-
- News
- Books
Featured Books
- pcb007 Magazine
Latest Issues
Current IssueSales: From Pitch to PO
From the first cold call to finally receiving that first purchase order, the July PCB007 Magazine breaks down some critical parts of the sales stack. To up your sales game, read on!
The Hole Truth: Via Integrity in an HDI World
From the drilled hole to registration across multiple sequential lamination cycles, to the quality of your copper plating, via reliability in an HDI world is becoming an ever-greater challenge. This month we look at “The Hole Truth,” from creating the “perfect” via to how you can assure via quality and reliability, the first time, every time.
In Pursuit of Perfection: Defect Reduction
For bare PCB board fabrication, defect reduction is a critical aspect of a company's bottom line profitability. In this issue, we examine how imaging, etching, and plating processes can provide information and insight into reducing defects and increasing yields.
- Articles
- Columns
- Links
- Media kit
||| MENU - pcb007 Magazine
Estimated reading time: 7 minutes
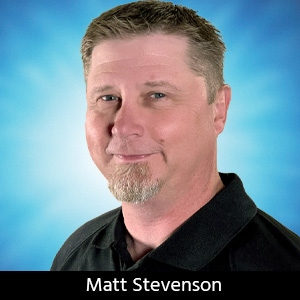
Connect the Dots: Navigating the Intricacies of PCB Drilling
Welcome to another leg on my quest to share best practices associated with designing PCBs for the reality of manufacturing. In a recent episode of the On the Line with... podcast, we discussed the critical role of drilling in the board manufacturing process. That is the subject of this article.
Drilling can be one of the most complex and tricky steps in the manufacturing process. Designers need to be aware of how to craft their designs to avoid problems during drilling that can drive up costs and increase the risk of board performance issues.
Done with the chemical messiness, we put holes in the board. Almost.
Drilling happens after lamination in the multilayer PCB board manufacturing process. Once the lamination process is complete, we have what we call a book: a stack of core layers manufactured into a multilayer PCB. At this stage of production, epoxy has squeezed out from between the layers and the edges are sharp and brittle.
Before drilling can begin, we have to clean the panels and flash around the edges in order to restore the panel’s perfect rectangular shape with smooth edges that are safe to handle. Not unlike using a router in a wood shop, we put the panels on a mechanical router, rout around the edges, and restore the correct panel size.
After that, we verify registration for all those layers, wherever they are in the book. With copper on the top and bottom of the multilayer board, we can’t see what’s already been done, so we need a method to align the holes with images now hidden by the copper.
We use a test board called a coupon to create drill targets for each layer, anticipating that the coupon holes match what is in the rest of the board. The drill is programmed to aim for those targets on every layer and, using an X-ray, calculate best fit for all locations on each layer, hitting all connections and missing clearances.
The drill team, like the designer, has to balance constraints. That is why we consult design notes that can help us with tolerances and drill bit sizes. The more help the designer gives us in the notes, the better we can assess tolerances during the drill process and make good conducting vias.
If it seems like a lot of things can go wrong when drilling a multilayer board, that is because it can. Which brings us to the most important part of the drilling process: Prep.
Sound preparation is at the heart of drilling.
As with much of PCB design and manufacturing, drilling is both a science and an art form. The process requires more than just cutting-edge equipment. To get the job done right, you need experience and expertise in every aspect of production. Both are key to properly preparing to drill holes in boards.
Take the hole sizes on the print as an example. We can’t just drill at the size on the print because, after plating, the hole will be smaller. Adding copper decreases the diameter of the hole so we need to know the amount of copper and surface finish applied at end of the process. A good CAM department will account for anything that goes in the hole and adjust the hole size to account for this, thus ensuring the drilling process finishes with the proper tolerances.
There should also be an open and ongoing conversation with the designer to remove any uncertainty about instructions in the notes. Designers should be prepared to answer questions about hole sizes, vias, and through-hole components, just to name a few.
