition, a clever design can optimize spacing between the holes, which reduces the amount of motion a drill needs between drilling. These design optimizations might seem minimal, but their savings can add up for large manufacturing runs.
- Optimize the through-hole and pad sizes to facilitate the drilling process and ensure high-quality PCB manufacturing.
Accurate drilling is key to a reliable and efficient board, and by focusing on these essential elements, designers can produce PCBs with fewer errors and failure rates.
Choosing the Right CAD Tool4
Each designer has different needs from a CAD tool, and needs can vary by project. We recommend evaluating CAD software using the following criteria:
- Price: When evaluating tools, make sure they are actively maintained and have an acceptable level of user support. CAD tools funded and developed by PCB manufacturers are built to work with their manufacturing process, so make sure their capabilities match your design requirements not just their capabilities. Commercial packages can become expensive quickly, so pay attention to the limits placed on products with multiple tiers of pricing to be sure important features are not locked behind an expensive paywall.
- Component libraries: A typical designer might need a library of about 10,000 parts. When looking at the library offered by a CAD tool, confirm that the requisite parts are available. Look for commonly used parts and check if the tool comes with access to specialized libraries required for the project.
- Ease of use: CAD tools should be intuitive and easy to use. Ease of use is an area where less expensive, open-source software tends to lag behind. If price is an important factor in the decision-making process, the result can be a balancing act between price and usability.
- Help and documentation: Ensure that the CAD tool provider offers user support early in the process. CAD tool software providers should make their documentation available online; quality documentation can be a huge help to designers who need questions answered in a hurry.
The most important part about picking a CAD tool, though, is that it shouldn't make designing too much of a chore. You want designing to be productive and efficient, and in the end, maybe that's the most important element to evaluate when you're trying out different tools.
Ready for 2024
As we move into 2024, I look forward to exploring best practices on a variety of PCB design and manufacturing topics. Sunstone’s alliance with ASC has expanded our PCB universe and opened the door for a more in-depth look at the PCB designer’s role in ensuring the smooth manufacturing of really cool stuff, from design to prototype to large-scale production.
References
- “Top 5 High-profile Activities for Production Excellence,” by Kevin Beattie, Design007 Magazine, April 2023.
- “Avoiding Five Common Pitfalls of Parts,” by Matt Stevenson, Design007 Magazine, June 2023.
- “Best Drilling Practices for Better PCB Manufacturing,” by Tim Totten, Design007 Magazine, August 2023.
- “Choosing the Right CAD Tool,” by Matt Stevenson, Design007 Magazine, October 2023.
Download Matt's book The Printed Circuit Designer’s Guide to… Designing for Reality and listen to the podcast here. You can view other titles in the I-007eBooks library.
This column originally appeared in the February 2024 issue of Design007 Magazine.
More Columns from Connect the Dots
Connect the Dots: The Future of PCB Design and ManufacturingConnect the Dots: Proactive Controlled Impedance
Connect the Dots: Involving Manufacturers Earlier Prevents Downstream Issues
Connect the Dots: Stop Killing Your Yield—The Hidden Cost of Design Oversights
Connect the Dots: Designing for Reality—Routing, Final Fab, and QC
Connect the Dots: Designing for Reality—Surface Finish
Connect the Dots: Designing for Reality—Solder Mask and Legend
Connect the Dots: Designing for Reality: Strip-Etch-Strip