Altus Group Introduces Innovative BGA Reballing Solution to Meet Growing Sustainability Demands
September 25, 2024 | Altus GroupEstimated reading time: 1 minute
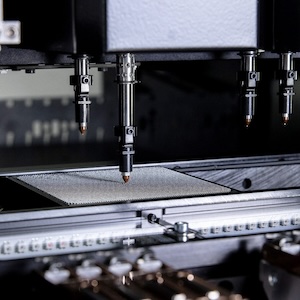
Altus Group, a leading distributor of capital equipment in the UK and Ireland, has introduced an advanced BGA re-balling solution to address the electronics industry's growing focus on sustainability and cost-efficiency. Developed by their pre-eminent supplier, Essemtec, this innovative process offers manufacturers a new approach to component recovery and reuse, aligning with increasing market demands for environmentally conscious practices.
Building on their expertise in adaptive SMT equipment, Essemtec has designed a cutting-edge BGA re-balling process that consolidates flux deposition, ball placement, and soldering into a single streamlined solution. This all-in-one approach is particularly advantageous for high-volume OEMs and companies in sectors such as military, aerospace, computing, and communication, providing a cost-effective and sustainable method for component recovery and reuse.
Jiri Kucera, Operations Director at Altus Group, said: "Reworking BGAs, recovery of expensive parts, and re-use is becoming a highly discussed topic across the electronics industry as consumers become more interested in sustainability. This is another example of Essemtec developing a process to meet the needs of the market."
The new robotic process offers several advantages over traditional manual methods:
1. Increased precision and reliability.
2. Support for various ball sizes (250 µm to 1 mm+) and materials.
3. Improved success rates compared to manual stencil techniques.
4. Cost-effective reuse of expensive BGA components.
Jiri added, "Companies are already using the Essemtec jetting unit for BGA re-balling across a range of pitched components, giving partners the power to bring some of the recovery processes back in-house rather than outsource to partners at a higher cost."
This solution is particularly relevant for organisations prioritising environmental impact and sustainability. By extending the lifecycle of electronic components, the process contributes to waste reduction and promotes a more circular economy in electronics manufacturing.
Altus sees this technology as a significant step in meeting the electronic industry's evolving needs. As sustainability continues to gain importance, solutions like this will play a crucial role in shaping the future of electronics manufacturing and repair.
Suggested Items
Keysight, Synopsys Deliver an AI-Powered RF Design Migration Flow
06/06/2025 | BUSINESS WIREKeysight Technologies, Inc. and Synopsys, Inc. introduced an AI-powered RF design migration flow to expedite migration from TSMC’s N6RF+ process to N4P technology, to address the performance requirements of today’s most demanding wireless integrated circuit applications.
IPC Releases Latest Standards and Revisions Updates
06/05/2025 | IPCEach quarter, IPC releases a list of standards that are new or have been updated. To view a complete list of newly published standards and standards revisions, translations, proposed standards for ballot, final drafts for industry review, working drafts, and project approvals, visit ipc.org/status. These are the latest releases for Q1 2025.
STARTEAM GLOBAL Unveils Innovative Additive Solder Mask Process
06/02/2025 | STARTEAM GLOBALSTARTEAM GLOBAL, a leading PCB manufacturer, has introduced a revolutionary additive solder mask process at its Flero STARTEAM (FST) factory in Italy, leveraging digital inkjet technology to enhance production efficiency and sustainability.
Advint Delivers Advanced Electroplating Training to Triangle Labs
06/02/2025 | Advint IncorporatedDuring the last week of April, Advint Incorporated conducted a comprehensive two-day on-site electroplating training session for the technical team at Triangle Labs, Inc., a key innovator in the printed circuit board space. The training was structured to align with the demands of high-reliability plating processes suitable for RF and high-frequency substrates.
The Chemical Connection: Reducing Defects in Circuit Board Production
06/04/2025 | Don Ball -- Column: The Chemical ConnectionWe all agree that in any manufacturing process, reducing defects in your product induced during manufacture (aka increasing yields) is a good thing. Doing so, however, can be a source of contention and frustration. I don’t pretend to be an expert in this field, because most of my work involves feasibility studies for new concepts or testing improvements made to existing equipment. High yields were usually not a factor; it’s simply about having enough data to prove or disprove a concept or seeing whether improvements to equipment design actually work. However, here are some observations I made visiting quality shops where high production at high yields was important.