-
- News
- Books
Featured Books
- pcb007 Magazine
Latest Issues
Current IssueInventing the Future with SEL
Two years after launching its state-of-the-art PCB facility, SEL shares lessons in vision, execution, and innovation, plus insights from industry icons and technology leaders shaping the future of PCB fabrication.
Sales: From Pitch to PO
From the first cold call to finally receiving that first purchase order, the July PCB007 Magazine breaks down some critical parts of the sales stack. To up your sales game, read on!
The Hole Truth: Via Integrity in an HDI World
From the drilled hole to registration across multiple sequential lamination cycles, to the quality of your copper plating, via reliability in an HDI world is becoming an ever-greater challenge. This month we look at “The Hole Truth,” from creating the “perfect” via to how you can assure via quality and reliability, the first time, every time.
- Articles
- Columns
- Links
- Media kit
||| MENU - pcb007 Magazine
Will Modern Additive Manufacturing Revolutionize PCB Manufacturing?
June 3, 2024 | I-Connect007 Editorial TeamEstimated reading time: 2 minutes
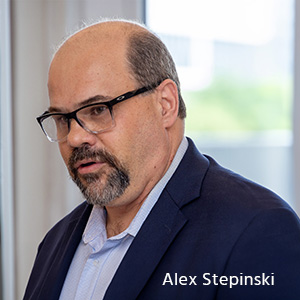
In this interview, Alex Stepinski delves into the evolving landscape of additive manufacturing technology in PCB fabrication. He highlights the historical shifts in additive and subtractive processes and emphasizes the recent focus on fine patterning and 3D printing. He discusses the challenges faced in achieving fully additive processes, citing past experiences and the need for extensive process control. The conversation also explores the drivers and barriers to adoption, with Alex underscoring the importance of OEM involvement and targeted marketing efforts.
Marcy LaRont: Alex, as high-density PCB requirements move to sub-25 micron features, traditional subtractive PCB processes simply cannot get us there. Let’s talk about additive manufacturing technology as it relates to PCB manufacturing: What are its advantages, disadvantages, and costs, and where that technology seems to be headed?
Alex Stepinski: Additive processes have been part of PCB fabrication since the beginning. Industry has basically just vacillated the ratio of subtractive to additive over time.
It changes based on production and process strategies. As always, there is the consideration of how to get where you need to be technologically, with reliability, and with the equipment you already have. Historically, companies have approached their manufacturing differently. Some companies were all panel plating. Some companies were all pattern plating, and some were a mix of the two. Today, you have a synthesis of both.
Recent discussions around additive have focused on very fine patterning, which forces a higher ratio of additive plating than historically has been commonly experienced in the market. The other aspect is 3D printing, an additive method that's been growing in recent years. We started talking about solder mask 20 years ago. Finally, some companies are leading the way in advanced 3D printing of solder mask.
Now, we are also starting to see additive in materials in conductive and dielectric layers. There are a host of different additive processing methods being applied today. There is still a lot of due diligence that needs to be done. In 2013, I helped build the first additive factory globally. It was 100% inkjet for resists and solder mask. No one has done a fully additive facility since that time. It worked very well for low-tech products. The challenge was that the process window was very small and required a lot of customization. Unfortunately, that inkjet supplier went out of business years later because nobody else could hold the process window that tightly without an inline process like ours.
To really have a fully additive process, and not just 3D printing, you need a lot of process control that we don't generally have in the market.
Barry Matties: It seems like you are describing a process engineer, someone who pays close attention to monitoring and controlling processes. Do you see a lack of process engineers?
Alex Stepinski: What I am talking about with the additive factory example is a case study from 10 years ago. A lot of process development was needed to identify the process control specifications. Once that was done, we were able to hold the specifications without significant supervision. Unfortunately, a lot of what we learned back then relative to additive is lost knowledge. From what I've seen in the market, people are relearning many of those lessons now. Adoption is still in its infancy, but I am happy to see it finally picking up.
To read this entire conversation, which appeared in the May 2024 issue of PCB007 Magazine, click here.
Testimonial
"Advertising in PCB007 Magazine has been a great way to showcase our bare board testers to the right audience. The I-Connect007 team makes the process smooth and professional. We’re proud to be featured in such a trusted publication."
Klaus Koziol - atgSuggested Items
Insulectro and Electroninks Sign North American Distribution Agreement
08/12/2025 | InsulectroElectroninks, a leader in metal organic decomposition (MOD) inks for additive manufacturing and advanced semiconductor packaging, today announced a strategic collaboration and distribution partnership with Insulectro, a premier distributor of materials used in printed electronics and advanced interconnect manufacturing.
STARTEAM GLOBAL Unveils Innovative Additive Solder Mask Process
06/02/2025 | STARTEAM GLOBALSTARTEAM GLOBAL, a leading PCB manufacturer, has introduced a revolutionary additive solder mask process at its Flero STARTEAM (FST) factory in Italy, leveraging digital inkjet technology to enhance production efficiency and sustainability.
Smart Automation: The Growing Role of Additive Manufacturing
04/23/2025 | Josh Casper -- Column: Smart AutomationAs additive manufacturing (AM) matures and reaches new business sectors throughout the manufacturing world, electronics manufacturing is beginning to reap the benefits of this ultra-flexible technology. AM (also known as 3D printing) capabilities have now expanded to support a wide range of applications in the electronics industry. The development of materials in additive manufacturing is meeting the demands of high-temperature environments and ESD protection necessary to become a viable solution in electronics manufacturing.
J.A.M.E.S. Explores the Future of Additive Manufactured Electronics
02/18/2025 | Marcy LaRont, I-Connect007Andreas Salomon is chief scientist at J.A.M.E.S, a joint venture of Nano Dimension and HENSOLD. In this interview he discusses the evolving landscape of additively manufactured electronics, highlighting the integration of cutting-edge technologies, such as micro-dispensing and ink jetting. These technologies enhance capabilities in signal integrity and miniaturization. He also talks about the importance of sustainability, the need for standardized testing, and collaboration among industry leaders that will drive innovation and transform the future of electronics manufacturing through IPC’s standards development.
Rogers Announces Addition of Woon Keat Moh to Board of Directors
12/23/2024 | Rogers CorporationRogers Corporation announced that Woon Keat Moh ("Moh") has been appointed as an independent member of the Company’s Board of Directors, effective January 1, 2025. Following this change, the Board will be composed of nine members, eight of whom are independent.