-
- News
- Books
Featured Books
- pcb007 Magazine
Latest Issues
Current IssueInventing the Future with SEL
Two years after launching its state-of-the-art PCB facility, SEL shares lessons in vision, execution, and innovation, plus insights from industry icons and technology leaders shaping the future of PCB fabrication.
Sales: From Pitch to PO
From the first cold call to finally receiving that first purchase order, the July PCB007 Magazine breaks down some critical parts of the sales stack. To up your sales game, read on!
The Hole Truth: Via Integrity in an HDI World
From the drilled hole to registration across multiple sequential lamination cycles, to the quality of your copper plating, via reliability in an HDI world is becoming an ever-greater challenge. This month we look at “The Hole Truth,” from creating the “perfect” via to how you can assure via quality and reliability, the first time, every time.
- Articles
- Columns
- Links
- Media kit
||| MENU - pcb007 Magazine
Estimated reading time: 5 minutes
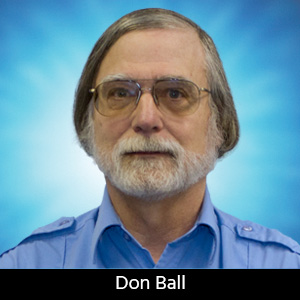
The Chemical Connection: Can the Limits of Subtractive Etching Be Extended?
Subtractive etching has been the technology of choice since the era of PCBs began in the mid-1950s. I can remember TV ads for one manufacturer that claimed their TV sets were of much higher quality claiming, “We use wires to make the connections for our television sets, not cheap printed circuit boards.” Imagine that.
Many alternative technologies have been tried—e.g., conductive inks applied with an ink jet printer, direct metallization, and semi- and fully-additive manufacturing—but none have been able to match the low cost and high productivity of the subtractive process. However, the subtractive process has its limits, and those limits are being challenged by the calls for the higher and higher circuit densities demanded today.
The problem, of course, is that the subtractive etching process etches sideways as well as downward in a ratio of one unit sideways to every three or four units down, depending on which etchant is used and the etchant parameters. This means there is a limit to how deeply one can etch before completely undercutting the etch resist at the top of the circuit. What are those limits? A reasonably good circuit board manufacturer today should be able to achieve 75-µm[MT1] (0.003") lines and spaces in 35-µm (1-ounce) foil, 50-µm (0.002") lines and spaces in 17-µm (half-ounce) foil, and (maybe, with some difficulty) 25-µm (0.001") lines and spaces in 5-µm (1/8-ounce) foil.
The ability to etch a 25-µm line and space in 5-µm copper sounds good with the demand for this type of density becoming more common. Unfortunately, there is something else that must be taken into consideration, in addition to the fact that the thinner foil is more expensive. A line in thinner copper has a much lower cross-sectional area and is more resistant to current flow than the same width line in thicker copper. This means that a lot more heat is generated for the same current flow, which may be unacceptable when considering how tightly packed the circuit lines are. The specification for the high-density lines may also include requirements that a 25-µm line has to be 17- or even 35-µm thick.
There are some things that can be done to improve upon these line and space limits. The key is to reduce the aspect ratio (the combined thickness of the etch resist and the foil divided by the space to be etched). The higher the aspect ratio the more difficult it is to get fresh etchant down into the space and remove spent etchant. In practical terms, this means that, for equal thicknesses of resist and foil, the etch rate in the spaces gets slower as the spaces narrow. Tests have shown that the etch rate in a 25-µm space is only about 60% that of a 125-µm space for the same thickness of resist and foil. As a result, there is more time for sideways etch and the ratio of downward etch to sideways etch can go from 3 to 1, 3 to 2, or even 1 to 1.
The limits above were achieved using a 30 µm (0.0018") thick dry film resist, which is probably the most common thickness in use today. That means that the aspect ratio of a 75-µm space etched in 35-µm foil is 30-µm resist + 35-µm foil divided by 75-µm space or 0.87. The aspect ratio of a 50-µm line etched in 17-µm foil with the same resist is 0.94. From this, we can assume the minimum aspect ratio for a successful subtractive etching process is around 1 (the closer to 1, the more difficult it is to etch but it’s still possible for most manufacturers). It is possible to achieve successful subtractive etching with aspect ratios higher than this, but it requires utmost attention to detail and optimization of every process step. For the purposes of this discussion, let’s use 1 as the minimum aspect ratio. If you are doing 75-µm lines and spaces on 35-µm copper with a 30-µm resist now, then you should be able to do finer lines and spaces with a reduced aspect ratio without any more problems than you have now (hopefully).
Reducing the aspect ratio by using thinner foil might not be acceptable due to increased heat generation, but reducing the thickness of the etch resist is certainly a viable option. Dry films come in various thicknesses depending on the application. The thinnest I have seen for general application is 15 µm. Going to this thickness will make it possible to do 50 µm spaces in 17 µm foil (aspect ratio 0.64) and just possible to do 25-µm spaces in 9-µm foil (aspect ratio 0.94), which is a help but may still be short of what is needed. And, of course, a 15-µm resist is going to cost significantly more than a 30-µm resist.
The best alternative for reducing the aspect ratio is to use a liquid resist. There are liquid resists available that are basically liquid dry films that can be applied to circuit foil in thicknesses of 5 µm or a little less. These have an additional advantage in that whatever type of exposure process you use, it doesn’t have to deal with a cover sheet like that on hot roll laminated dry films. With a 5-µm resist, the aspect ratio for a 50-µm space on 35-µm foil becomes 0.8, well under the maximum aspect ratio of 1 we have determined is the limit for subtractive etching. For 25-µm lines in 17-µm foil, the aspect ratio is 0.88, making it theoretically possible to etch 1-mil lines and spaces in half-ounce foil. I say theoretically because, not having access to a liquid resist coater, I’ve not been able to try this. Extending the theoretical a little further, it may be possible to go down to 15-µm lines and spaces in 9-µm foil.
So, there is some hope for extending the limits of subtractive etching by using a liquid resist. This will still involve capital expense for coaters (roll coaters, spin coaters, or dip coaters) and ovens for baking and maybe multiple lines depending on production levels. You’ll still need a very good exposure system as well, which may require an upgrade. This will give you the chance to remain competitive in the higher density circuit market and will be a lot less expensive than going to a fully additive process or opting out of this market altogether.
This column origiinally appeared in the May 2024 issue of PCB007 Magazine.
More Columns from The Chemical Connection
The Chemical Connection: Sales Organization from a Capital Equipment PerspectiveThe Chemical Connection: Through-glass Vias in Glass Substrates
The Chemical Connection: Reducing Defects in Circuit Board Production
The Chemical Connection: Common Misconceptions in Wet Processing
The Chemical Connection: Surface Finishes for PCBs
The Chemical Connection: Earthquakes, Astronauts, and Aquatics—A Lighter Look at the Past
The Chemical Connection: Better Fabs Attract a Better Workforce
The Chemical Connection: Can Changing Spray Nozzles Improve My Etch Quality?