Estimated reading time: 4 minutes
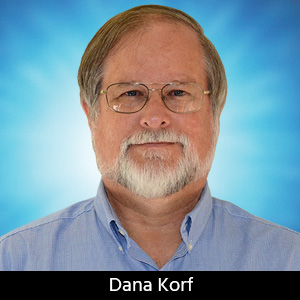
Dana on Data: Resurrecting IPC Class 1
IPC specifications and guidelines have been the standard performance, quality, acceptance, and design basis for PCB designs for approximately two generations. They have proven to be conservative enough that PCBs far exceed their expected lifetimes in a multitude of environments. Requirements are continually adjusted to reflect improvements in materials and process capability that match the increasing component, interconnect, and cost reduction demands.
Operational environments are classified into three well-established classes: 1, 2, and 3. Each class provides increased longer-term reliability in increasingly harsher operating environments and life/service critical applications. Over time these classifications have been informally, and formally, utilized per the following:
- Class 1: As far as I can tell, nobody uses this class.
- Class 2: Default class for conventional applications.
- Class 2.5: This is the Class number that I have invented to reflect many industries that specify Class 2 performance along with key Class 3 requirements, such as plated through-hole plating thickness and annular ring, without several Class 3 coupons or testing requirements.
- Class 3: This has several sub-classes that are tailored to end product applications, including automotive, space, and medical. These sub-classes tighten the quality requirements to improve PCB reliability for the indicated applications environmental conditions.
Are We Too Conservative?
In a previous column, I mentioned my iPod, which is still operational after 22 years. However, I suspect that the intended lifetime was significantly less than this, probably more like three to five years. I have several other electronics devices that are also still operational after 20–40 years.
One could conclude that the PCB requirements are most likely too conservative. We need to challenge and question some of the default requirements:
- Dielectric materials: Could a lower grade of material be used? Can we combine several overlapping technical slash sheets? Do small/thin boards need the same mechanical strength that large/thick PCBs require?
- Copper conductors: Can standard copper thicknesses be reduced by 20–25% at a lower cost?
- PCB thickness: The default PCB thickness is generally 0.062". Could it now be reduced to 0.040" for double-sided to eight layers to reduce material use while maintaining required mechanical strength?
- PCB size/volume: Can the mechanical strength requirements for thin/small PCBs be relaxed below those required for thick/large PCBs? Single-sided materials are available for single-sided and double-sided applications.
- Reflow/rework temperature: Can material Td (time to delamination) be reduced and cost reduced to satisfy 245°C versus 260°C reflow temperatures?
- Reflow/rework cycles: Can materials cost be reduced to only survive two to three soldering cycles, versus six to 10, for low-density/short lifetime products?
- Surface finish: Default all Class 1 and 2 boards to use OSP instead of ENIG gold surface finishes to reduce cost. The gold surface finishes can be the predominate cost factor, along with edge routing, for small boards.
Allow Class 1 Requirements for Prototype and Proof-of-concept Models
Many protypes and proof-of-concept boards will never be shipped to a customer. They may have a limited lifetime in a lab during several debug cycles. These may also be built in small volumes to provide hardware for software development. They aren’t expected to survive in the end product environmental conditions since they will remain in the lab.
Class 1 prototype and proof-of-concept limited use boards can use the same design rules and materials as the production boards. The quality requirements can be relaxed to reduce the production cycle time and cost. Examples are:
Material: The prototype manufacturer is allowed to use materials in stock vs. the production supplier materials when IPC slash sheet specified materials are on the drawings.
Impedance: Two general methods are allowed for impedance validation. The most common is the Impedance TDR test. This requires a human to manually test the various impedances on each layer on a panel-based coupon or within the active PCB. This takes time and money. The second method is called “controlled construction.” This method measures the PCB thickness, copper thickness, and line widths gathered from process control coupons to confirm that the impedance model was built correctly. This should provide sufficient quality validation for a Class 1 board. The production Class 2 boards can require the TDR testing.
- Annular ring: Relax the annular ring requirement to allow for wider process variations. Let the electrical continuity and isolation testing validate the connectivity.
- Plated through-hole plating thickness: Allow Class 2 plating thicknesses for Class 3 boards as long as the prototype build will not be subjected to environmental thermal testing.
- Cosmetic anomalies: Do not reject boards that have cosmetic defects as long as they don’t affect the circuit functionality or assembly. Class 1 prototype boards are generally not intended to be shipped to end customers.
PCB designers, NPI team leaders, and product design engineers should consider relaxing the Class 2 requirements to Class 1 requirements for initial prototype and proof-of-concept revisions to reduce their NPI cost and schedule. Shorter lifetime products need to work with IPC to optimize Class 1 requirements to optimize their cost structure.
Dana Korf is the principal consultant at Korf Consultancy LLC.
More Columns from Dana on Data
Dana on Data: Best Practices in Interpreting Drawing Notes—‘Use Latest Revision’Dana on Data: The Missing AI-NPI Link
Dana on Data: Merging 2D Electrical, 3D Mechanical Worlds
Dana on Data: The Evolution of Fabrication Drawing
Dana on Data: The Insane PCB DFM Process
Dana on Data: eCAD PCB Design Deficiencies
Dana on Data: Nuke the Netlist
Dana on Data: Simplify PCB Documentation