-
- News
- Books
Featured Books
- pcb007 Magazine
Latest Issues
Current IssueIn Pursuit of Perfection: Defect Reduction
For bare PCB board fabrication, defect reduction is a critical aspect of a company's bottom line profitability. In this issue, we examine how imaging, etching, and plating processes can provide information and insight into reducing defects and increasing yields.
Voices of the Industry
We take the pulse of the PCB industry by sharing insights from leading fabricators and suppliers in this month's issue. We've gathered their thoughts on the new U.S. administration, spending, the war in Ukraine, and their most pressing needs. It’s an eye-opening and enlightening look behind the curtain.
The Essential Guide to Surface Finishes
We go back to basics this month with a recount of a little history, and look forward to addressing the many challenges that high density, high frequency, adhesion, SI, and corrosion concerns for harsh environments bring to the fore. We compare and contrast surface finishes by type and application, take a hard look at the many iterations of gold plating, and address palladium as a surface finish.
- Articles
- Columns
Search Console
- Links
- Media kit
||| MENU - pcb007 Magazine
The Value Side of Training, Part 1: Five Easy Ways to Measure the ROI on Training
July 9, 2024 | Mike Hoyt, IPCEstimated reading time: 3 minutes
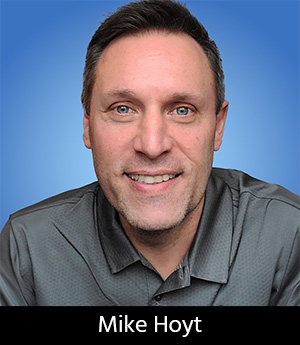
The best thing about a good investment is the yield it provides. This series of articles on the value side of training will focus on how to effectively measure the return on your investment (ROI) when training your staff. I will offer practical, quantifiable metrics you can apply today. Think of it as a quick checklist for every effective training program.
But before we jump into the ROI checklist, here are core principles to consider when it comes to training:
- Training is not a cost; it is an investment
- Not all training is created equal
- Training is not a one-time event
Training is not a cost; it is an investment
This should not be a surprise. For many of you, training is an easy no-brainer. But the opposite is also true, namely the painful results of not training. It’s easy to assume that training is expensive, but let’s not forget how costly and detrimental it is when you don’t invest in something valuable. We can easily quantify into dollars lost the effects of ignorance, poor quality, scrap, and attrition.
Not all training is created equal
It is easy to say, “We already invest in training,” or “That’s why we have a certified IPC trainer.” But let’s be realistic: There are good, bad, and in the middle training programs. Some effective training programs get new hires to proficiency 33% faster than others. While some are very engaging and interactive, others are not. Unfortunately, some training programs simply check the box. They may be outdated and become a negative experience for the learner.
With training programs, it’s important to consider how they perform and evaluate the results. I’m not suggesting changing an effective training program just for the sake of change, but inviting you to be open to new possibilities and better outcomes for the sake of improvement.
Training is not a one-time event
Growth and learning are ongoing processes. At age 88, inventor and artist Leonardo DaVinci said “Ancora imparo” or “I’m still learning.” We all need access to opportunities to personally improve and grow. Believe you can learn something new every day and then apply it to your job and training for all your employees, from entry-level to the C-suite.
In the next few months, I will share five articles on these ROI metrics that you can start using right away in your evaluation:
1. Time to proficiency: How long does it take a trainee to reach an industry-defined level of proficiency? Faster time to production equals more revenue generated and less time in training.
2. Minimal involvement of personnel: How much time do your brightest and smartest employees spend mentoring trainees? How much time are they away from their main responsibilities and from production? Unfortunately, that can hurt your bottom line more than you think.
3. Elimination of error: How much time, personnel, and money is spent on rework, repair, and scrap? How many dollars are lost on unsatisfied customers, especially if they are lost?
4. Mitigation of turnover: How many employees leave each year because training did not help them enough or there are no additional training opportunities for advancement. Think of the time, personnel, and resources that go into the rehiring process.
5. Training content is learned effectively: Using proven educational methods, we are measuring how much a person actually remembers from the training course and can apply to their job. An easy way to measure this is by looking at the quality of their work and whether the trainee had a positive learning experience.
I look forward to sharing more about each of these five areas and helping you build an effective training program that will pay for itself.
Mike Hoyt is the IPC workforce training advisor.
Suggested Items
Bridging the Knowledge Gap in Test: A Conversation with Bert Horner
06/11/2025 | Barry Matties, I-Connect007Bert Horner is a seasoned industry veteran and co-creator of The Test Connection, Inc. (TTCI), a test and inspection company spanning over 45 years. In this candid conversation, Bert reflects on the challenges our industry faces with the retirement of career professionals and the subsequent loss of critical tribal knowledge. As he unveils The Training Connection’s innovative training initiatives, Bert emphasizes the importance of evolving educational programs that align with industry needs, particularly in design for test (DFT), and sheds light on strategies being implemented to foster the next generation of engineers.
IPC Launches New Wire Harness Design Course Led by Defense Industry Expert
06/03/2025 | I-Connect007 Editorial TeamIPC is expanding its educational offerings with a new online course designed to provide foundational knowledge in wire harness and cable design. The course, Introduction to Wire Harness Design I, is led by a seasoned mechanical engineer and subject matter expert in military cable systems working at FNSS Defense Systems in Turkey.
Advint Delivers Advanced Electroplating Training to Triangle Labs
06/02/2025 | Advint IncorporatedDuring the last week of April, Advint Incorporated conducted a comprehensive two-day on-site electroplating training session for the technical team at Triangle Labs, Inc., a key innovator in the printed circuit board space. The training was structured to align with the demands of high-reliability plating processes suitable for RF and high-frequency substrates.
STI Electronics Celebrates Frank Honyotski’s 25 Years of Service
06/02/2025 | STI ElectronicsSTI Electronics, Inc., a full-service organization providing training services, training materials, analytical/failure analysis, prototyping, and contract PCB manufacturing, proudly announces the 25th work anniversary of Frank Honyotski, Master Instructor.
The Knowledge Base: Beyond the Badge—Why Membership Matters More Than Ever
05/28/2025 | Mike Konrad -- Column: The Knowledge BaseMembership in trade associations like the Surface Mount Technology Association (SMTA) offers substantial benefits that can significantly enhance a professional's career in the electronics manufacturing industry. These advantages encompass extensive networking opportunities, access to specialized technical conferences, and complimentary training programs, all contributing to professional growth and industry recognition.