-
- News
- Books
Featured Books
- pcb007 Magazine
Latest Issues
Current IssueThe Hole Truth: Via Integrity in an HDI World
From the drilled hole to registration across multiple sequential lamination cycles, to the quality of your copper plating, via reliability in an HDI world is becoming an ever-greater challenge. This month we look at “The Hole Truth,” from creating the “perfect” via to how you can assure via quality and reliability, the first time, every time.
In Pursuit of Perfection: Defect Reduction
For bare PCB board fabrication, defect reduction is a critical aspect of a company's bottom line profitability. In this issue, we examine how imaging, etching, and plating processes can provide information and insight into reducing defects and increasing yields.
Voices of the Industry
We take the pulse of the PCB industry by sharing insights from leading fabricators and suppliers in this month's issue. We've gathered their thoughts on the new U.S. administration, spending, the war in Ukraine, and their most pressing needs. It’s an eye-opening and enlightening look behind the curtain.
- Articles
- Columns
- Links
- Media kit
||| MENU - pcb007 Magazine
Estimated reading time: 1 minute
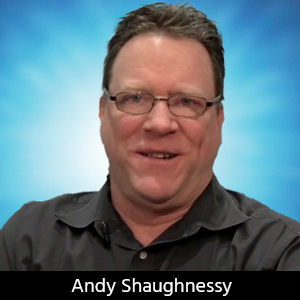
The Shaughnessy Report: All Together Now—The Value of Collaboration
PCB designers could learn quite a bit from NASA and the private companies that develop spacecraft: Every one of these vehicles is a testament to the value of collaboration among disparate stakeholders. Without a collaborative culture, the rocket might never get off the ground.
Of course, most PCB designers would probably agree that collaboration is an important part of the design process. But does the average designer truly collaborate with all the stakeholders involved in designing and manufacturing the board? Most likely not.
Many designers are still tossing the design “over the wall” and hoping for the best. They don’t talk to the fabricator or the assembly provider, and definitely not the component supplier. They’re just out there winging it because that’s how they’ve always done it, and it’s worked out most of the time.
Collaborating with your fab and assembly partners goes a long way toward reducing or eliminating respins. The typical PCB design undergoes an average of three respins. Now, many companies just assume that the board will go through a respin or two, and that extra cost is included in the budget. By the time the board gets put on hold in fab or assembly, the designer is already working on another design. The problems are baked in the cake.
For this month’s issue of Design007 Magazine, we asked our expert contributors to weigh in on collaboration. We start off with a conversation with Charlie Capers, who discusses how PCB designers can create a collaborative culture at their company. Kelly Dack then explains how collaboration among stakeholders can lead to a smooth, successful design, and the lack of collaboration can lead to respins, boards being put on hold, and field failures. Stephen Chavez illustrates how true collaboration can even help a designer’s work/life balance.
In our conversation with John Watson and his student Mehdi Kacem, Mehdi explains how his drive to learn and willingness to collaborate have helped him succeed in John’s PCB design classes. Duane Benson points out the need to communicate with your component provider, who should be considered a full partner in your design cycle. We also have columns from Barry Olney, Matt Stevenson, and Hannah Grace, and an article by Anaya Vardya.
This column originally appears in the June 2024 issue of Design007 Magazine.
More Columns from The Shaughnessy Report
The Shaughnessy Report: Planning Your Best RouteThe Shaughnessy Report: Solving the Data Package Puzzle
The Shaughnessy Report: Always With the Negative Waves
The Shaughnessy Report: Breaking Down the Language Barrier
The Shaughnessy Report: Back to the Future
The Shaughnessy Report: The Designer of Tomorrow
The Shaughnessy Report: A Stack of Advanced Packaging Info
The Shaughnessy Report: A Handy Look at Rules of Thumb