Estimated reading time: 5 minutes
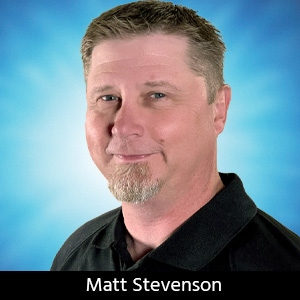
Connect the Dots: Designing for Reality—Electroless Copper
Roll up your sleeves because it's time to get messy. In a recent episode of I-Connect007’s On the Line with… podcast, we discussed electroless copper deposition. This process deposits a copper layer into the through-holes and vias of what will eventually be a PCB.
Electroless copper deposition feels like a black box to many people. It sort of looks like a black box, too. The boards go in one side, come out the other, and emerge differently. So, let's crack open that black box and look inside.
This manufacturing step involves a chemical deposition of copper. Specifically, it is a chemical-catalyzed deposition of copper, mainly to the epoxy inside the holes. Electroless differs from electrolytic in that electrolytic deposition relies on electricity. However, there is too much insulating material in the different layers of the PCB for electrolytic processes to work in through-holes.
Without electroless copper deposition, boards later end up with voided copper holes in the manufacturing process. Understandably, this preparatory step is critical for the manufacturer to get right. When done correctly, it creates a very fine layer of copper that makes the connection from top to bottom through the through-hole. Since this thin layer of copper is conductive, it allows a later electrolytic process to deposit a more thorough layer of copper.
Preparing for Electroless Copper
This step isn’t simply spraying a bit of copper in the holes. It is a multi-chemical process that involves many chemical baths, rinses, and other processes. To prepare for this step, the manufacturer first needs to clean up the residue left behind by the drilling process.
The challenge is that drilling creates heat. This tends to melt and possibly smear epoxy over the internal copper connections of the circuit board. Smeared epoxy creates a possible insulator between copper connections and the through-hole, eliminating or making an unreliable connection. The manufacturer needs to remove these smears chemically. It’s called the de-smear process. This results in a uniform, clean surface—perfect for the application of electroless copper.
Next, we remove other remnants from the drill process. The drill can sometimes produce copper burs on the surface, like when drilling through a 2×4. Any bumps or protrusions need to be removed. Maintaining the smooth surface plane throughout this process is crucial. We use a mechanical scrub to remove these irregularities on the surface created by the drilling process.
Designers may have concerns about rough surfaces left by this step, primarily because the scrub uses a nylon brush to roughen both sides of the panel surface. Copper is porous but very smooth. It needs to be roughened to get good adhesion during the dry film lamination process. Copper roughening is a great equalizer to keep the adhesion of the dry film photoresist during the plating processes.
Time for Electroless
After being de-smeared, smoothed, and roughened, the boards go into the baskets that enter the electroless copper process. They first go into a chemical bath to help slightly swell the epoxy. As it swells, it becomes more porous, allowing the copper and catalyst to enter. When the swelling decreases, it has a more uniform copper coverage.
The catalyst is a palladium-based process. Palladium is not cheap, but it works very well. A catalyst initiates a reaction but is not consumed. The catalyst gets into all the through-holes and deposits in the epoxy. Later, the palladium will attract the copper ions in the electroless copper bath and act as a nucleation site for a reaction to occur. The copper bonds to the palladium, creating a copper layer about 30 to 70 micro-inches thick.
Two forces act against the copper plating. First, all the air needs to be removed from the through-holes. Manufacturers use mechanical processes such as vibration, thumping, and agitation to increase the fluid flow through the holes and move the air out. There are other tricks to help break the surface tension and increase the opportunity for getting copper in all those holes. If you fail to get copper in every hole, it creates a void, which may lead to a missed connection later, which means a scrapped panel.
Another potential challenge to the electroless copper process is in the aspect ratio—the thickness of the panel to the smallest drill size. For example, a 100-mil thick panel with a 10-mil drill creates a 10:1 aspect ratio. This is common and shouldn't challenge too many manufacturers. But as you get thicker panels and smaller holes together, the increased aspect ratio becomes more problematic. Eventually, manufacturers must rely on capillary action to get fluid in and out of the holes.
However, capillary action won't be enough. Once you place the solution in the hole, you need to continually replace it to ensure enough copper is in contact with the catalyst. Getting the hole wet once is good, but you need to replenish that action. Mechanical processes are used to get fluid through the holes numerous times to produce a thick enough coating.
The copper needs to be thick enough to survive the pre-clean processes and the initial dunking of panels into a sulfuric acid bath, which happens later in the manufacturing process. Portions of the pre-clean process will etch copper away if uninhibited. Enough copper must remain after those processes to ensure adequate electrical conduction for electroplating.
Electroless Copper Design Considerations
If the electroless copper deposit goes wrong, voids in through-holes could cause manufactured PCBs to end up in the scrap heap. Luckily, designers can consider this possibility when designing for the reality of manufacturing. To avoid problems during this process, use the largest vias possible. While there are sometimes good reasons to use micro-vias and high aspect ratio holes, aim for a 10:1 aspect ratio or smaller. The smaller the aspect ratio, the better the chances the boards will be reliable long-term and properly yielded to minimize costs.
To learn more about designing for the reality of the PCB manufacturing process, check out more episodes of On the Line with….
Download The Printed Circuit Designer’s Guide to… Designing for Reality by Matt Stevenson. You can view other titles in the I-007eBooks library.
This column originally appeared in the August 2024 issue of Design007 Magazine.
More Columns from Connect the Dots
Connect the Dots: Proactive Controlled ImpedanceConnect the Dots: Involving Manufacturers Earlier Prevents Downstream Issues
Connect the Dots: Stop Killing Your Yield—The Hidden Cost of Design Oversights
Connect the Dots: Designing for Reality—Routing, Final Fab, and QC
Connect the Dots: Designing for Reality—Surface Finish
Connect the Dots: Designing for Reality—Solder Mask and Legend
Connect the Dots: Designing for Reality: Strip-Etch-Strip
Connect the Dots: Designing for Reality—Pattern Plating