-
- News
- Books
Featured Books
- design007 Magazine
Latest Issues
Current IssueCreating the Ideal Data Package
Why is it so difficult to create the ideal data package? Many of these simple errors can be alleviated by paying attention to detail—and knowing what issues to look out for. So, this month, our experts weigh in on the best practices for creating the ideal design data package for your design.
Designing Through the Noise
Our experts discuss the constantly evolving world of RF design, including the many tradeoffs, material considerations, and design tips and techniques that designers and design engineers need to know to succeed in this high-frequency realm.
Learning to Speak ‘Fab’
Our expert contributors clear up many of the miscommunication problems between PCB designers and their fab and assembly stakeholders. As you will see, a little extra planning early in the design cycle can go a long way toward maintaining open lines of communication with the fab and assembly folks.
- Articles
- Columns
Search Console
- Links
- Media kit
||| MENU - design007 Magazine
Plasmatreat at IPC APEX EXPO 2024
April 2, 2024 | PlasmatreatEstimated reading time: 2 minutes
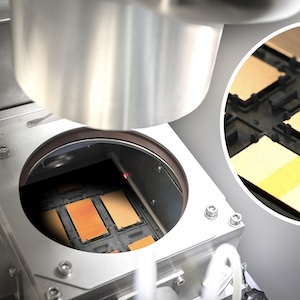
For the pretreatment of highly sensitive electronic components, Plasmatreat will present a real innovation at the IPC APEX Expo in Anaheim 2024: The new REDOX tool safely and effectively reduces oxide layers on electronic components in an inline process. The company will be demonstrating how processes in the electronics industry can be made more efficient and environmentally friendly with plasma systems operating under atmospheric pressure from April 9 – April 11, 2024, at booth 2843.
REDOX-Tool: Alternative process to the usage of flux
Metals are an important part of electronics manufacturing. However, their surface oxidizes when it is exposed to air and humidity and prevents the formation of a perfect solder joint in the production process. With the REDOX-Tool, Plasmatreat is presenting a game-changing innovation at IPC APEX that provides a remedy and can even make the use of flux redundant: The REDOX-Tool, a special production cell (Plasma Treatment Unit/PTU), removes oxide layers in an inline process. The innovative system uses only a combination of nitrogen and hydrogen, eliminating the need for environmentally harmful formic or citric acids. For treatment, components are heated in a single or dual-lane tunnel flooded with inert gas (e.g. N2 or N2H2) and prepared for plasma reduction. Plasma nozzles, also operating with inert gas, reliably remove trapped oxygen molecules from the metal surface. Controlled cooling of the treated products under inert conditions stabilizes the reduction achieved for the next process step. The result of the plasma application is optimized surface adhesion and reliable adhesion in subsequent processes. This effectively reduces defects, delamination and product failure. The innovative REDOX-Tool also provides complete process control and product traceability.
Surface Pretreatment Before Conformal Coating
Another topic covered at the show will be the importance of surface pretreatment before conformal coating. Effective pretreatment is crucial before the application of conformal coating in electronics, ensuring optimal coating performance and maximal protection for electronic components. This preparatory process typically encompasses multiple stages, including thorough cleaning, surface preparation, and conditioning of circuit boards and components.
Failure to properly pretreat the surface before applying conformal coating can lead to various issues, including incomplete coverage, bubbling, blistering, cracking, and curing problems. Incompatibility between the coating and substrate may cause detachment, leaving areas vulnerable. Contaminants present on the surface can compromise the coating's efficacy and durability. Moreover, certain conformal coatings are difficult to remove for rework or repair, resulting in costly fixes or high reject rates.
Effective pretreatment is essential for addressing and preventing these challenges associated with conformal coating in electronics. Proper pretreatment can enhance adhesion, promote coating uniformity, and bolster the overall effectiveness of the protective layer. Careful selection of pretreatment methods based on factors such as substrate material, environmental conditions, and coating type is crucial. Adhering to industry standards and guidelines for pretreatment processes further ensures the successful application and performance of conformal coatings in electronic components.
"Plasmatreat addresses the growing complexities in electronics manufacturing processes with cutting-edge, inline-capable plasma technology. The pretreatment of delicate products using potential-free Openair-Plasma significantly enhances product quality, cost efficiency, process reliability, and environmental sustainability," explains Hardev Grewal, President and CEO at Plasmatreat USA, Inc.
Visit Plasmatreat at IPC APEX EXPO, at booth 2843.
Suggested Items
Real Time with... IPC APEX EXPO 2024: Final Finishes and IC Substrate Manufacturing
04/24/2024 | Real Time with...IPC APEX EXPOEditor Marcy LaRont and Richard DePoto, Uyemura's Business Development Manager, engage in a comprehensive discussion about the positive aspects of the show, the benefits of RAIG in final finishes, and the hurdles faced when upgrading your surface finish. Also discussed are the role of Uyemura's MEC pretreatment agents in IC substrate manufacturing and the importance of collaboration and knowledge sharing.
The Plating Forum: The Critical Role of Pretreatment for Plating
10/22/2020 | George Milad -- Column: The Plating ForumPretreatment is usually customized to the incoming substrate and the plated metal. George Milad explains how it is a critical step and must be completed before plating to achieve the desired adhesion and to enhance the quality of the deposited metal.
Atotech Launches ST-Line
12/08/2016 | AtotechAtotech has launched the ST-Line, state-of-the-art equipment designed for the requirements of soldermask and dry film pretreatment processes in the manufacturing of PCB.