Sayonara to the Last Standing Copper Foil Plant in North America
December 17, 2024 | Marcy LaRont, I-Connect007Estimated reading time: 4 minutes
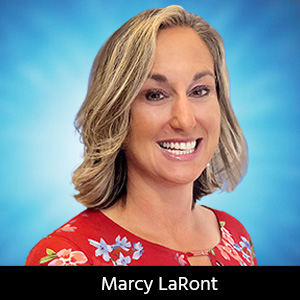
In July 2021, PCB007 Magazine published an interview with Michael Coll and Chris Stevens of Nippon Denkai about the new acquisition by Nippon Denkai of the last-standing ED foil manufacturer in North America. The plant in Augusta, Georgia, was formerly owned by Oak Mitsui, Inc. and had been purchased by Nippon Denkai the previous March, after which significant investment was made with the expectation of providing more jobs.
Many COVID-related shutdowns were still in effect. Copper prices were soaring, as was demand in the wake of the need for lithium-ion batteries for electric cars and massive projections for their growth. Copper foil suppliers for the PCB industry were working to allocate their supply between the PCB and EV industries.
The demand for copper was not isolated to just electronics. When asked about the pressure to supply industries outside of electronics, Chris Stevens responded, “As the only ED foil manufacturer in North America, we really feel that we have an obligation to the PCB market, which we have been supplying for over 40 years. We are spec’d into a lot of military, defense, and aerospace applications, and we know it is critical to continue supporting this business.”
It’s now the end of 2024 and the bottom has apparently fallen out. Nippon Denkai Ltd., plagued with financial difficulties reported to have been caused in part by the semiconductor shortage, a decline in the demand for smartphones, the enforcement of the U.S. Inflation Reduction Act, and the financial fallout from COVID amidst ever-increasing copper prices, recently filed for bankruptcy and civil rehabilitation proceedings. The company is dissolving its U.S. holdings and has announced the closure of the copper foil manufacturing plant in Georgia.
It is rarely a straight line to bankruptcy for any business and Nippon Denkai is no exception. Though the myriads of very real market challenges certainly adversely affected their business holdings, rarely are only market factors to blame for an organization’s financial demise, especially when that organization was positioned to capitalize on ridiculous market demand which should have more than made up for the high price of copper.
Poor decisions and organizational management may have played a part.
Nevertheless, the U.S. is now faced with the closure of the last standing copper foil manufacturing plant in North America serving the PCB fabrication industry and supporting many U.S. military and defense products.
How much will this matter? It will undoubtedly cause a ripple within the supply chain, mostly around the timing of negotiating new agreements with overseas copper foil suppliers and management of production output.
But amidst the backdrop of the CHIPS Act, and the drive to rebuild American manufacturing and secure the supply chain for products and applications that could put U.S. security at risk, the closure of this last U.S. plant right now feels a bit hard to believe. Who was minding the store? With all the government’s financial awards and strong statements of support for stateside electronics manufacturing, this certainly looks terrible. So, should the U.S. government step in and purchase the asset from Nippon Denkai, perhaps as part of the massive investment for the Printed Circuit Board Market Catalyst program?
American manufacturers and business owners who are already on tenterhooks about the future of American manufacturing and their role in it are wondering whether the government’s slow pace and inability to focus on anything but what is immediately in front of them makes them incapable of recognizing potentially important opportunities as they arise, even if largely symbolic, let alone taking advantage of them.
“We regret that our colleagues at Denkai are facing this situation,” said David Schild, executive director of the Printed Circuit Board Association of America. “Single points of failure in the microelectronic supply chain will have consequences for PCB manufacturers and related industries. With no more U.S. copper foil vendors, PCB manufacturers will have to qualify other vendors or find alternative materials. This will likely disrupt delivery of certain DoD programs of record as well as commercial customers supporting the nation’s critical infrastructure. DoD Industrial Base Policy needs to double down on domestic single-source/single-point failures in the microelectronics supply chain.”
If you are angry or frustrated at this news, I encourage you to reach out to your legislative representative, and advocacy groups like PCBAA and IPC.Visit them in Washington, D.C., and invite them to your site. They usually welcome the opportunity to visit with their constituents as a way to show they support business in their states. Advocacy staff at both IPC and PCBAA will help you do this.
This is the power we have collectively. It might be the only power we have left. No one is too small to get involved. No one’s business is unimportant. Don’t leave all the heavy lifting to the big guys who already work in advocacy. With something as important as this, it’s time to get involved. Don’t make excuses. Do more. Do something. The time is now, because it may be all that we have.
Today, we say “sayonara” to copper foil manufacturing in the U.S. and to the jobs attached to it. It feels a little like coal in our stockings, so here’s to better things in 2025 and beyond.
Testimonial
"In a year when every marketing dollar mattered, I chose to keep I-Connect007 in our 2025 plan. Their commitment to high-quality, insightful content aligns with Koh Young’s values and helps readers navigate a changing industry. "
Brent Fischthal - Koh YoungSuggested Items
50% Copper Tariffs, 100% Chip Uncertainty, and a Truce
08/19/2025 | Andy Shaughnessy, I-Connect007If you’re like me, tariffs were not on your radar screen until a few months ago, but now political rhetoric has turned to presidential action. Tariffs are front-page news with major developments coming directly from the Oval Office. These are not typical times. President Donald Trump campaigned on tariff reform, and he’s now busy revamping America’s tariff policy.
Global PCB Connections: Understanding the General Fabrication Process—A Designer’s Hidden Advantage
08/14/2025 | Markus Voeltz -- Column: Global PCB ConnectionsDesigners don’t need to become fabricators, but understanding the basics of PCB fabrication can save you time, money, and frustration. The more you understand what’s happening on the shop floor, the better you’ll be able to prevent downstream issues. As you move into more advanced designs like HDI, flex circuits, stacked vias, and embedded components, this foundational knowledge becomes even more critical. Remember: the fabricator is your partner.
MKS’ Atotech to Participate in IPCA Electronics Expo 2025
08/11/2025 | AtotechMKS Inc., a global provider of enabling technologies that transform our world, announced that its strategic brands ESI® (laser systems) and Atotech® (process chemicals, equipment, software, and services) will showcase their latest range of leading manufacturing solutions for printed circuit board (PCB) and package substrate manufacturing at the upcoming 17th IPCA Show to be held at Pragati Maidan, New Delhi from August 21-23, 2025.
MKS Showcases Next-generation PCB Manufacturing Solutions at the Thailand Electronics Circuit Asia 2025
08/06/2025 | MKS Instruments, Inc.MKS Inc, a global provider of enabling technologies that transform our world, today announced its participation in Thailand Electronics Circuit Asia 2025 (THECA 2025), taking place August 20–22 at BITEC in Bangkok.
Point2 Technology, Foxconn Interconnect Technology Partner to Revolutionize AI Cluster Scalability with Terabit-Speed Interconnect
08/06/2025 | BUSINESS WIREPoint2 Technology, a leading provider of ultra-low-power, low-latency mixed-signal SoC solutions for multi-terabit interconnect, and Foxconn Interconnect Technology (FIT), a global leader in precision interconnect solutions, have signed a Memorandum of Understanding (MOU) to accelerate the commercialization of next-generation Active RF Cable (ARC) and Near Pluggable e-Tube (NPE) solutions.