-
- News
- Books
Featured Books
- pcb007 Magazine
Latest Issues
Current IssueInventing the Future with SEL
Two years after launching its state-of-the-art PCB facility, SEL shares lessons in vision, execution, and innovation, plus insights from industry icons and technology leaders shaping the future of PCB fabrication.
Sales: From Pitch to PO
From the first cold call to finally receiving that first purchase order, the July PCB007 Magazine breaks down some critical parts of the sales stack. To up your sales game, read on!
The Hole Truth: Via Integrity in an HDI World
From the drilled hole to registration across multiple sequential lamination cycles, to the quality of your copper plating, via reliability in an HDI world is becoming an ever-greater challenge. This month we look at “The Hole Truth,” from creating the “perfect” via to how you can assure via quality and reliability, the first time, every time.
- Articles
- Columns
- Links
- Media kit
||| MENU - pcb007 Magazine
Estimated reading time: 4 minutes
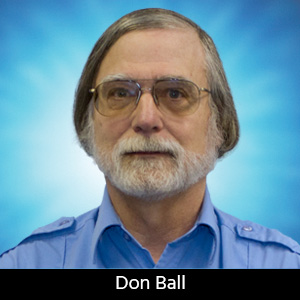
The Chemical Connection: How We Deal With a Technology Roadmap
Ideally, we would all be aware of what future technology demands will be, at least for the near future, and take steps to be prepared to meet those demands. For most of us, however, while we may be aware of what’s coming in terms of production requirements, we usually don’t do much to get ready for them until we’re forced to by the market. We generally don’t have the time or personnel to spend on detailed planning or money to purchase any new equipment before it’s needed. So, how do most of us deal with it?
Like other equipment and chemistry suppliers, our impetus for change comes almost entirely from our customers. As your customers’ demands increase due to new technologies, one of your first instincts will be to turn to your suppliers and ask, “Can we do this?” In many cases the answer is “yes,” and directions can be given to accomplish the desired task. If the answer is “no” or “I don’t know,” then the supplier has a pretty good idea of the direction he needs to go to improve his product and increase his business. This is basically a reactive rather than a proactive process for change because most of us do not have the means to spend the time and money necessary to be proactive.
At this point, I can only speak about how my own company has gone about creating its own roadmap for future development. For the most part, the roadmap has been steady and consistent over the years, although there have been some missteps along the way. Early on, in addition to building equipment, we set up a photochemical machining business in the same building. This turned out to be a not-so-good idea as some potential customers resented it, feeling like they were having to compete with us for business while we were simultaneously trying to get them to purchase our equipment. Later on, we tried to develop controls for more efficient oil-fired home furnaces—after all, how many etchers could you possibly sell once the initial demand was satisfied? This proved to be an effort in futility as much larger and better-known companies had that market pretty well sewn up. There have been many other temptations over the years to expand into related wet processing areas, such as screen printers, semi- and fully-aqueous cleaners for assembled boards, etc. These efforts died away after short periods of time and taught us that the time and money were better used to improve and develop our core business. This has been an important part of our business roadmap for at least two decades.
One part of the early roadmap that paid (and still pays) great dividends has been establishing a small area with demo equipment to familiarize potential customers with the subtractive etching process. This has developed into a separate customer and development lab that is a major driver in shaping our roadmap for improving existing technology and preparing to meet the challenges faced by new technological demands. As our customers run into production problems caused by increasing technological demands, they consult with us on how they can best use their existing equipment to meet those demands. In this way, we become aware of what problems are coming and can determine what direction to take to refine existing designs or decide if a new design is required. We can test any proposed solutions and try out new designs before introducing them to our product line, and have some confidence that the proposed solutions and designs actually work.
The development lab has become an integral part of our business roadmap and keeps us on a (mostly) straight path. It’s not inexpensive, and questions are raised every couple of decades as to whether the expense is worth it. After all, it is hard to quantify the value, i.e., we spent X amount of dollars this year on the lab, but how many dollars of business did it generate? However, in one case, a simple lab test run generated several million dollars in the glass etching business (most people are astonished at how much glass etching is done in the manufacturing of display screens, both TV and phones). Thankfully, examples like this come up often enough to quiet the doubters.
We are fortunate to have this tool in our arsenal since most companies have nothing comparable to this to determine the straightest path to traverse the problems ahead. Many of your suppliers may have similar programs in place and it certainly won’t hurt to keep in touch with them and keep up with the newest refinements. One of our customers, who I have great respect for, is constantly in touch with their suppliers for advice on refining and optimizing their equipment and processes. They have been able to weather the storms of technological challenges fairly smoothly without spending a lot of time and expense on new processes and equipment.
In closing, I’d like you to reflect on the fact that the basic process for manufacturing printed circuit boards has not changed all that much in 75 years. We still put a protective coating on the parts of the metal we wish to save and spray an etchant onto the board to remove the metal we don’t want to save. There have been no major technical innovations in the production methods—just improvements and refinements in those methods. There will come a time when technical requirements for PCB manufacturing will be beyond the capabilities of subtractive etching but that time is still some way off.
This column originally appeared in the September 2024 issue of PCB007 Magazine.
More Columns from The Chemical Connection
The Chemical Connection: Sales Organization from a Capital Equipment PerspectiveThe Chemical Connection: Through-glass Vias in Glass Substrates
The Chemical Connection: Reducing Defects in Circuit Board Production
The Chemical Connection: Common Misconceptions in Wet Processing
The Chemical Connection: Surface Finishes for PCBs
The Chemical Connection: Earthquakes, Astronauts, and Aquatics—A Lighter Look at the Past
The Chemical Connection: Better Fabs Attract a Better Workforce
The Chemical Connection: Can Changing Spray Nozzles Improve My Etch Quality?