-
- News
- Books
Featured Books
- smt007 Magazine
Latest Issues
Current IssueSpotlight on India
We invite you on a virtual tour of India’s thriving ecosystem, guided by the Global Electronics Association’s India office staff, who share their insights into the region’s growth and opportunities.
Supply Chain Strategies
A successful brand is built on strong customer relationships—anchored by a well-orchestrated supply chain at its core. This month, we look at how managing your supply chain directly influences customer perception.
What's Your Sweet Spot?
Are you in a niche that’s growing or shrinking? Is it time to reassess and refocus? We spotlight companies thriving by redefining or reinforcing their niche. What are their insights?
- Articles
- Columns
- Links
- Media kit
||| MENU - smt007 Magazine
Untapped Potential: Automating Warehouse Management Into the Present
October 15, 2024 | Josh Casper, Horizon SalesEstimated reading time: 2 minutes
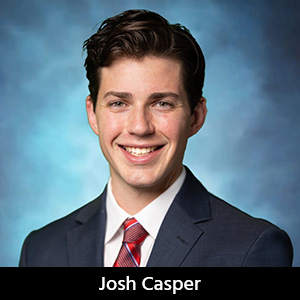
The push toward automation in electronics manufacturing has led to significant improvements in SMT and through-hole technology (THT) production. Today’s manufacturers are outfitted with precision pick-and-place machines, sophisticated inspection systems, and advanced solder deposition solutions. These investments reflect a broader industry trend toward automating high-value production tasks to boost efficiency, improve quality, and reduce headcount in a shrinking labor market. While the spotlight has rightly focused on automating SMT production, one crucial area remains woefully under-invested: materials storage and handling.
This oversight is particularly concerning given the critical role that materials management plays in the overall manufacturing process. Materials—such as SMT/THT components, bare boards, and solder paste—are the lifeblood of production. How they are stored, tracked, and deployed directly impacts the effectiveness of the entire operation. Here, we’ll explore the impact of material handling and how automating this area can significantly enhance productivity, reduce costs, and ensure quality in electronics manufacturing.
The Impact of Manual Materials Handling
Manual materials handling remains a significant bottleneck in many electronics manufacturing facilities. In traditional setups, components are stored on shelves or in bins, with warehouse employees responsible for manually retrieving and deploying them to the production line. This manual process leads to myriad issues.
First, manual component kitting is one of the more labor-intensive areas of the facility. Operators are tasked with manually moving from location to location and retrieving one part at a time. For argument’s sake, if an operator can pick a single part every minute (and that’s being very aggressive), a smaller 60-piece kit would take at least an hour to pick. Now, multiply that across all the jobs and a manufacturer could be pulling in a single eight-hour shift. How many employees are dedicated to just pulling and returning materials? The time spent locating and moving materials slows down the production process, significantly negating the benefits of advanced automation on the SMT line.
Another common issue in manual picking is component misplacement. When reels are stored on shelves and tied to a manual location, it is entirely dependent upon the operator to ensure they’re not only pulling the correct part, but also returning it to the correct location. It’s human nature to make these mistakes, but they can easily compound, leading to line stoppages due to a single missing component. Worse yet, having the automated placement equipment placing the wrong component on multiple PCBs creates re-work havoc because it was incorrectly put in a kit by the manual picking operation.
Manual handling often leads to inventory inaccuracies as well. Without real-time tracking and automated management, it’s easy for inventory levels to become misaligned with actual stock. This can result in overstocking, which ties up valuable space and capital, or stock outages, which can halt production and lead to costly emergency ordering. Component visibility is critical, especially in a world where component availability leaves much to be desired.
To read the rest of this article, which appeared in the October 2024 issue of SMT007 Magazine, click here.
Testimonial
"The I-Connect007 team is outstanding—kind, responsive, and a true marketing partner. Their design team created fresh, eye-catching ads, and their editorial support polished our content to let our brand shine. Thank you all! "
Sweeney Ng - CEE PCBSuggested Items
Defense Speak Interpreted: If CHIPS Cuts Back, What Happens to Electronics Packaging Funds?
09/02/2025 | Dennis Fritz -- Column: Defense Speak InterpretedIn my May column, I examined the topic of the CHIPS Act and its current status as a U.S. government program. I found that CHIPS activities continue, but some corporations have delayed or canceled them because of budget cuts or corporation-specific problems. However, CHIPS integrated circuits—mostly administered by the Department of Commerce—don’t fully drive the electronics interconnection activity being funded by the government. Let’s cover the progress/status of other programs:
Facing the Future: Challenges and Opportunities in Reshoring PCB Manufacturing
08/12/2025 | Prashant Patel -- Column: Facing the FutureFor decades, offshore manufacturing dominated the global electronics industry. The pursuit of cost efficiency, scalability, and access to vast labor markets made countries like China, Taiwan, and Vietnam attractive destinations for printed circuit board (PCB) production. But a seismic shift is underway, from geopolitical instability and supply chain disruptions to rising labor costs and national security concerns.
Automated Production Equipment and Manncorp Announce Strategic Partnership to Expand SMT Solutions for U.S. Electronics Manufacturers
08/06/2025 | Automated Production EquipmentAutomated Production Equipment (APE), a trusted supplier of high-performance soldering and rework systems, proudly announces a strategic partnership with Manncorp, a leading provider of Surface Mount Technology (SMT) production equipment. This collaboration brings together two industry leaders to deliver expanded, end-to-end SMT solutions to electronics manufacturers across North America.
KYZEN to Feature CYBERSOLV 141-K and KYZEN E5631J at SMTA Michigan Expo and Tech Forum
08/05/2025 | KYZEN'KYZEN, the global leader in innovative environmentally responsible cleaning chemistries, will exhibit at the SMTA Michigan Expo and Tech Forum, scheduled to take place Tuesday, August 19, 2025 at Laurel Manor in Livonia, Michigan. During the event, the KYZEN Clean Team will highlight precision aerosol cleaner CYBERSOLV 141-K and understencil cleaner KYZEN E5631J.
Global Citizenship: Chinese PCB Fabricators Will Remain an Important Part of the Supply Chain
08/06/2025 | Tom Yang -- Column: Global CitizenshipIn today’s hyperconnected electronics landscape, collaboration is no longer optional; it’s essential. No single country holds a monopoly on innovation, and no one company or country can go it alone. Electronics manufacturing is very much a global business, and this will not change, no matter how the tariffs and global trade winds are blowing. Whether you're a startup founder building your prototype, an aerospace engineer pushing the boundaries of performance, or a supply chain leader managing a complex global network, Chinese PCB fabricators have likely already touched your world.