-
- News
- Books
Featured Books
- pcb007 Magazine
Latest Issues
Current IssueFueling the Workforce Pipeline
We take a hard look at fueling the workforce pipeline, specifically at the early introduction of manufacturing concepts and business to young people in this issue of PCB007 Magazine.
Inner Layer Precision & Yields
In this issue, we examine the critical nature of building precisions into your inner layers and assessing their pass/fail status as early as possible. Whether it’s using automation to cut down on handling issues, identifying defects earlier, or replacing an old line...
Engineering Economics
The real cost to manufacture a PCB encompasses everything that goes into making the product: the materials and other value-added supplies, machine and personnel costs, and most importantly, your quality. A hard look at real costs seems wholly appropriate.
- Articles
- Columns
Search Console
- Links
- Media kit
||| MENU - pcb007 Magazine
BOOK EXCERPT: The Printed Circuit Designer’s Guide to... DFM Essentials, Chapter 2
November 14, 2024 | I-Connect007 Editorial TeamEstimated reading time: 1 minute
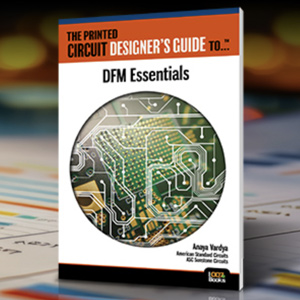
The Printed Circuit Designer’s Guide to... DFM Essentials
by Anaya Vardya, American Standard Circuits / ASC Sunstone Circuits
Chapter 2: Panelization
Panelization is the process of placing one or more PCBs on a manufacturing panel and incorporating features to assist manufacturing (such as tooling holes, fiducials, coupons, panel thieving, etc.). Panelization is one of the highest impact factors in the cost of a PCB.
The panel area available for circuit boards plus coupons is known as the usable area (Figure 2.1). Test coupons are added by the fabricator to the perimeter of the manufacturing panel outside the usable area. The number and type of coupons are based on the specs that the PCBs are being built to and requirements for controlled impedance. Coupons may sometimes further reduce the amount of a PCB panel that is available for the circuit boards. This is defined by the fabricator as required perimeter for coupons. This is typically about 1 inch or 25.4 mm and is a fixed area based on panel size. Panel utilization is measured as a percentage, defined by the total area for PCBs divided by the total panel area.
Cost-effective material utilization is defined by a target panel with greater than 75% panel utilization. Raw laminate is one of the primary cost constituents of a multilayer PCB. Optimizing panel structures around standard base materials while achieving maximum material utilization on one of the standard panel sizes can have a significant impact on multilayer board prices and deliveries. The three most preferred sizes in North America are 12x18 inches, 18x24 inches and 21x24 inches, with 18x24 inches being the most common. For special applications, other panel sizes can be provided. In Asia, typically the shops will process custom panel sizes in order to maximize utilization. The most effective cost per unit area processed is usually found with a larger panel size.
Visit the I-Connect007 library to continue reading The Printed Circuit Designer’s Guide to DFM Essentials.
Suggested Items
Transparent Electronics Market to Reach $2611 Million by 2030
01/31/2025 | BUSINESS WIREThe Global Transparent Electronics Market was valued at $963 Million in 2023 and is anticipated to reach $2611 Million by 2030, witnessing a CAGR of 15.4% during the forecast period 2024-2030.
Taiwan Earthquake Shows Shows Minimal Impact on Wafer Fabs, But Tightness in the TV Panel Supply May Worsen in 1Q25
01/21/2025 | TrendForceA magnitude 6.4 earthquake struck southern Taiwan, with its epicenter in Chiayi, at 12:17 AM on January 21, 2025. TrendForce’s preliminary assessment found that nearby wafer fabs had not suffered significant damage.
Würth Elektronik at PEDC 2025
01/14/2025 | Wurth ElektronikOn January 29 to 30, 2025, the Pan-European Electronics Design Conference (PEDC) will convene leading experts from industry and research in Vienna.
The Chemical Connection: Can Changing Spray Nozzles Improve My Etch Quality?
01/13/2025 | Don Ball -- Column: The Chemical ConnectionWhenever the need to improve etch quality due to tightening customer specifications arises, the inevitable question asked early on is, “Will going to a different type of nozzle or nozzle flow rate make my etch quality better?” Unfortunately, the answer is most likely, “Probably not.” (Sorry, folks.) So, why not?
Laser Photonics Propels R&D Efforts in PCB Depaneling
01/01/2025 | BUSINESS WIRELaser Photonics Corporation, a leading global developer of industrial laser systems for cleaning and other material processing applications, and its subsidiary, Control Micro Systems (CMS Laser), announced the expansion of their Printed Circuit Board (PCB) Depaneling technology development project for the electronics market.