-
- News
- Books
Featured Books
- pcb007 Magazine
Latest Issues
Current IssueThe Hole Truth: Via Integrity in an HDI World
From the drilled hole to registration across multiple sequential lamination cycles, to the quality of your copper plating, via reliability in an HDI world is becoming an ever-greater challenge. This month we look at “The Hole Truth,” from creating the “perfect” via to how you can assure via quality and reliability, the first time, every time.
In Pursuit of Perfection: Defect Reduction
For bare PCB board fabrication, defect reduction is a critical aspect of a company's bottom line profitability. In this issue, we examine how imaging, etching, and plating processes can provide information and insight into reducing defects and increasing yields.
Voices of the Industry
We take the pulse of the PCB industry by sharing insights from leading fabricators and suppliers in this month's issue. We've gathered their thoughts on the new U.S. administration, spending, the war in Ukraine, and their most pressing needs. It’s an eye-opening and enlightening look behind the curtain.
- Articles
- Columns
- Links
- Media kit
||| MENU - pcb007 Magazine
Estimated reading time: 3 minutes
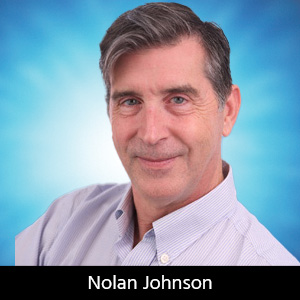
Nolan’s Notes: Do More, Get More
This month in SMT007 Magazine, we’re investigating box build, a manufacturing sector so closely adjacent to board assembly that some OEM customers think they’re the same thing. To those of us doing this work, we know they’re very different. Traditional electronic assembly work is typically concerned only with attaching the components to the circuit board. That’s our idea of a “finished good.”
But what’s finished to us is just a subassembly to the OEM. That board still must be hooked up to other bits and bobs—maybe a power supply and a set of buttons, or perhaps an enclosure. There might be other boards to connect either directly or via wiring. Those extra steps mean you’re shipping the populated boards somewhere else, which lengthens the supply chain and manufacturing lead times, uses more logistical resources, and more. So, what to do?
Well, for many OEMs, co-locating board assembly and box-build services make sense under these circumstances. Instead of a long line of vendors, each doing just one step of the assembly process, what if one vendor could do all the steps? This can make the OEM’s life a lot easier. (I know, there are a lot of steps in assembly, but from an OEM product manager’s point of view, board assembly is a single box on their supply chain flow chart.)
For many EMS suppliers, adding box-build services makes sense, too. In essence, an EMS provider’s value-add is project-based specialized labor. If they can add even more specialized labor services, which are of value to their OEM customers, then they’re likely to 1) get more business from each job in the queue; 2) earn customer loyalty by owning more of the customer’s manufacturing process; and 3) attract new customers who need those expanded services as well. It’s tempting. But board assembly and box build are like cats and dogs: Both can be very good for the quality of your life, but the care and feeding of the two are very different if you want them to thrive.
When I started researching this topic, I expected we would publish content on technical and practical box-build topics: workstations, tools, training, hiring, and such. But I soon realized this is a business planning story. What’s different are the manufacturing philosophy and skill set; hiring criteria are similar, but also different. The supply chain, standards, and functional test requirements are not the same. In other words, some unique investment is required when committing to box build, especially if you aspire to build the OEM’s finished product and drop-ship their orders.
In this issue, Joe O’Neil gives a business-level tutorial on how box build is its own animal. Jon Schmitz, business development head at RiverSide Integrated Solutions, provides a day in the life of a company specializing in both assembly and box build. Columnist Mike Konrad brings a second practical perspective to his interview with two assembly experts doing box build. Since it’s wiring that connects the boards to the box, we also talked in-depth with Christina Rutherford, a materials engineer specializing in aviation wiring harnesses, about the role of wire harness manufacturing and standards developed by both WHMA and IPC.
In addition to the feature content, we bring you a case study on the contribution of inspection equipment at ADCO, and an article by Susan Kayesar on how cloud-based services are contributing to improved design for manufacture throughout the manufacturing chain—including assembly. Dr. Jennie Hwang starts her column series on artificial intelligence, and we round out the issue with a box-build/wire harness related paper from the IPC APEX EXPO 2023 Technical Program on testing pull force on crimped connectors. (I guess there was some practical information on this issue, after all.)
If you aspire to grow your business, increase your margins, generate “more sticky” customer relationships, or do any combination of the three, you will find information on this issue that will further your understanding and perhaps even help you avoid pitfalls.
This column originally appeared in the April 2024 issue of SMT007 Magazine.
More Columns from Nolan's Notes
Nolan’s Notes: Finding Your Sweet SpotNolan’s Notes: Moving Forward With Confidence
Nolan's Notes: The Next Killer App in Component Manufacturing
Nolan’s Notes: Looking Deep Into the Future With X-ray
Nolan’s Notes: Your Golden Ticket
Nolan's Notes: Find the Help You Need—Accessing Technical Resources
Nolan’s Notes: Emerging Trends in 2025
Nolan’s Notes: Soldering Technologies