Maximizing ROI Through Better Wet Process Control
August 20, 2024 | I-Connect007 Editorial TeamEstimated reading time: 2 minutes
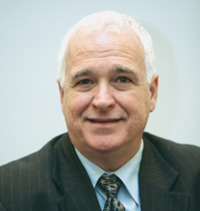
Mike Carano is a program manager and SME for advanced packaging and PCB technologies at Trusted Semiconductor Solution. He has more than 40 years of experience in the electronics industry, with special expertise in manufacturing, performance chemicals, metals, semiconductors, medical devices, and advanced packaging.
For this issue, we reached out to Mike to learn more about how dialing in on wet process can benefit your bottom line.
“When things get out of control, the variation in your wet process begins,” Mike says. “Just because they look like good boards and may even pass electrical test, it does not necessarily mean you have good boards. Once the chemistry is headed toward the right or left side of the process control parameter cliff, the plating is compromised. If the copper is thinner than it should be, when the customer puts it into service, the board may fail after 500 cycles vs. the requisite 1,000 or 2,000 cycles. The root cause issue is that you plated 7/10ths of a mil of copper instead of one-mil of copper because you were not controlling your process. The fact that you passed your own electric test becomes inconsequential.”
What he’s really talking about is the need for a paradigm shift “where tight control of your processes is the way you manage your organization, wet process being one particular and crucial area of operations.”
With respect to process control, he tells his clients, “you have to stop thinking like a fabricator and think more like a semiconductor company.” Don't be solely reliant on your suppliers’ technical support to do the job either, he adds, because by then, it could be too late. “We all need to be laser-focused on precision. We need to be better at what we do. Perfection may not be attainable, but we should strive to get as close as we can. You achieve that through process control, which encompasses the critically essential skills of troubleshooting, root-cause analysis, problem-solving, and strategizing.
Marcy LaRont: Mike, PCB fabricators care about quality and yield because it ultimately translates to cost and profitability. Today, we also have sustainability goals and requirements. What should be the priorities in tightening up control?
Mike Carano: It has been frustrating over the years to witness the general lack of ability to troubleshoot and solve problems in some of the places I visit, which is why I write articles and present courses on advanced troubleshooting. I often see a “teeter-totter” mindset, this conundrum that you must sacrifice either quality or productivity and that somehow you can’t have both. Of course, the manufacturing folks err toward greater productivity, so you always have control over all your processes in real-time. Things will always go wrong. But when you simply rely on mass inspection, and don’t focus on process control, costs and rework go up, and productivity ultimately declines, all because of an imperfect system.
To read the rest of this article, which appeared in the August 2024 issue of PCB007 Magazine, click here.
Testimonial
"The I-Connect007 team is outstanding—kind, responsive, and a true marketing partner. Their design team created fresh, eye-catching ads, and their editorial support polished our content to let our brand shine. Thank you all! "
Sweeney Ng - CEE PCBSuggested Items
Advint and SanRex Expand High-Performance DC Rectifier Access for North American PCB Fabricators
08/12/2025 | Advint IncorporatedAdvint Incorporated has entered a strategic partnership with SanRex Corporation, enhancing access to industrial-grade DC rectifiers for the US printed circuit board industry. With a legacy of power innovation and performance across the globe, SanRex rectifiers are available through Advint’s proficient distribution network.
Advint and Sayron Bring Advanced Rectifier Solutions to High-Reliability PCB Manufacturers
08/01/2025 | Advint IncorporatedAdvint Incorporated has partnered with Sayron, a leading global rectifier manufacturer, to supply cutting-edge IGBT-based DC rectifiers to high-performance PCB manufacturers across North America and beyond. Sayron’s precision-engineered rectifiers align with the stringent requirements of advanced PCB processes.
Trouble in Your Tank: Metallizing Flexible Circuit Materials—Mitigating Deposit Stress
08/04/2025 | Michael Carano -- Column: Trouble in Your TankMetallizing materials, such as polyimide used for flexible circuitry and high-reliability multilayer printed wiring boards, provide a significant challenge for process engineers. Conventional electroless copper systems often require pre-treatments with hazardous chemicals or have a small process window to achieve uniform coverage without blistering. It all boils down to enhancing the adhesion of the thin film of electroless copper to these smooth surfaces.
Magnalytix’s Dr. Mike Bixenman to Guide PDC at SMTA High-Reliability Cleaning and Conformal Coating Conference
07/31/2025 | MAGNALYTIXMagnalytix, providing real-time reliability solutions for electronics manufacturing, is excited to announce that Dr. Mike Bixenman will present the professional development course “The Effects of Flux Residues and Process Contamination on the Reliability of the Electronic Assembly” on Wednesday, Aug. 13 at 9:00 AM CST to open the second day of the STMA High-Reliability Cleaning and Conformal Coating Conference.
Setting Design Constraints Effectively
07/31/2025 | Stephen V. Chavez, Siemens EDAPCB design requires controlling energy within the medium of a PCB. The manner in which we control the chaos of energy is by implementing and utilizing physical and electrical rules, known as constraints, along with a specific structure and material(s) that make up what is known as the foundation of the design. These rules govern everything within the PCB structure and generally fall into two camps: performance and manufacturability. Setting this foundation correctly is extremely important and the key to success.