-
-
News
News Highlights
- Books
Featured Books
- pcb007 Magazine
Latest Issues
Current IssueThe Hole Truth: Via Integrity in an HDI World
From the drilled hole to registration across multiple sequential lamination cycles, to the quality of your copper plating, via reliability in an HDI world is becoming an ever-greater challenge. This month we look at “The Hole Truth,” from creating the “perfect” via to how you can assure via quality and reliability, the first time, every time.
In Pursuit of Perfection: Defect Reduction
For bare PCB board fabrication, defect reduction is a critical aspect of a company's bottom line profitability. In this issue, we examine how imaging, etching, and plating processes can provide information and insight into reducing defects and increasing yields.
Voices of the Industry
We take the pulse of the PCB industry by sharing insights from leading fabricators and suppliers in this month's issue. We've gathered their thoughts on the new U.S. administration, spending, the war in Ukraine, and their most pressing needs. It’s an eye-opening and enlightening look behind the curtain.
- Articles
- Columns
- Links
- Media kit
||| MENU - pcb007 Magazine
Young Professionals Spotlight: Process Engineer Kevin Dial, American Standard Circuits
September 5, 2024 | Dan Beaulieu, D.B. Management GroupEstimated reading time: 2 minutes
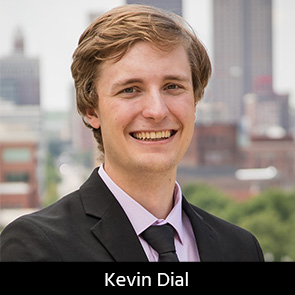
When I heard that my friends at American Standard Circuits had hired a new, fresh-out-of-college process engineer, I was anxious to meet him. Now, you get to read this interview. It’s a rare perspective of a young man new to our industry.
Dan Beaulieu: Kevin, tell me about your journey to America Standard, and what is your position now with ASC?
Kevin Dial: I joined ASC as a wet process engineer in the summer of 2022 after graduating from the University of Iowa. It’s hard to believe two years flew by that quickly, but here we are.
Beaulieu: You’re becoming a veteran by now. What are your daily responsibilities?
Dial: My biggest focus is on circuit formation steps, including imaging, via plating, and etching. Then, I monitor results through AOI and ET. It is a wide-ranging mandate where I can design controls for critical processes and investigate fascinating chemistry. The process engineering team is also putting a lot of effort into refining our registration control scheme from post-etch punch to primary drill tooling. Our exotic material sets often demand that we dig deep into the first principles of a challenge and deploy engineering tools in thoughtful, unique ways. The job generally boils down to constructing flexible, resource-efficient processes that execute our diverse, high-technology product mix.
Beaulieu: What is your background?
Dial: I am a trained chemical engineer with a minor in business administration. The curriculum balanced my interests in industrial process design, undergraduate electrochemical research, and the fundamentals of business organizations. My undergraduate thesis project was a modular gas-to-liquids hydrocarbon synthesis unit that could be transported between decommissioned oil wells to capture methane into useful products. It won a national student team design competition, one of my proudest professional achievements.
Beaulieu: What drew you to ASC?
Dial: As a problem solver, growth only happens outside one’s comfort zone. Three years ago, I couldn’t pick a PCB out of a police lineup, but I was intrigued by all the unfamiliar chemical processes. I figured I could use my background in electroplating as a launch point into the electro-, photo-, and thermal chemistry I didn’t know. I also saw a tight-knit, experienced engineering team that could support my inquiries. The first couple of months were like drinking out a firehose and probably the most educational experience of my life.
Beaulieu: Were you drawn at all by the technology?
Dial: Yes, 100%. Learning PCBs was one thing, but learning our technology set is entirely different. Understanding the unique challenges of running such a diverse set of thermal management solutions, RF/microwave designs, mixed-material builds, embedded passive components, and HDI features is a continuous process that keeps me excited to come to work every day. Every panel is an engineering marvel.
To read this entire conversation, which appeared in the August 2024 issue of PCB007 Magazine, click here.
Suggested Items
SMT007 Magazine July—What’s Your Competitive Sweet Spot?
07/01/2025 | I-Connect007 Editorial TeamAre you in a niche that’s growing or shrinking? Is it time to reassess and refocus? We spotlight companies thriving by redefining or reinforcing their niche—what are their insights? In the July 2025 issue of SMT007 Magazine, we spotlight companies thriving by redefining or reinforcing their niche and offer insights to help you evaluate your own.
Smarter Machines Use AOI to Transform PCB Inspections
06/30/2025 | Marcy LaRont, PCB007 MagazineAs automated optical inspection (AOI) evolves from traditional end-of-process inspections to proactive, in-line solutions, the integration of AI and machine learning is revolutionizing defect reduction and enhancing yields, marking a pivotal shift in how quality is managed in manufacturing.
Magnalytix and Foresite to Host Technical Webinar on SIR Testing and Functional Reliability
06/26/2025 | MAGNALYTIXMagnalytix, in collaboration with Foresite Inc., is pleased to announce an upcoming one-hour Webinar Workshop titled “Comparing SIR IPC B-52 to Umpire 41 Functional & SIR Test Method.” This session will be held on July 24, 2025, and is open to professionals in electronics manufacturing, reliability engineering, and process development seeking insights into new testing standards for climatic reliability.
The Death of the Microsection
06/26/2025 | Bob Neves, Reliability Assessment Solutions, Inc.I got my start out of college grinding and polishing PCB microsections. My thumbs are a bit arthritic today because of the experience (microsection grinders know what I mean). Back then, via structures were rather large, and getting to the center in six steps of grinding and polishing was easy compared to what my team has been doing recently at the lab.
Specially Developed for Laser Plastic Welding from LPKF
06/25/2025 | LPKFLPKF introduces TherMoPro, a thermographic analysis system specifically developed for laser plastic welding that transforms thermal data into concrete actionable insights. Through automated capture, evaluation, and interpretation of surface temperature patterns immediately after welding, the system provides unprecedented process transparency that correlates with product joining quality and long-term product stability.