Northrop Grumman to Produce First Hypersonic Glide Phase Interceptor
September 30, 2024 | Northrop GrummanEstimated reading time: 1 minute
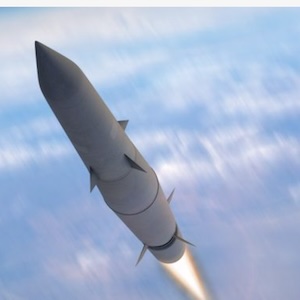
The U.S. Missile Defense Agency (MDA) will proceed with Northrop Grumman Corporation for the Glide Phase Interceptor (GPI) program, the first-of-its-kind defensive countermeasure against hypersonic missile threats. Working in close partnership with MDA, the three-year developmental effort produced a purpose-built, innovative design capable of defeating existing and emerging hypersonic threats.
During this next phase of development, Northrop Grumman will:
- Continue to refine the preliminary design of the GPI, which will fire from the U.S. Navy’s Aegis Ballistic Missile Defense destroyers and Aegis Ashore using the standard Vertical Launch System
- Demonstrate system performance in hypersonic environments prior to conducting its Preliminary Design Review
- Complete flight experiments ahead of schedule leveraging the company’s own flight-proven systems
- Use digital engineering practices to connect the entire GPI program to accelerate design processes and develop interceptor capabilities faster and more efficiently
Expert:
Wendy Williams, vice president and general manager, launch and missile defense systems, Northrop Grumman: “GPI adds mission critical standoff to warfighters in scenarios where distance creates an advantage. Tailorable to a multitude of mission requirements, Northrop Grumman’s revolutionary solution is designed to perform in the evolving threat landscape.”
Details:
Northrop Grumman’s design includes advanced technologies, such as a seeker for threat tracking and hit-to-kill accuracy, a re-ignitable upper stage engine used for threat containment and a dual engagement mode to engage threats across a wide range of altitudes.
Northrop Grumman will work closely with the United States in support of its role under the GPI Cooperative Development program with the Japan Ministry of Defense to deliver interceptors to the MDA.
Testimonial
"Our marketing partnership with I-Connect007 is already delivering. Just a day after our press release went live, we received a direct inquiry about our updated products!"
Rachael Temple - AlltematedSuggested Items
Flexible Circuit Technologies to Host Free Flex Heater Webinar
08/18/2025 | Flexible Circuit TechnologiesGlobal Supplier of flexible circuits, flex design services, and assembly/box-build services, Flexible Circuit Technology will host their latest webinar, "Thermal Precision Meets Flexibility: The Technology Behind Heater Circuits" on Tuesday, August 26th, 2025 at 11 AM EDT.
Global PCB Connections: Understanding the General Fabrication Process—A Designer’s Hidden Advantage
08/14/2025 | Markus Voeltz -- Column: Global PCB ConnectionsDesigners don’t need to become fabricators, but understanding the basics of PCB fabrication can save you time, money, and frustration. The more you understand what’s happening on the shop floor, the better you’ll be able to prevent downstream issues. As you move into more advanced designs like HDI, flex circuits, stacked vias, and embedded components, this foundational knowledge becomes even more critical. Remember: the fabricator is your partner.
The Art and Science of PCB Floor Planning: A Comprehensive Guide
08/14/2025 | Cory Grunwald and Jeff Reinhold, Monsoon SolutionsPCB design is an intricate and crucial part of developing electronic products. One of the foundational stages of PCB design is floor planning, a phase where the placement of components and the flow of signals are meticulously mapped out. A good floor plan ensures that the PCB performs well, is easy to manufacture, and meets all mechanical and electrical requirements. We’ll explore the essential aspects of floor planning, from its objectives and process to the challenges that designers face.
EnSilica Establishes New EU Mixed-Signal Design Centre in Budapest, Hungary
08/12/2025 | EnSilicaThe facility strengthens EnSilica’s presence in the European Union and taps into Budapest’s deep technology ecosystem, which hosts numerous leading automotive and industrial multinationals. This expansion will increase the Group’s global headcount to around 210 employees.
Happy’s Tech Talk #41: Sustainability and Circularity for Electronics Manufacturing
08/13/2025 | Happy Holden -- Column: Happy’s Tech TalkI attended INEMI’s June 12 online seminar, “Sustainable Electronics Tech Topic Series: PCBs and Sustainability.” Dr. Maarten Cauwe of imec spoke on “Life Cycle Inventory (LCI) Models for Assessing and Improving the Environmental Impact of PCB Assemblies,” and Jack Herring of Jiva Materials Ltd. spoke on “Transforming Electronics with Recyclable PCB Technology.” This column will review information and provide analysis from both presentations.