-
- News
- Books
Featured Books
- pcb007 Magazine
Latest Issues
Current IssueInventing the Future with SEL
Two years after launching its state-of-the-art PCB facility, SEL shares lessons in vision, execution, and innovation, plus insights from industry icons and technology leaders shaping the future of PCB fabrication.
Sales: From Pitch to PO
From the first cold call to finally receiving that first purchase order, the July PCB007 Magazine breaks down some critical parts of the sales stack. To up your sales game, read on!
The Hole Truth: Via Integrity in an HDI World
From the drilled hole to registration across multiple sequential lamination cycles, to the quality of your copper plating, via reliability in an HDI world is becoming an ever-greater challenge. This month we look at “The Hole Truth,” from creating the “perfect” via to how you can assure via quality and reliability, the first time, every time.
- Articles
- Columns
- Links
- Media kit
||| MENU - pcb007 Magazine
Estimated reading time: 5 minutes
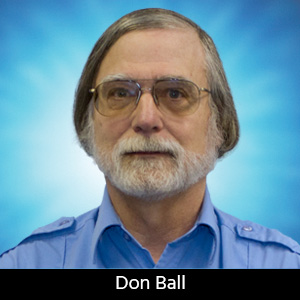
The Chemical Connection: Chemical and Equipment Control of High-density Circuits
As line and space requirements and specifications get increasingly tighter, it is obvious that at some point you must consider tightening the controls on the chemical and equipment parameters (temperature, specific gravity, conveyor speed, etc.) of your production lines to meet those requirements. For the purposes of this discussion, let’s consider line and space requirements of 75 µm (0.003") or less with tolerances of ±5% as the tipping point for serious consideration of tighter chemistry and equipment control.
There are optional controls (at extra cost, of course) available from most equipment suppliers to tighten up these parameters. On the other hand, I’ve seen equipment ordered with every conceivable control imaginable, all the bells and whistles, so to speak, only to visit that plant a year later and find most of them weren’t being fully used because they found they didn’t need as tight a control as they initially thought. So, just how much expensive control equipment do you really need?
We will initially focus on the etchers using cupric chloride and alkaline etchants. The etcher is the critical point in the production process where small changes in chemistry or equipment parameters can have a significant effect on line-width specifications and where tighter controls can be of the most benefit. The chemistry parameters that need to be monitored (not necessarily in order of importance) are temperature, specific gravity, oxidation reduction potential (ORP), free acid for cupric etchers, and pH and chlorides for alkaline etchers. Equipment-wise, the important parameters are conveyor speed, spray pressure, and oscillation. Most etchers in use today have some form of spray tube movement to improve chemistry exchange and even out the side-to-side etch profile on the etched panels.
Let’s take a brief look at each of these parameters to determine what is needed and where improved control (costs more) can be effective.
Before delving into the individual parameters, I have one important piece of advice to give on equipment purchases. Most etchers nowadays come with PLC control displays. I have occasionally seen requests for relay electronics, mostly as a cost reduction consideration and, in some cases, unwillingness to switch from a tried and true, easy-to-understand system to a newfangled computer system. Don’t even think about getting a new etcher for high-density circuits without a PLC control display.
All etching machines will come with a temperature controller as standard. Most control specifications that I have seen are in the ±1°F range. My observations show that most are really holding temperature variation to ±0.5°F or less. Testing has shown that the change in etch rate due to temperature for cupric chloride operating at 130°F (54°C) is about 0.5 µm per min./°F. (Alkaline is a little more, but not much.) So, for a temperature control that holds temperature to a ±0.5°F range, the maximum change in etch rate will be, at most, 0.5 µm per minute and will probably be much less than this. If you want to control your temperature even tighter than this, the alternative will be something like an encoder-based AC servo motor control for a couple of thousand dollars of extra cost. It is for you to decide if closer control is needed.
Again, most etchers will have a specific gravity control as standard. For cupric chloride the maximum etch rate occurs at about 34°Be (1.306 sg) and the lowest etch rate at 28°Be (1.239 sg). The change in etch rate between these two extremes is approximately 0.4 µm per min./°Be (0.11 sg units). The specific gravity controls that come standard on a typical etcher should be able to hold the set point at ±0.5°Be, so we’re looking at a maximum change in etch rate of 0.4 µm/min. Except for the tightest tolerance work, this should be more than adequate for high-density work. For alkaline etchant, the situation is a little different. The specific gravity is the trigger for the addition of replenisher solution that not only controls the specific gravity but also the pH through the ammonia in the solution and the chloride levels from the ammonium chloride added, which is also contained in the solution. Thus, even though the change in etch rate due to specific gravity is not much greater than that for cupric chloride, changes in pH and chloride levels will also affect etch rates. For this reason, a much tighter control of the specific gravity for alkaline etchant is highly recommended. The price of a controller that will hold a specific gravity set point of ±0.1°Be will be in the range of $5,000–$10,000 but should be considered essential for alkaline etchers, especially for high-density work.
For cupric chloride, the main control is the ORP, which basically measures the ratio of Cu+2 ions to Cu+1 ions displayed as millivolts. As the Cu+1 concentration increases due to copper being etched, the ORP goes down, and the etch rate drops slightly. Copper will etch when the ORP rises above 500 mv, and etch rates will increase until 600 mv is reached, when the etch rate levels off (at 600 mv, there is almost no Cu+1 in solution). The change in etch rate over this range is about 0.25 µm per min/ for every 10 mv. Typical ORP controls will hold to within ±10 mv of the setpoint, so the potential change in etch rate is 0.5 µm/min.
However, the etch vs. ORP graph for cupric chloride in this range shows a plateau between 540 mv and 580 mv, where the etch rate remains fairly flat at around 25 µm/min. The best control point for the ORP is 560 mv, where the ORP controller can maintain ±10 mv setpoint with virtually no change in etch rate. Most etchers will have an ORP monitor as standard, but it will cost $15,000–$20,000 to add the equipment needed to make it a controller. If you are contemplating doing high-density circuits, an ORP controller is a must.
ORP monitors can also be useful for alkaline etch, but we will discuss this in more detail next month.
For cupric chloride, the free acid level (HCl) must also be controlled closely. The free acid is necessary to prevent oxide buildup on the copper surface (which slows the etch rate) and to keep the Cu+1 ions in solution. With too little free acid, the Cu+1 ions will precipitate out of solution leading to an inaccurate ORP reading. The recommended operating range for free acid is from 0.5N (18 grams/liter HCl) to 3N (110 gpl HCl). Within this range, the change in etch rate is 0.75 µm per min/ for each 0.1N increase or decrease in free acid content so free acid must be controlled to at least ±0.1 N. An acid controller will mean an additional $8,000–$10,000 to the cost of the etcher but is vitally important for high-density circuits.
Next month, I will continue with more alkaline etchant control issues and controls for developers and strippers.
This column originally appears in the June 2024 issue of PCB007 Magazine.
More Columns from The Chemical Connection
The Chemical Connection: Sales Organization from a Capital Equipment PerspectiveThe Chemical Connection: Through-glass Vias in Glass Substrates
The Chemical Connection: Reducing Defects in Circuit Board Production
The Chemical Connection: Common Misconceptions in Wet Processing
The Chemical Connection: Surface Finishes for PCBs
The Chemical Connection: Earthquakes, Astronauts, and Aquatics—A Lighter Look at the Past
The Chemical Connection: Better Fabs Attract a Better Workforce
The Chemical Connection: Can Changing Spray Nozzles Improve My Etch Quality?