In addition to the complexities related to design, the drilling process itself offers intangibles. Books aren’t 100% rigid. The inner layers will skew and stretch, creating movement. The drill team has to predict how panels will move so when we drill, it will be accurate. Think of it like a layer cake with frosting in the middle. Things squish around when you mash them together.
This is where the cohesion between the CAM team and the drill team comes into play. The CAM team is responsible not just for identifying the right size bit for the drill machine, but also for predicting layer behavior. The drill team uses the information provided by CAM to align the drill to the inner layers to ensure a functional circuit leaves the drill department.
Now we go ahead and make holes in the board.
But before we start drilling, we have to make a sandwich. When panels are piled atop each other in drill stacks, we place an aluminum entry material on the top and a phenolic material on the bottom of the stack. The top of the sandwich helps dissipate heat and, at the drill point, gives the device a foothold to drill straight. If the material is slick or hard, the bit can skate on the surface before it goes in the board, meaning it can deflect from the target point or go in diagonally, which is clearly not optimal.
There is also a back-up material on the bottom that the drill goes through. Going back in time to high school wood shop again, drilling boards is like drilling wood. If there’s no pressure on the back of the board when the drill comes out, the wood splinters and creates a volcano. It’s the same for boards. Drill movement will blow out the back, so a sacrificial piece of material is critical.
A guide on the top and a catch on the bottom makes for a crisp and accurate hole.
The delicate balance between drill bit size and panel thickness.
Drill bits are really small. An 8-mil bit is thinner than a human hair, so too much lateral pressure can break it or cause a deflection. The relationship between panel thickness and drill hole size is what we call aspect ratio. For example, a 10-mil drill on a 100-mil board creates a hole aspect ratio of 10 to 1.
How far can you throw?
The term throw refers to how deep you can plate into the aspect ratio called out in the design. How much copper can you get to the center of the hole vs. the knee or surface? If the board is too thick for your hole, there is an increased chance of weak connections or no connection at all. Copper expands and contracts a lot, and a thin spot can fracture with exposure to heat. If your board makes it to assembly with thin spots in one or more connections, as it thermal cycles through its useful life, there can be reliability issues and even field failure.
Fewer layers mean there will be less risk of throw issues. With a board of four to six layers, there are rarely throw issues, but how many layers is too many? It depends on the manufacturer. If you keep your design at or below the 10 to 1 example, most fabricators can accommodate that using their standard drilling process.
There is more to consider than just aspect ratio. The board complexity plays a role as well. For a complex design, there could be as many as 25,000 via holes on one panel and take as many as eight hours on the drill machine. As a designer, if you call out 8-mil and 12-mil holes, and they’re spread out, that creates the need for a longer drilling process. If there is more distance between holes, there is more time spent moving and less time spent drilling. The same can be said for multiple hole sizes. Every time we have to change a bit during drilling, everything stops.
We encourage designers to consider the drilling process carefully and optimize their designs to make it more efficient. If, for example, vias can be combined to a singular size, we spend less time on drill setup and bit changes. Designs with fewer hole sizes and similarly sized holes grouped together are cheaper to produce and yield better results.
Drilling is a critical part of the manufacturing process. Hole quality needs to be great and getting there starts with a design optimized for drilling.
This column originally appeared in the July 2024 issue of Design007 Magazine.
Download The Printed Circuit Designer’s Guide to… Designing for Reality by Matt Stevenson. You can view other titles in the I-007eBooks library.
More Columns from Connect the Dots
Connect the Dots: The Future of PCB Design and ManufacturingConnect the Dots: Proactive Controlled Impedance
Connect the Dots: Involving Manufacturers Earlier Prevents Downstream Issues
Connect the Dots: Stop Killing Your Yield—The Hidden Cost of Design Oversights
Connect the Dots: Designing for Reality—Routing, Final Fab, and QC
Connect the Dots: Designing for Reality—Surface Finish
Connect the Dots: Designing for Reality—Solder Mask and Legend
Connect the Dots: Designing for Reality: Strip-Etch-Strip