-
- News
- Books
Featured Books
- design007 Magazine
Latest Issues
Current IssueRules of Thumb
This month, we delve into rules of thumb—which ones work, which ones should be avoided. Rules of thumb are everywhere, but there may be hundreds of rules of thumb for PCB design. How do we separate the wheat from the chaff, so to speak?
Partial HDI
Our expert contributors provide a complete, detailed view of partial HDI this month. Most experienced PCB designers can start using this approach right away, but you need to know these tips, tricks and techniques first.
Silicon to Systems: From Soup to Nuts
This month, we asked our expert contributors to weigh in on silicon to systems—what it means to PCB designers and design engineers, EDA companies, and the rest of the PCB supply chain... from soup to nuts.
- Articles
- Columns
Search Console
- Links
- Media kit
||| MENU - design007 Magazine
Estimated reading time: 3 minutes
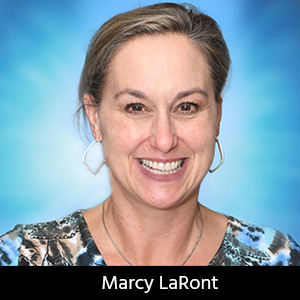
Marcy’s Musings: The ‘Magic’ of Additive Processes
Repair, replace, or go in a completely different direction? Today’s PCB manufacturers grapple with these questions as they look to their customers, supplier partners, and even the government to discern what will make the most economic sense for their businesses over the long term. Purchasing capital equipment is often a fraught endeavor unless you have an unlimited bankroll or significant government backing.
I get it. I don’t buy a “new” car until I drive my existing car into the ground. I like high-end, but I don’t like car payments. My average car ownership is eight or more years. As with any large capital purchase essential to your everyday life, the longer you own it, the less it costs over time. It’s good financial management. Something must change for me to consider a different strategy: the car is beyond repair, the cost of maintenance is now at unacceptably high levels, and/or the market presents the opportunity to purchase a new, better vehicle in such a way that seems to assure a better ROI.
Such is the crossroads at which many PCB fabricators find themselves when deciding whether to change their current processes and go additive or stay the course until something significant compels a change. But change is on the horizon, and it seems to be driven by significant technological advancements in chips and advanced packaging, offering PCB fabricators some additive manufacturing solutions to explore.
In this month’s issue of PCB007 Magazine, we talk to several industry members about additive manufacturing technology for the PCB fabricator. Though modern semi-additive and fully additive technologies are still emerging for PCB manufacturing, additive technology is not new. In its simplest definition, additive manufacturing (AM) is the process of creating something by adding layers of material to achieve the desired end. This issue will discuss where it stands today, where the benefits truly lie, and where it seems to be headed.
Kicking off our issue, I encourage you to take some time with Alex Stepinski of Smart Factory Design, our resident expert in sustainable manufacturing processes for high-technology products, who reviews areas in PCBs where additive technology is currently developing, and offers a solution for broader industry adoption of inkjet solder mask much sooner in "Will Modern Additive Manufacturing Revolutionize PCB Manufacturing?" He discusses this specific technology and it seems to tick all the ROI boxes: reductions in cycle time, waste, energy usage, the number of human operators required, and increased reliability, which translates to a reduced loaded cost to manufacture. This is explained well in my interview with Milena and Hans Fritz of German equipment distributor SAT in how they address both technology development and moving customer partners forward on the journey to change.
My discussion with PCB fabricator Winonics answers this query in a different way as they share not only how they approach their business, but what they are doing in AM R&D. Also featured in this issue is additive pioneer Nano Dimension, whose CTO provides a compelling overview of how ML and AI encapsulated in much of additive manufacturing processes have the power to revolutionize PCB prototyping. Rounding out the issue, I had the pleasure of interviewing Antonio Schmidt and David Hahn of Notion Systems at IPC APEX EXPO about their digital inkjet process, ROI, EHD, and more.
As usual, our columnists come to the fore with much value-added information. Don Ball with Chemcut takes a counterpoint approach to the drive for moving toward inkjet and additive manufacturing, by asking, “Can the limits of subtractive etching be extended?” Paige Fiet explains the 8D problem-solving method she learned from her father, the best engineer she has ever known. Happy Holden provides his technical expertise in the next installment of Happy’s Tech Talk on semi-flex FR-4. Travis Kelly of PCBAA discusses the most recent development in the 2025 budget allocation for the Defense Production Act and puts out a call to action for industry members.
To move away from what has been our tried-and-true approach to fabricating boards with features that were considered small just 10 years ago and over 95% yields is tough, but will the decision be made for us over the next 10 years? What is certain is that PCB fabricators should be paying close attention to all things "additive manufacturing" as our part of the supply chain evolves to support next-generation technology and packaging requirements, whether or not fabricators decide to participate.
This column originally appeared in the May 2024 issue of PCB007 Magazine.
More Columns from Marcy's Musings
Marcy’s Musings: Destination MetallizationMarcy's Musings: Charting the Future
Marcy’s Musings: Attaining Superior Wet Process Control
Marcy’s Musings: The Art, Science, and Reality of Thriving
Marcy’s Musings: All Things Material
Marcy's Musings: The Growing Industry
Marcy’s Musings: The Many Facets of Sustainability
Marcy’s Musings: Countdown—The Fabricator’s Guide to IPC APEX EXPO